Smoother gear operation with SPH fluid injection
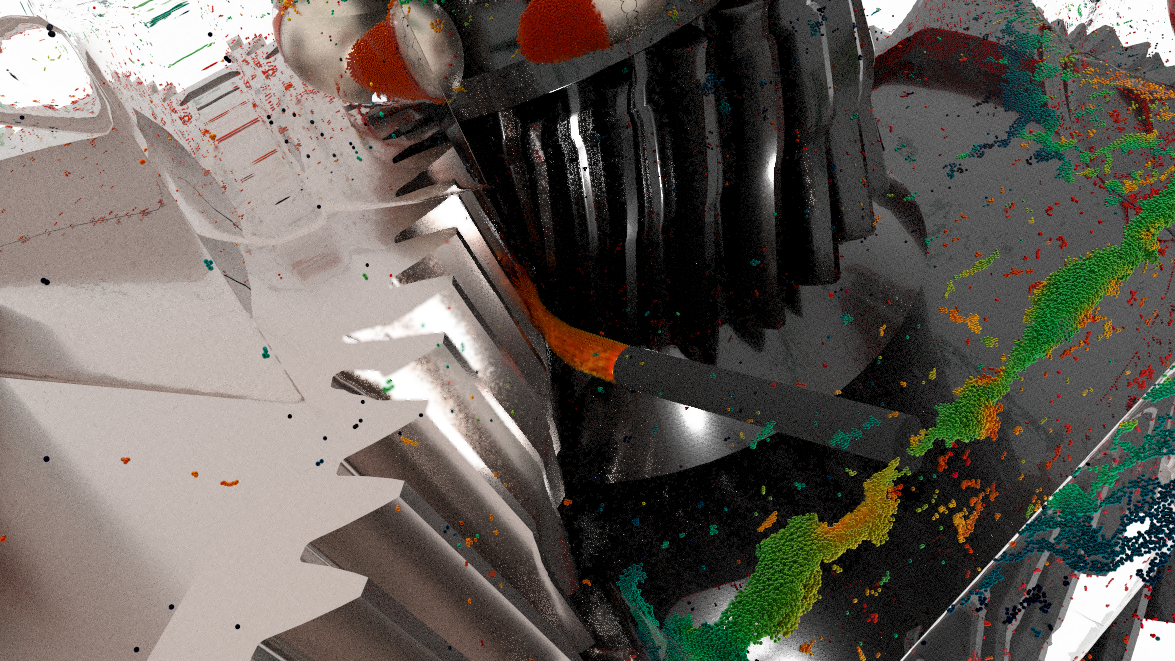
Smoother lubrication with oil injection
The injection of oil offers several advantages over traditional oil bath lubrication for gearboxes. Oil injection allows for a significant decrease in oil consumption while achieving improved accuracy compared to an oil bath. Indeed, the injection process enables pinpoint control over the lubricant delivery, ensuring optimal lubrication at critical locations. Injecting oil precisely where needed minimizes waste, resulting in lower overall oil consumption.
However, lubrication by injection requires a higher level of knowledge of the flow pattern and system dynamics. Moreover, it usually demands higher initial investment compared to oil bath systems. Therefore, detailed engineering insights in the early design phase of a gearbox are critical to realize optimum injector positioning and injection strategies.
A viable tool to cope with this challenge early in the design of a gearbox lubrication system is Smoothed-Particle Hydrodynamics (SPH).
Shifting gears with SPH fluid injection
Simcenter STAR-CCM+ 2402 marked the “big entrance” of the SPH technology into one single integrated CFD environment. In the previous 2402 release, the Smoothed-Particle Hydrodynamics (SPH) solver enabled targeting powertrain lubrication with oil bath applications.
In Simcenter STAR-CCM+ 2406, we took the term “entrance of SPH” more literally: with the introduction of inlets for SPH, you can now tackle powertrain lubrication through injection. Specifically, you now have the option to inject oil by imposing either its velocity or mass flow. Additionally, you can impose a constant oil distribution or simulate a time evolution, such as during the start-up of the lubrication system.
By those means Simcenter STAR-CCM+ 2406 now enables you to visualize the lubricant flow within your gearbox using SPH with inlet boundary conditions. This allows you to validate the precise direction of the oil on gear elements, ensuring efficient and reliable lubrication.
Stay integrated with the power of Simcenter STAR-CCM+ as a platform
Thanks to the integration of SPH into our flagship Multiphysics platform, you can now harness Simcenter STAR-CCM+’s full suite of quantitative data analytics capabilities in conjunction with smoothed-particle hydrodynamics. For gearboxes, you can e.g. monitor churning losses by looking at the forces and torque evolutions throughout your simulation.
On that note, one additional enhancement for SPH in Simcenter STAR-CCM+ 2406 is for the torque evolution. The report and plot of the torque no longer depend on the surface mesh resolution. Even if you have a coarse surface mesh representation of your geometries, it won’t impact the precision of the torque evolution anymore. This ensures accurate results regardless of the surface mesh details.
More applications with rotating injectors
In the example above, you saw a static SPH fluid injection. Static inlets are commonly used when the flow entering the domain is not influenced by rotation. With Simcenter STAR-CCM+ 2406, you can also set up a rotating inlet boundary condition. In injection lubrication systems, rotating injectors are commonly used to deliver the oil lubricant to moving parts such as gears or bearings. The rotating inlet condition ensures that the lubricant flow enters the domain with the desired rotational motion. Properly modeling this behavior is crucial for accurate simulations of powertrain lubrication performance.
In this animation, we see the application of a simplified e-machine lubrication system. Using SPH for this application allows to easily monitor where the lubricant oil goes with a simple workflow compared to finite-volume models.
Other applications become also reachable in this new version thanks to the addition of inlet boundary conditions. You can start to model vehicle water runoff or oil leakage applications where you look at where the liquid (water or oil) goes on/in the vehicle. You can observe how the liquid spreads over different parts of the vehicle, where it accumulates, and interacts with other components. While these applications are now feasible, it must be noted that some features are still missing for higher fidelity simulation such as the surface tension model that we are currently working on.
To mesh or not to mesh – revisited
It’s been the fundamental question since the initial introduction of SPH: To mesh or not to mesh! As for the previous release, SPH offers distinct advantages over other multiphase models for target applications. Traditional CFD simulations often require cleaning the CAD and creating a volume mesh, which can be time-consuming and complex for gearbox or E-machine applications. SPH eliminates this step entirely. Instead of relying on a volume mesh, it operates directly on particles distributed throughout the computational domain. Users benefit from a more seamless experience. SPH in Simcenter STAR-CCM+ combines user-friendly workflows, CAD integration, geometry flexibility, and robust motion handling.
Furthermore, an industrial gearbox can be simulated with SPH in about 12 minutes. Thus, for early design screenings, the SPH method is ideal to be used with the Design Manager for design exploration to eliminate quickly and effortlessly low-performance design. If your objective is to visualize oil distribution within the gearbox and monitor the churning losses, SPH is the best candidate for this application.
However, if air significantly affects the oil, or if you need to model spray inlets or look at heat transfer, or if you need to model the mist (gas and liquid mix) or to model phase change or electromagnetics or other complex physics, we recommend using finite-volume multiphase models which are more suited for the highest accuracy.
SPH and finite volume methods complement each other, and it always depends on the scope of your applications and the required level of fidelity to make the proper choice of the model to use.
In conclusion, while the SPH technology has already made a significant entrance in the last release, ensuring robust and well-defined inlet conditions is essential for maximizing its potential. By carefully setting up these boundaries, engineers can harness the power of SPH and explore engineering possibilities that turn complexity into a competitive advantage.
Stay tuned! This just one new feature of Simcenter STAR-CCM+ release 2406, out since the 3rd of July!