Simcenter STAR-CCM+ 2019.3: Simulate In-Cylinder Combustion
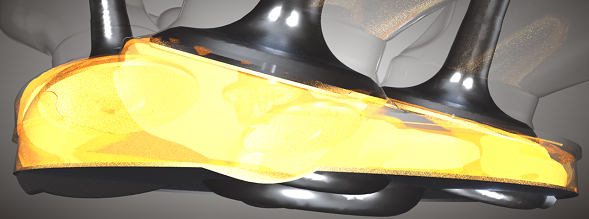
Undoubtedly, the internal combustion engine is one of the greatest inventions of all time. Back in the late 19th century, Nikolaus A. Otto managed to build an internal combustion engine based on principles that are the foundation of the four-stroke, spark-ignited gasoline engine that you find in many of today’s passenger cars. Over time, engine technology has evolved, as have the methods for developing engines. I wonder if Otto and the other pioneers ever could have imagined being able to investigate different operating strategies using a digital engine instead of spending time building a real engine? And, would they have imagined being able to visualize how the flame in the combustion chamber is propagating?

With Simcenter STAR-CCM+ 2019.3, engine developers will be able to simulate combustion in gasoline direct-injection (GDI) spark-ignition engines and visualize the combustion process using Simcenter STAR-CCM+’s advanced post-processing capabilities, for example by visualizing the flame front as shown in Figure 1.
The combustion model that we are introducing is the well-known ECFM-3Z (Extended Coherent Flame Model – Three Zones) model [1], which is the most widely used combustion model for in-cylinder simulations. Our journey with the ECFM-3Z model started years ago, as it was introduced into STAR-CD in the mid-2000s. Now that we bring the ECFM-3Z model to Simcenter STAR-CCM+ we leverage the experience on implementation and application that was gained over all those years.
What makes the ECFM-3Z model so popular? There are several key factors contributing to its success: (a) high computational efficiency; (b) robustness; (c) it is applicable to both premixed and non-premixed turbulent combustion. The model is providing a sub-grid description of the mixing and combustion processes, where the turbulence timescale enters the equations describing mixing and combustion, and that is important when modeling turbulent combustion in engines.

Let’s have a look at how this model performs in Simcenter STAR-CCM+ with a simulation of a four-cylinder GDI production engine. Figure 2 compares the simulated pressure traces with the experimental ones for a low load operating condition (3 bar IMEP), a part load operating condition (8.3 bar IMEP) and a high load operating condition (15 bar IMEP). The high load operating condition was simulated first, and all model parameters were left unchanged when simulating the two other load points. Overall, the pressure is well-predicted and the small discrepancies can be attributed to slight uncertainties in fueling and spark timing.
One way to understand the flame propagation process is to investigate the temperature evolution in the combustion chamber. To this end, we can make use of the built-in advanced post-processing capabilities of Simcenter STAR-CCM+ and look at the development of the temperature field from two different views. In Animation 1 we are looking down at a horizontal cut-plane beneath the spark-plug and Animation 2 shows the temperature evolution for a vertical cut-plane across the spark-plug for the high load operating condition. As expected, the flame is propagating from the spark-plug toward the walls. How the flame propagates through the combustion chamber depends on the flow pattern, turbulence, and how homogeneous the fuel-air mixture is, just to name a few key factors. Through visualization it is possible to explain the behavior of a certain operating strategy and combustion chamber geometry, which is of great value during combustion system development and optimization.
So, remember to download Simcenter STAR-CCM+ 2019.3 when released to take advantage of the new in-cylinder combustion simulation capabilities.
Watch our recent on-demand webinar on in-cylinder combustion and validation here.
Read more about the Simcenter STAR-CCM+ In-Cylinder Solution here.
Acknowledgment The experimental data was obtained from the DYNAMO (Dynamic Analysis Modelling and Optimisation of GDI Engines) project which has been partially funded by the Advanced Propulsion Centre, UK. Project partners are hereby acknowledged.
[1] O. Colin and A. Benkenida, Oil & Gas Science and Technology – Rev. IFP, Vol. 59 (2004), 6 pp. 593-609.
Comments
Comments are closed.