The 5 challenges affecting electric vehicle design and development
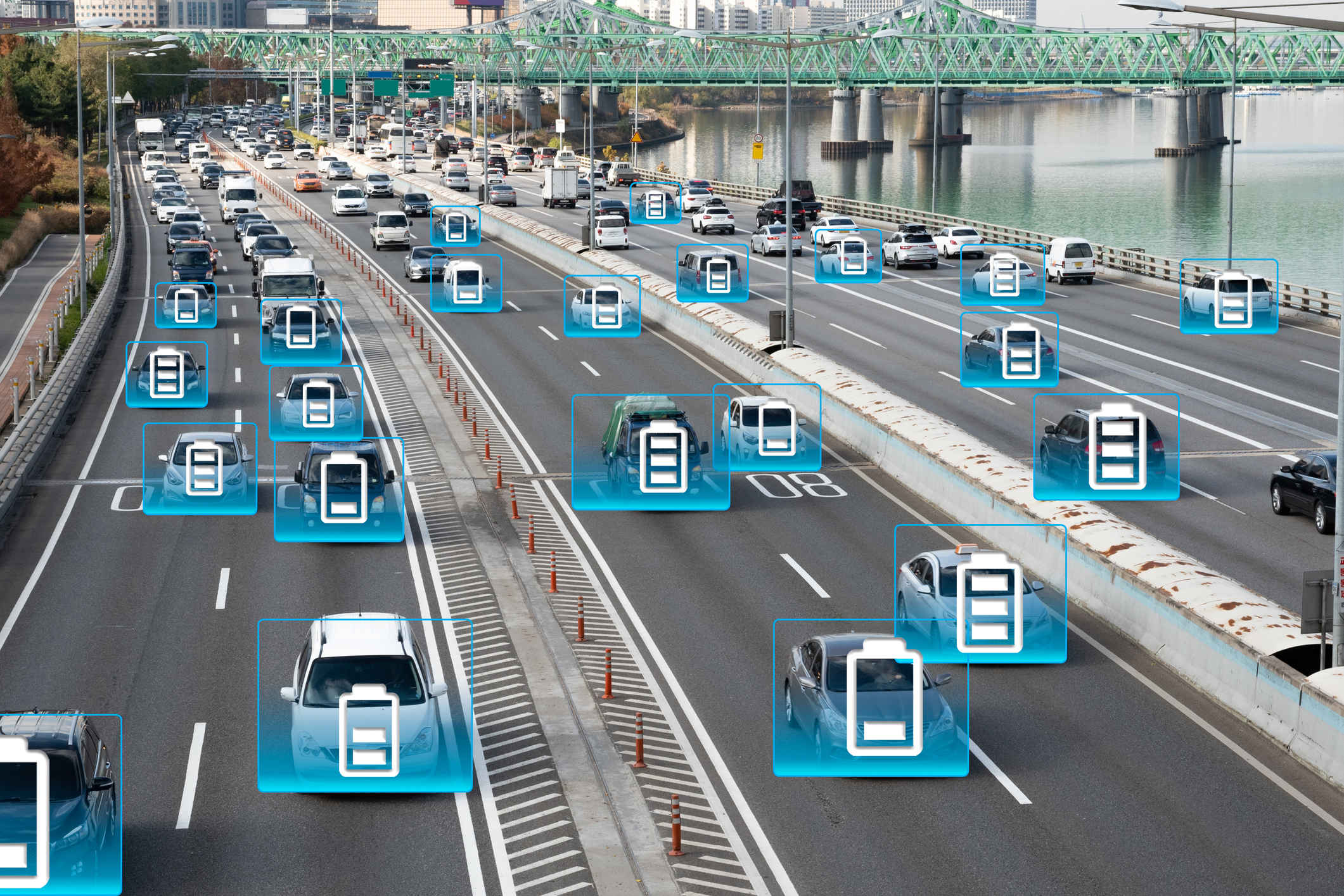
Our automotive engineering experts share their insights into the challenges of electric vehicle design and development.
Have you considered purchasing an electric car as your next vehicle? Chances are that you have. Despite the economic crisis, markets in North America, Europe, or China face rising demand for electric vehicles. And manufacturers respond to this demand. The choice of electrified vehicle (xEV) models and brands is broader than ever. Newcomers compete with established carmakers to gain market share.
What are the top 5 challenges affecting electric vehicle design and development?
Vehicle electrification has reset the rules of the game. The amazing commercial success of the Tesla brand demonstrates that the xEV market is a place where mobility dreams become possible, but not easy. Succeeding in this highly competitive marketplace will require dedication, knowledge, imagination, collaboration, and much more. Next to deploying the right commercial strategy, market players will need to rethink their engineering methods and processes and adopt a fast pace of innovation.
So, what does the vehicle electrification trend change in terms of engineering? What challenges do engineers encounter in electric vehicle design and development?
We’ve asked the question to Steven Dom, Director Business Development Automotive, and Warren Seeley, Director Business Development Powertrain. They have identified the 5 top engineering challenges that automotive engineers need to address today. Get their expert insights in this article and share your own in the comments below.
Challenge #1: select the “right” vehicle architecture

Steven Dom: “With electric vehicles, there is no preconception of what the vehicle should look like. Conventional internal combustion engine vehicles were conceived around a central element: the powertrain. Electric vehicles leave a lot more freedom to the design engineers. The perspective is both exciting and frightening. On one hand, it is thrilling to witness the wealth of innovative designs that are proposed by both new and established companies. Some designs are only made possible thanks to the flexibility of EV architectures. On the other hand, it transforms the job of the design engineer and makes it more demanding than ever.
How can the engineer make sure that she/he selects the most appropriate, better optimized, in short, the “best” architecture that meets all performance requirements? Trying out all options is impossible. Firstly, because there are simply too many of them. Secondly, because time-to-market is also a burning issue. The design engineer does not only need to select the best architecture, but she/he also needs to select it quickly.”
From generative design to design optimization, there are several tools at hand to help engineers explore the uncharted territories of EV design.
Challenge #2: adopt a human-centered design and engineering approach

Steven Dom: “Consider how future electric means of transportation will transform people’s lives beyond mobility. For over a century, cars have represented more than a mere means of transportation. They have been a game-changer in terms of personal mobility. They have re-shaped the face of human dwellings and cities. And they have brought joy to car enthusiasts and motorsport fans.
Cars have certainly helped accelerate the industry and economic transformations. But our world changes. The impact of carbon emissions on climate change, and the rarefication of fossil resource, drives an economic and societal shift. The mindset of people evolves. Yes, powerful cars used to be a symbol of career success and a source of pride. But rather than enjoying the roar of a revving V12 engine, consumers now expect vehicles that are above all safe, comfortable and eco-friendly.”
Deal with electric vehicle design differently
“Electric vehicles are different. They are quieter by nature. The sound of an electric car is not determined by the booming noise of the engine, the clapping of the pistons, the sound of air intake and exhaust. There is room to add tunes that can be carefully designed by artists and music composers. The goal is not only to fulfill the need for a pedestrian alerting system but also to express the model’s and brand’s personality.
The bodies of EVs also feature a wealth of innovative designs. For luxury, long-range limousines, the shape is often sleek and slender, as reducing aerodynamic drag matters more than ever. And for urban mobility solutions, it is the interior space that counts, turning car-sharing solutions into shared offices or living rooms on wheels. With regards to design, the possibilities seem limitless. How can manufacturers fully realize the opportunity of open-ended design?”

Manufacturers must place the needs and desires of human beings at the center of their designs, not the technology. They should keep focusing on consumers’ needs and expectations and adequately address their concerns.
Address consumers’ concerns
Despite a growing consumer’s acceptance, there are still major hurdles to the wide adoption of EV technology. Manufacturers need to push the barriers with the sole purpose of offering a vehicle that meets consumers’ needs. They need to balance characteristics such as driving range, costs, battery charging capacity and charging time, and more. Dom and Seeley wonder about the ever-increasing consumers’ expectations. Although a lot of progress has been made in the field of EV technology, it seems that it will never be enough. Will consumers be satisfied with vehicles that are on par with or exceed the range of ICE vehicles? Consulting company Deloitte exhibits some optimism:
“Over the next few years, we expect some barriers to be completely removed. EVs’ driving range is already comparable to that of ICE vehicles; price has already reached parity, if you consider subsidies in various markets and total cost of ownership; and the number of models available is increasing.”
Source: Deloitte
Deloitte identifies the lack of charging infrastructure as the latest top priority for consumers, reflecting the possibility that they are starting to see EVs as a realistic option and are now considering the practicalities of ownership.
Exceed consumers expectations
But even if manufacturers successfully address future owners’, or users’, concerns, the questions of fulfilling tacit expectations remains. The ever-higher degree of vehicle automation forces NVH engineers to rethink their definition of comfort. Despite technological advances, NVH engineers are more than ever challenged to answer this one question: how can I create the most comfortable ride experience for drivers and passengers? As humans interact with robot-taxis, they’ll expect a safe, comfortable, and pleasant ride. And while safety is a fairly objective criterion, and one that advanced drivers’ assistance systems (ADAS) actively tackle, the notion of comfort and pleasure is harder to define.

Read the blog post Adopt a people-centric approach to electric vehicle sound engineering for more insights into this topic.
Challenge #3: manage the thermal characteristics of the vehicle
Warren Seeley: “Talking about comfort, let us address the intricate question of thermal comfort. With conventional vehicles, that question was easily answered: the heat generated by the engine helped to warm up the cockpit or defrost the windshield. And since driving range was never an issue, batteries and electrical systems could serve the purpose of heating seats or blowing cold air whenever needed. But how do you manage thermal comfort in an electric vehicle without sacrificing range? And how will you achieve excellent heat distribution, making sure that batteries do not overheat while passengers shiver?”
Addressing the question of thermal behavior in the concept stage of vehicle development is crucial to the brand’s success. Siemens’ holistic digital twin approach balances energy and thermal characteristics along with other essential vehicle performance attributes such as durability, NVH, and driving dynamics.

If you need pieces of evidence that EVs can perform under extreme conditions, watch the replay of this webinar: Rapidly validate systems performance using system simulation and reduced order modeling techniques. It addresses, among others, the aspects of EV thermal management under the extreme conditions of Californian Death Valley’s scorching sun.
Challenge #4: get a grip on battery design and integration
Warren Seeley: “Should EV manufacturers get a grip on battery technology or rely on the supplier’s expertise? The question remains open. Most EV manufacturers rely largely on suppliers for various vehicle parts and act mainly as integrators. And while this trend tends to be reverted, with manufacturers seeking to own design and development of a larger portion of the vehicle, battery design and development remains the stronghold of specialized suppliers.”

In a recent discussion with Ed Bernardon, Vice President, Strategic Automotive Initiatives, Henrik Fisker, Founder, Chairman, and CEO of Fisker Inc., explains: “For me this time around, it was not important to prove to anybody that I can manufacture a car. We will be owning a lot of our technology that we feel is important. […] I don’t need to own the development of an air-conditioning, that’s a commodity.
At the moment, we have done a lot of battery research and we have figured out that there is not solid-state battery technology coming around the corner, it’s too difficult, it’s too hard to scale up. Therefore, we know that we will be living with lithium-ion batteries for a long time, and we don’t need to own the cell manufacturing technology. I’d rather be open to different battery technologies when they improve slightly and also be able to package my batteries so that if one battery manufacturer can supply enough, I can use somebody else.”
Again, integration of the components and especially of the batteries is key to success. The digital twin helps assess and compare battery performance in multiple setups and configurations, early on.

Listen to the full podcast with Henrik Fisker and Ed Bernardon here.
Challenge #5: adapt to the changing landscape of the supply chain
Steven Dom: “Engineering and manufacturing an electric vehicle radically change the OEM-supplier relationship. To start with, there are only about 200 single components in an electric motor, compared to at least 4000 parts in an internal combustion engine. This drastic reduction in part number brings numerous advantages for the manufacturers. On one hand, this can lead to a significant cost reduction. Not only is the purchase of the parts less costly, but producing EVs also permits economies of scale, when OEMs source their parts from fewer suppliers. Having fewer parts also has implications in terms of maintenance and the overall cost of ownership. It becomes much easier to replace a single component.
For suppliers, the downside is that they are more closely tied with the OEM. For example, the question of battery integration, addressed by Warren, is a crucial one. The digital twin approach drives or steers the suppliers’ decisions. They are also almost obliged to rely on the same simulation tools as the OEMs do. To summarize integration is more important today than ever.”

Of course, there isn’t a single way to address all these challenges. But at Siemens, we’re certain that adopting a holistic digital twin approach will help tackle the future of mobility. Partnering with Siemens, relying on engineering services for technology transfer, and deployment of the digital twin methodology is a step towards success.
Address the challenges of electric vehicle design and development
Learn how to implement a digital twin approach in your electric vehicle design and engineering process by reading the comprehensive white paper: “Relying on a comprehensive digital twin –
Using Simcenter to master the performance engineering complexity of electrified vehicles”