Simcenter STAR-CCM+ 2206 released! What’s new?
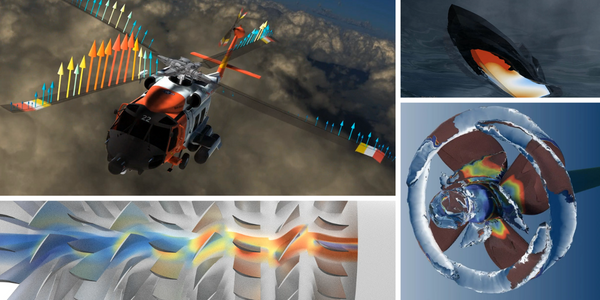
Boost your ability to model the complexity of multi-physics Computational Fluid Dynamics (CFD) applications and explore engineering possibilities. Go faster with innovative simulation technology ranging from intelligent and tailored automated workflows to integrated cloud-based computation. Simcenter STAR-CCM+ 2206 comes with a host of exciting new capabilities.
Learn how to use Support Center
New enhancements in Simcenter STAR-CCM+ are aimed at helping you:
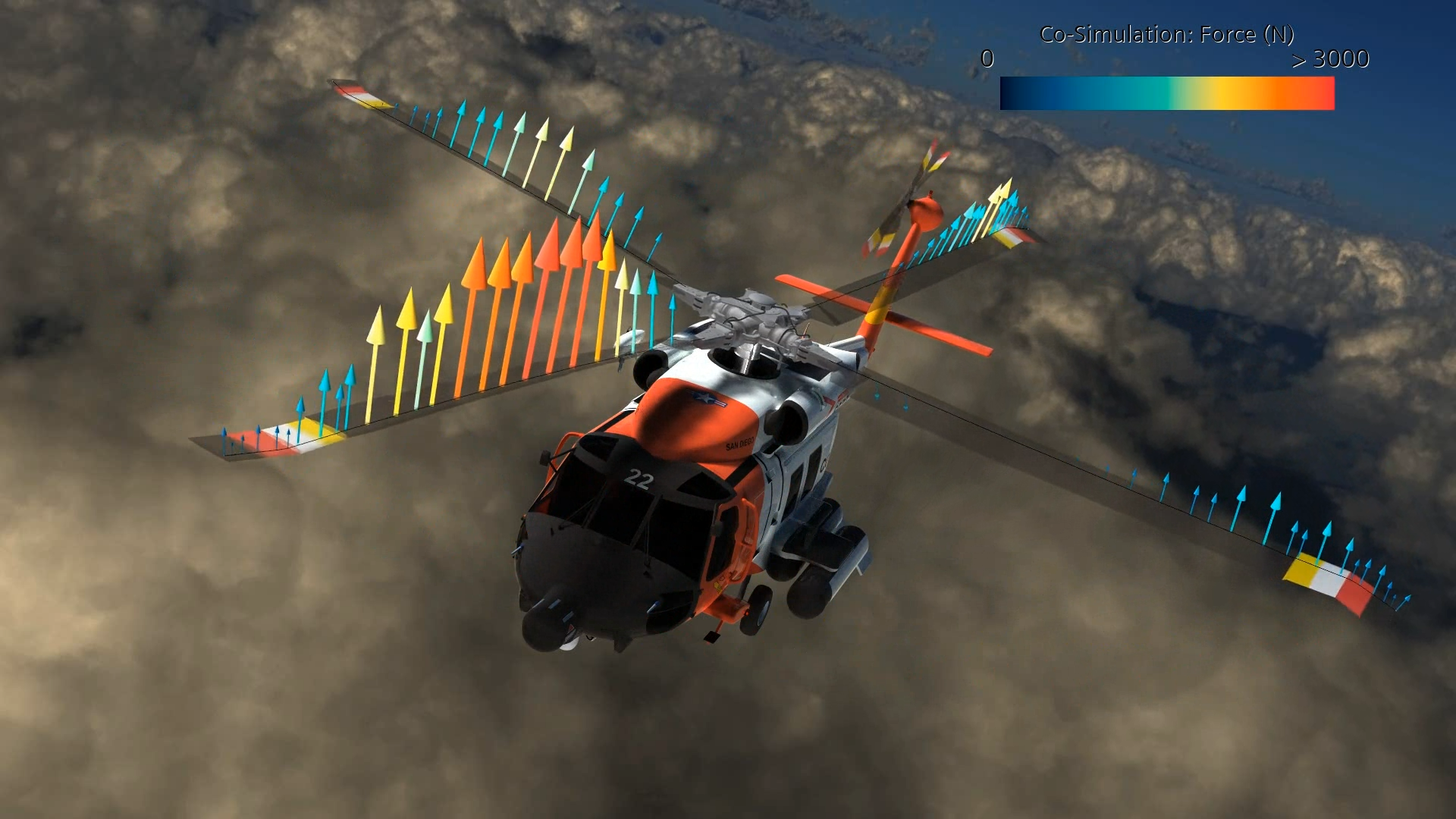
Model the complexity
Run high-fidelity aeroelastic simulations for rotor blades faster with an automated workflow
Applications such as helicopters, urban air mobility vehicles, and wind turbines heavily rely on accurate predictions of the complex interaction between aerodynamics forces and structural responses of their rotor blades. Hence, to increase the performance of those rotors while reducing vibration and noise, high-fidelity aeroelastic simulations are a key enabler for Computational Fluid Dynamics (CFD) engineers.
Simcenter STAR-CCM+ 2206 offers a fully automated rotor blade aeroelasticity workflow that provides a high-fidelity solution with minimum user effort. The new workflow is automatically linking and mapping to all common industry-standard rotor blade structural mechanics solvers, such as RCAS, CAMRAD II, DYMORE, or Flightlab with the ability to adapt to other software tools.
In a file-based coupling, aerodynamic forces and moments from the blades stemming from transient aerodynamic simulations are automatically mapped to a beam representation throughout a full rotation. The structure dynamics solver in turn computes elastic blade deformations under those loads. The co-simulation autonomously iterates until the overall system is converged for both the structure and flow field enabling engineers to easily gain insights into the complex aeroelastic behavior of rotors.
Get rapid and convenient insight in thermoacoustic stability of combustion systems
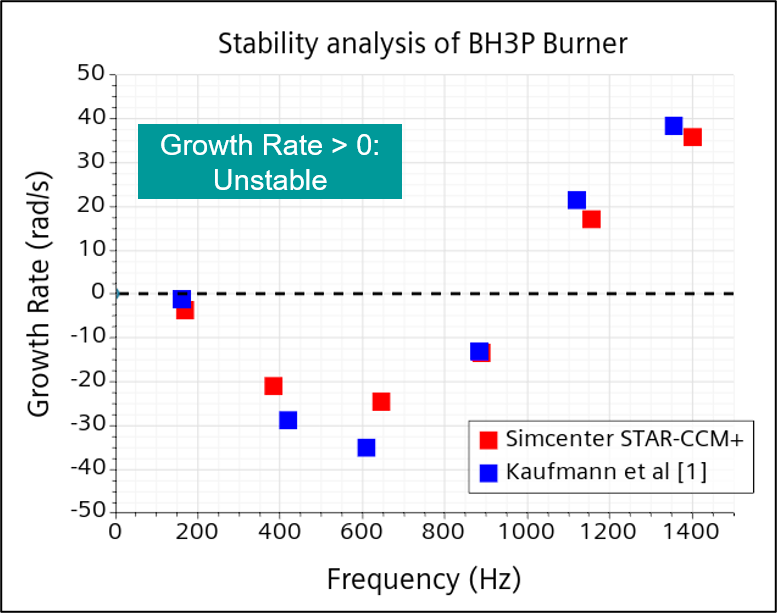
We consider thermoacoustics the coupling between pressure and heat release oscillations. This phenomenon continues to be a challenging design consideration especially as the use of Hydrogen extends in the face of tightened emissions requirements.
Hydrogen enrichment has been reported to shift regions of thermoacoustic instabilities to lower equivalence ratios and flame temperatures. This implies that a gas turbine combustor that is dynamically stable at a given equivalence ratio or flame temperature may be rendered dynamically unstable and vice versa as a result of hydrogen addition.
With Simcenter STAR-CCM+ 2206, we introduce an acoustic modal solver with the thermoacoustic n-tau model. This solver delivers engineers a rapid and convenient insight in thermoacoustic stability of the combustion systems. The approach avoids the need to export flow solutions to external tools for further analysis. Indeed, we can easily execute the modal solver as a post-processing step using the solution field from steady-state RANS simulations.
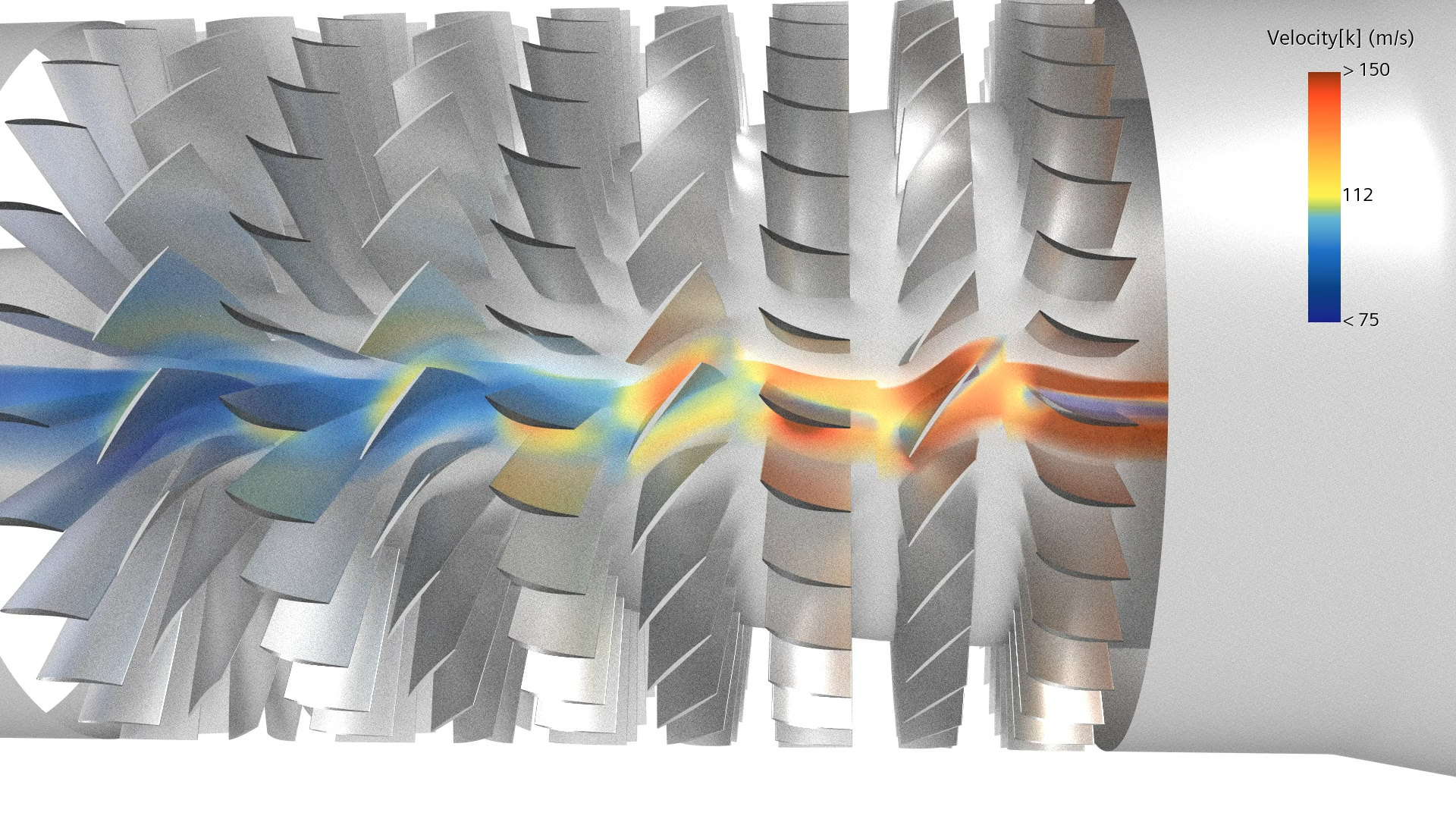
Explore the possibilities
Quickly explore performance maps for rotating machines, propellers, airfoils, and alike
Many applications such as airfoils or rotating machines, like pumps, compressors, or propellers all share a sudden nonlinear response of their performance metrics like lift, drag, and efficiency under the variation of a critical operating parameter, such as the angle of attack or the mass flow throughput.
Identifying those critical turning points in performance maps is one of the most important engineering tasks to ensure safe and reliable operation of such systems. However, carrying out required performance sweeps to find the peak lift of an airfoil or generating the speed lines for rotating machinery, while essential, all traditionally come at a high price. Even if sweeps can generally be automated, narrowing down those stalling and choking points, with the required level of precision, and under various operating conditions can be a very time-consuming job. Both in terms of engineering and computational time.
With the new smart sweep feature in Simcenter STAR-CCM+ 2206, you can now:
- automate smarter
- faster
- and more efficient design sweeps
for applications that need to capture those critical turning points in performance maps.
Fully embedded into design manager, the smart sweep automatically adapts the stepping parameter to narrow in on the target. The sweep autonomously bisects the stepping parameter to resolve the sweep in the area of interest in the parameter space e.g., use bisecting to detect the onset of compressor surge. Stopping criteria based on response values can be used to avoid infeasible cases. And, to further speed up the time to solution and increase convergence robustness, previous design results can be used for initialization of subsequent sweep points in the study.
Thanks to those smart sweeps tackling sophisticated industry-related exploration campaigns and the simulation-based creation of accurate performance maps for rotating machines, propeller curves, airfoil stall angle, etc. has never been easier, more precise, and yet faster.
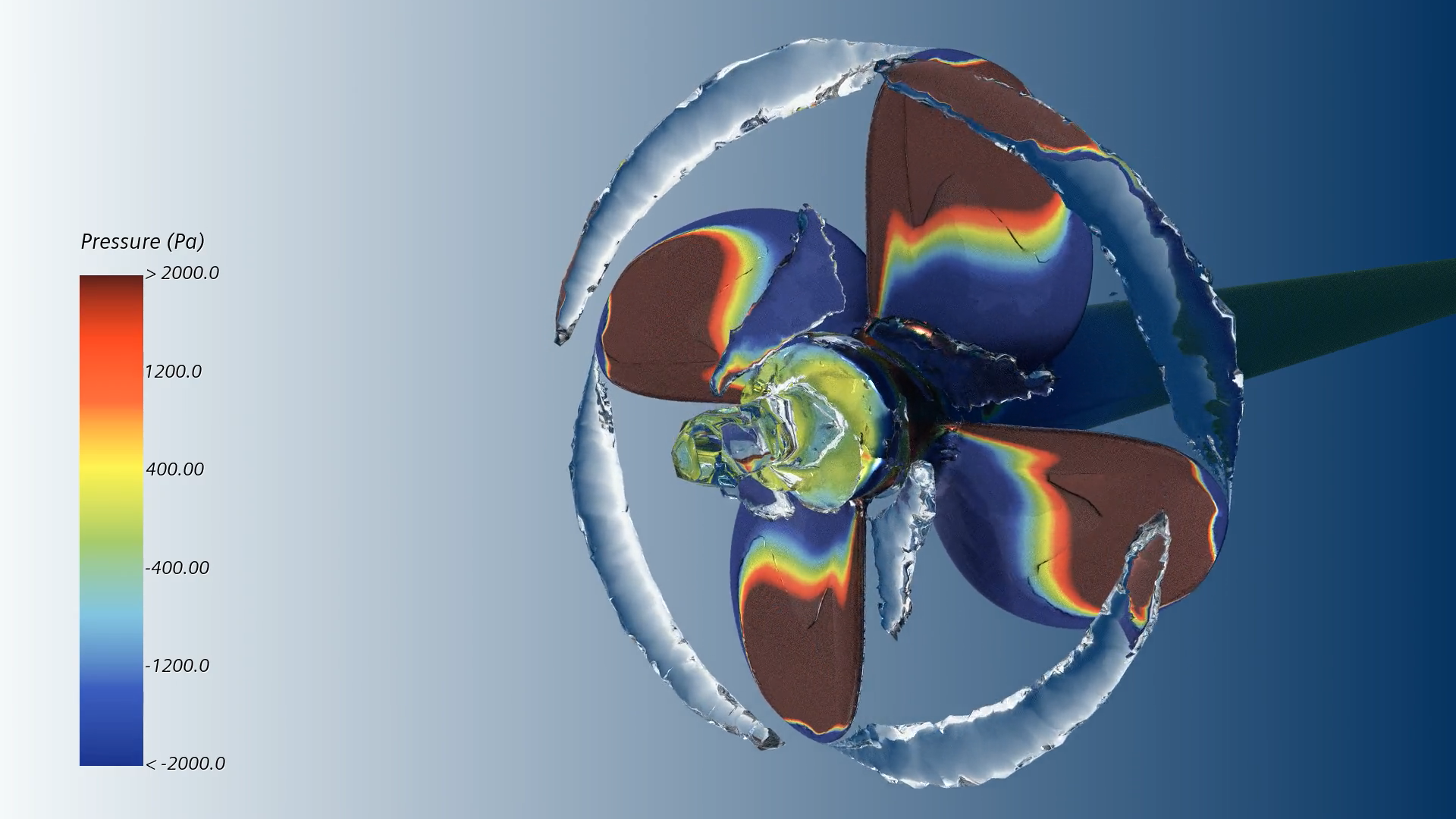
Go faster
Seamlessly leverage the power of symmetry with Idealization Transforms for data mappers
Ever since smart simulation engineers have been leveraging symmetries to reduce the computational effort and speed up the time to solution without compromising simulation fidelity. And despite increasing availability of high-performance compute power such smart leveraging of symmetry in an engineering problem will always remain a key to time and cost-efficient engineering.
However, even if the symmetry assumption is valid, running idealized models such as:
- a 2D or 3D sector
- an axisymmetric representation
- or a half model
come with a challenge when they are required for subsequent usage.
For idealizations to feed full configuration simulations as an initial condition, a boundary condition or in a co-simulation, the required mapping of data, that ensure the correct transformations from idealized to full model used to be a time-consuming and error-prone procedure.
With the Idealization transforms for data mappers in Simcenter STAR-CCM+ 2206, we now enable engineers to go significantly faster creating full-configuration solution from idealized models through easy-to-use data mapper transforms. Without any user intervention required, Simcenter STAR-CCM+ automatically creates respective Idealization transforms, whenever an idealization is introduced in the setup. For example, when a part is meshed as two-dimensional when a periodic contact or interface is introduced, or a half model is created, Simcenter STAR-CCM+ will immediately create a periodic, extrusion, or symmetry idealization transform respectively. Even compositions of several transforms are recognized.
Those idealization transforms allow users to map and interpolate data from source to target with a single click. This enables engineers to go faster from idealized to full configurations to seamlessly leverage the power of symmetry.
Instant access to practically unlimited compute, direct from your desktop
Running CFD simulations on the cloud offers increased flexibility and scalability over on-premise hardware, with on-demand access and unlimited capacity.
However, setting up and accessing the cloud using 3rd party providers often:
- requires significant expertise in cloud and HPC technologies
- and interrupts existing workflows.
With Simcenter Cloud HPC, we are offering our users a seamless experience for simulation in the cloud. We run jobs on Amazon Web Services cloud infrastructure, configured and managed by Siemens, directly from within Simcenter STAR-CCM+. We don’t need additional configuration or expertise to access this all-in-one solution. This gives you the freedom to instantly scale up and down as needed to:
- go faster
- meet deadlines
- or explore more designs.
With Simcenter STAR-CCM+ 2206, we release the first public preview of Simcenter Cloud HPC. This allows our customers to try the service for free and experience the power of CFD in the cloud, delivered by Siemens.
Please contact your account representative to find out more.
Effectively template Vehicle Thermal Simulations with parts-based Dual Stream Heat Exchangers
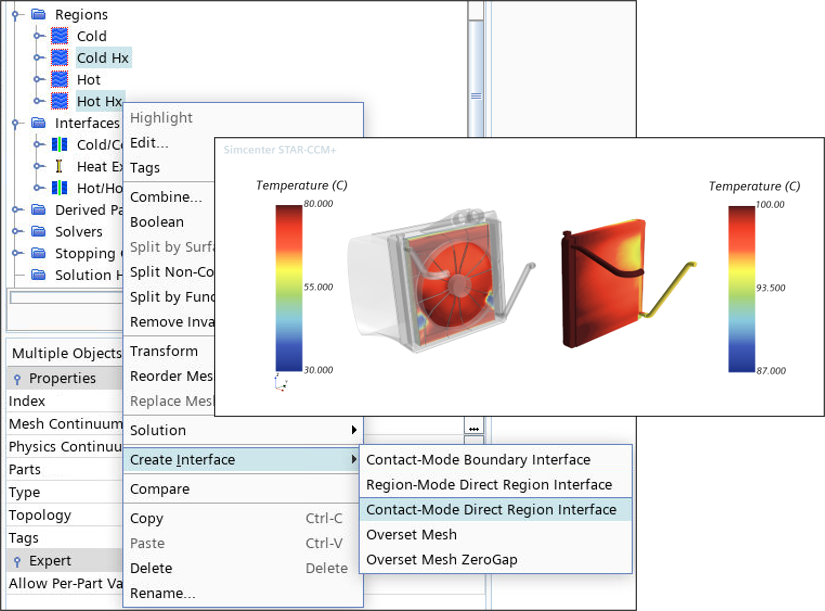
Vehicle thermal management Computational Fluid Dynamics (CFD) simulations require:
- the handling of very complex assemblies
- while modeling heat-transfer physics on hundreds of parts and multiple heat-exchangers with high fidelity.
Enabling workflow automation and templating is, therefore, a crucial element for a quick, efficient, and consistent VTM simulation setup.
By introducing the Parts-based dual-stream heat exchanger option for the actual Flow Dual Stream heat exchanger model, Simcenter STAR-CCM+ 2206 now enables engineers to:
- easily handle vehicle cases that have variable number of heat exchangers
- and significantly simplifying templated workflows.
The part-based profile allows users to only have one region for all cold Heat Exchanger parts, one for each hot Heat Exchanger parts, one for the cold fluid domain and, one for the hot fluid domain while customizing heat exchanger inputs on a per part basis.
This results in a significant reduction of the number of regions, boundary conditions, and interfaces. And hence simplifies the workflow of templating with arbitrary numbers of heat exchangers.
As such the new parts-based actual flow dual-stream heat exchanger model and report enable engineers to go faster in workflow automation for Vehicle Thermal Management solutions.
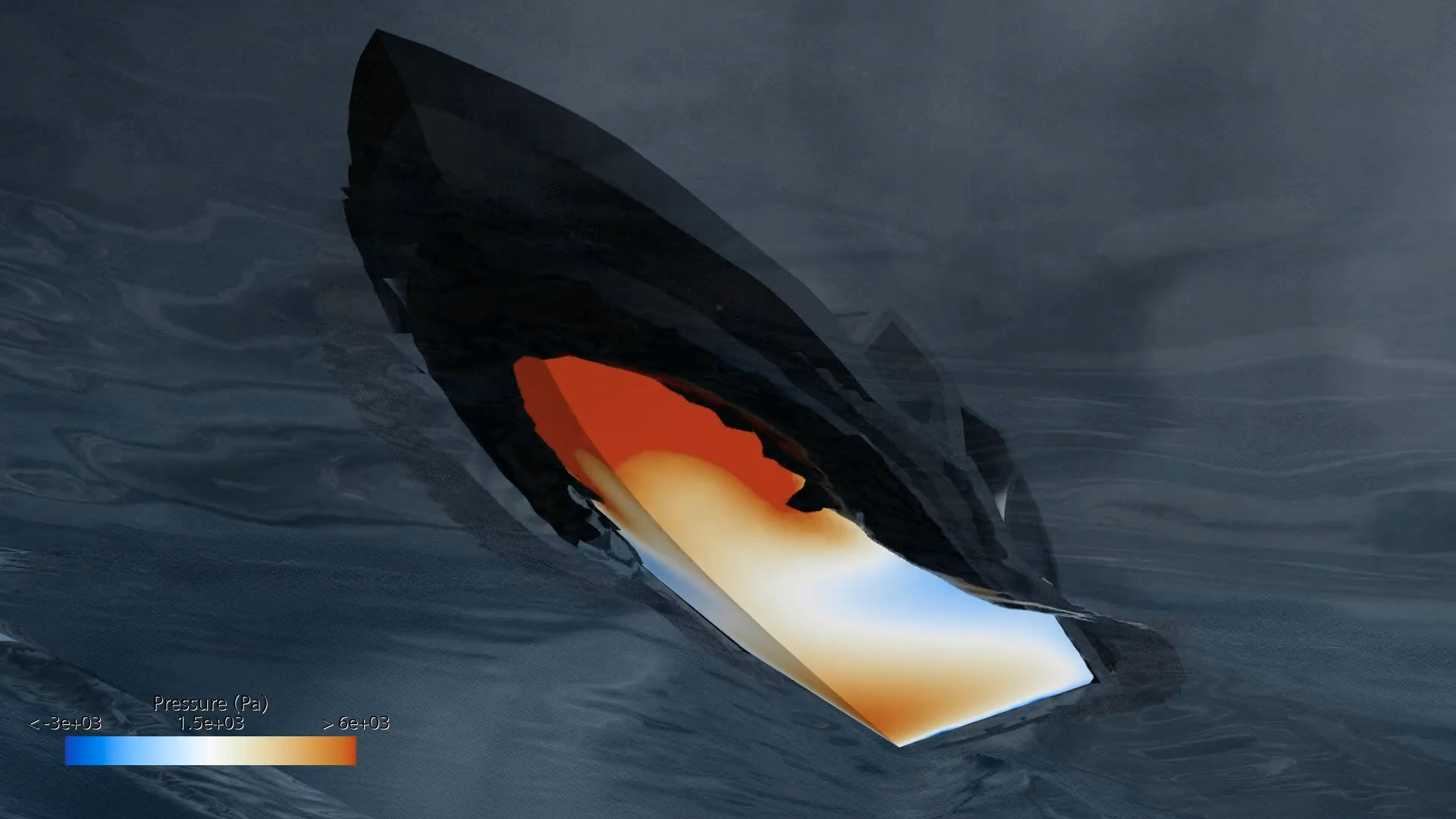
Stay integrated
Collaborate effectively on multidisciplinary applications through Simcenter data exchange
For engineers to collaborate effectively on multidisciplinary applications, being able to transfer results quickly, easily, and reliably from CFD to mechanical and multi-body simulations is crucial.
With Simcenter STAR-CCM+ 2206, we introduce an efficient data exchange between Simcenter STAR-CCM+ and Simcenter 3D by introducing a common data format. As the standardized Simcenter data format, the SCD5 file provides a robust and efficient file exchange of solution data between Simcenter products.
This feature caters for any application where thermal and aerodynamic loads are critical to mechanical performance. The new capability allows the rapid exchange of volumetric temperature distributions on structures and pressure distribution on surfaces. We support exchanges of both transient and steady simulation results. Complimentary to CGNS exchanges of CFD data the Simcenter data format better accommodates the mesh and element conventions of finite element solvers.
This new feature allows engineers across domains to:
- stay integrated in one simulation environment
- and model the complexity of today’s multiphysics-affected products faster than ever.
These are just a few highlights in Simcenter STAR-CCM+ 2206. Those features will enable you to design better products faster than ever, turning today’s engineering complexity into a competitive advantage.