Simulate the Real World Using Multiphysics
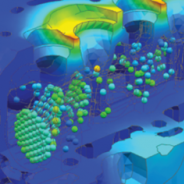
Product behavior in the real world is influenced simultaneously by multiple domains of physics, making multiphysics analysis a growing necessity for computer-aided engineering (CAE).
Multiphysics analysis allows you to not only predict how a design will perform in actuality, but to compare different design variants without the time-consuming and costly process of creating multiple physical models and then testing them.
Multiphysics analysis also reduces post-production failures, further saving costs from warranty repairs. This is thanks to more accurate predictions of how the product will function under stress and other various conditions.
Say you’re an engineer who is developing a fuel tank for a car. Fluid dynamics dictates how fuel inside the tank sloshes, which then creates hydrodynamic forces that in turn deform the tank. You have to know how the tank will react to different driving conditions and fuel levels. Transient-fluid dynamic analysis determines fluid velocities and pressures that result from vehicle motion. These are then mapped to a structural-analysis model to identify the magnitude and location of the corresponding structural deformation.
However, the process to couple computational fluid dynamics (CFD) analysis of the fuel with the structural analysis required to understand how the tank structure responds is extremely challenging with traditional CAE tools. In order to solve these problems, you need a modern CAE environment that is multiphysics capable. A modern CAE environment should allow for the seamless flow of information from one domain to another, while empowering you to manipulate native geometry and evaluate how changes affect product performance, yet also be simple enough to use that you don’t have to be an expert in order to do so.
Multiphysics analysis is complicated, however, and when you factor in the increasing product complexity of, say, a car—which has to meet both automotive industry standards for fuel efficiency and reduced emissions along with consumer demands—time does become a concern. Parallel processing solves this problem; it decreases the amount of time it takes to solve for various physical phenomena by dividing the numerical solution into discrete packages that are then solved in parallel.
To read more about multiphysics analysis and for other examples of how it’s used, see the white paper “Multiphysics Analysis: Promoting Innovation in the Product Development Process.”
Amy