Simcenter Testlab 2019.1: NVH Synthesis component-based TPA
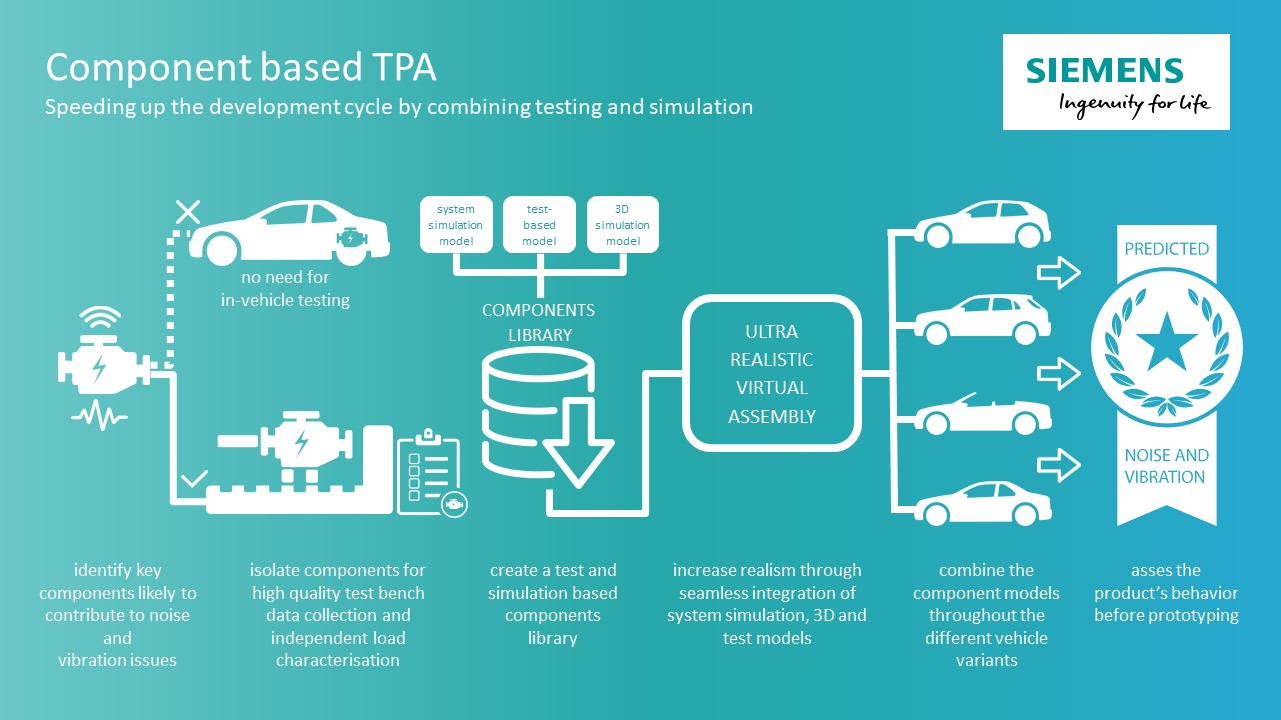
Over the past few decades, the automotive world has changed. Striving for lower to zero-emission vehicles, reaching higher safety levels for drivers and passengers, and taking significant steps towards autonomous driving have been a never-ending development trend in the recent years. Whatever design innovation, steps forward, and changes in our mobility habits, the automotive industry considers driving experience, subjective feeling, and passenger comfort as being at the center of their design choices.
The optimization of fuel efficiency, for example, must now be balanced with comfort and safety. Noise and vibration, as well as brand characteristics must be respected to keep the branded signature of the vehicle. For this, many noise and vibration testing techniques are now being explored to optimize the sound of each and every component of the vehicle.

Classical TPA – definition
Transfer Path Analysis (TPA) is a well-known technique that has been applied for years in all types of industries. TPA allows us to understand the important dynamic paths in a source-receiver system that generates vibration or sound. TPA is a standard troubleshooting tool, which typically uses a test-based approach, that allows us to pinpoint the weak points in a complete structure—such as a vehicle, once it is completely assembled. We could, for example, define if the critical noise contributor of a car is the front suspension top right side or the powertrain roll restrictor mount, or maybe whether it is a critical combination of both.

Classical TPA – limitation
In a TPA environment, the loads that are calculated are directly linked and dependent on the vehicle boundary conditions. A change in the stiffness of the vehicle body on the suspension input point would mean that the calculated loads flowing at that point need to be re-evaluated. The characteristic of the interface point is directly involved in the calculation process, and the calculated loads are no longer only component characteristics.
However, in a very competitive world with constant evolution, more vehicle variants must be developed in shorter times and with a reduced availability of prototype vehicles, making this classical TPA approach less practical. But the capability of predicting noise contribution of vehicle components early in the development process is a major challenge. It would allow engineers to set realistic system design targets early on and would allow them to avoid costly and time-consuming design iterations. This is why engineers are currently seeking for new technologies that would enable full vehicle noise predictions from individual component models derived from test bench or in-situ measurements.
In order to keep the complete vehicle NVH performance under control, designers want to cascade the targets down to the component instead, fixing, for example, expected loads coming out of the HVAC or the steering system. They would then even complete powertrain, independently from the rest of the vehicle body. This is where the component-based TPA approach comes in.

Component-based TPA – definition
Component-based TPA is an approach that allows engineers to identify independent structure-borne source loads, combining these with vehicle noise transfer functions to predict interior noise as perceived by driver and passengers.
The difference between classical TPA an component-based TPA lies in the forces that are evaluated:
- “Classical TPA” Contact Forces are forces at the interface to the receiver system generated from the source system. The force is dependent on the interaction of the source-receiver system.
- “Component based TPA” Blocked Forces are forces generated by the source system, which are unaffected by the presence of any other component or receiver system; sometimes referred to as independent loads of the source.
The resulting independent loads are converted to contact forces using Frequency Based Substructuring (FBS). All independent sources are combined, and the total vehicle noise is evaluated numerically. By applying the methodology on time domain data, auralization can be done and continuous control on acoustic quality can be ensured.

Component-based TPA – The added value
Testlab 2019.1 NVH Synthesis component-based TPA prioritizes the quality of the data in every instance of the process. The data acquired from the test-benches are high-quality, which results in high-quality loads in the components library and further into creating hyper-realistic virtual models of the product true to any consequent prototyping. Not just that, the Simcenter solutions not only offer testing capabilities, but seamlessly combine with the Simcenter 3D simulation suite and Amesim system simulation suite, offering you an all-round solution for component-based TPA and virtual assembly.
Component-based TPA opens the door to a wide range of applications:
- Target setting during the development cycle: a specific maximum load target can be defined per component independent of the possible cross coupling effect. Set right targets setting at different sub-systems, for different departments or suppliers
- Keep control of your NVH target at each vehicle development step: Combine the bench-measured or simulation result blocked forces with FBS and target FRF to predict the total noise. Make sure different systems work well together
- Direct evaluation of one single component variant over multiple body platform. Blocked forces are independent from boundary conditions

Component-based TPA – Implement it
- Do you want help and support when starting to use the NVH synthesis component-based TPA? Our Simcenter Engineering and consulting division can support and ensure technology transfer at the end of the project. The process requires the highest test data quality and consistency: make use of Simcenter Testlab TPA and dedicated excitation hardware to get it right.
- For a more technical background, you can have look at our knowledge post here.
- Indirect measurement of blocked forces has its ISO norm. Click here for more information.
- Interested in more TPA background? Discover why TPA is not an established technology