The new revolution in testing: Simcenter 3D Smart Virtual Sensing and Model-based System Testing
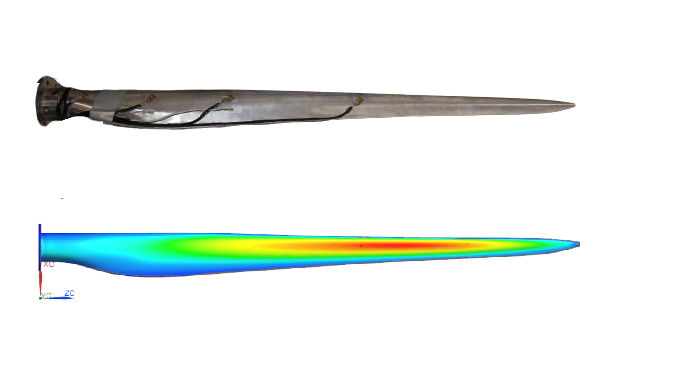
Smart Virtual Sensing is changing how we conduct physics tests. Test and validation are crucial steps for product design and the evolution of new concepts. Usually, we instrument sensors to the key locations and measure the system’s response to required load conditions. This enables us to verify if the static and dynamic responses are as expected or if a system can survive in critical load conditions. The testing technology has evolved rapidly due to the demand for efficient test validation, with the regular release of new types of physical sensors, higher precision test channels, new integrated post-processing capabilities, XiL testing, and more…
Challenges for test and validation
Test engineers are often confronted with the following challenges: How can you take a measurement in locations where physical sensors cannot be placed? examples of such places include:
- Strain gauges cannot be fitted to hot spots due to complex geometry
- Tight packaging makes instrumenting the accelerator to the critical section impossible
- Operational loads are hard to measure as adding an additional load transducer modifies the structure dynamics
- Long instrumentation time and large effort to place a large number of sensors in order to cover the entire structure
- Performing full vehicle tests to validate specific vehicle components is time-consuming and costly
- Damage happens to the expensive structure during the testing due to unexpected overload
Many an engineer has pondered, surely there is a new technology that can help to address these challenges?
Revolutionary Solutions – Simcenter 3D Smart Virtual Sensing
In our previous blog, we introduced how Simcenter 3D Smart Virtual Sensing helps you to do field estimation (strain, stress, velocity, acceleration, and displacement) and load estimation (force, moment). It provides a framework for data fusion of FE model prediction and physical measurement. This framework provides accurate results with compensation for both model inaccuracy and test noise. Additionally, besides augmenting the test results after physical testing, it can export an Executable Digital Twin (xDT) to run in a real-time platform for real-time testing.
With Simcenter 3D Smart Virtual Sensing, you can:
- Measure inaccessible hot spot locations from physical sensors placed in accessible locations
- Measure the acceleration from remote locations to avoid tightly packed places.
- Measure the operating loads through a few strain gauges instead of adding load transducers.
- Use virtual sensors to replace or enrich physical sensors, to speed up the test campaign and optimize the cost
- Determine the operational loads of target components from the whole vehicle testing and then reproduce the equivalent loads on a test bench.
- Monitoring the full field stress in real-time during the testing process allows input loads to be adjusted when the critical stress is met.
Implementation
How can we tackle so many challenges? Simcenter provides an integrated workflow from the Simcenter 3D Smart Virtual Sensing application to the testing environments. This is based on the exported Executable Digital Twin (xDT) that can be deployed on Model-based System Testing (MBST) platforms, giving it the adaptive capability to solve numerous test problems.

The starting point of this workflow is always with Simcenter 3D Smart Virtual Sensing, where we create the smart virtual sensing solution and define the input and output of the xDT. The inputs are the necessary physical measurements, the output can be virtual sensors in required locations, loads, and full-field status. The data fusion solver and the reduced-order FE model are embedded into the exported xDT.
Off-line vs real-time Model-based System Testing
Simcenter 3D Smart Virtual Sensing xDTs can be deployed into both Simcenter Testlab RT (real-time MBST) and Simcenter Testlab Neo (offline MBST). Each option enables different user scenarios.
You may choose to work offline because you simply want to extend measured data sets. Since you have already completed the test and data acquisition, the virtual sensing data can help extend your physical measurements to provide you with full engineering insight, such as operational loads and augmented virtual sensing measurement. It enables you to easily integrate the new method into existing test projects. For example, perform durability analysis in more locations with extended virtual sensors.
Deploying Smart Virtual Sensing within Testlab RT provides all the loads and virtual sensor estimation in real time, enabling you to monitor and interact with the test process.
For example, when testing a new part or even a prototype, damaging the part can result in large costs and extended development times. Therefore, methods of protecting the part can be invaluable. With Simcenter Testlab RT together with Smart Virtual Sensing xDT, you gain additional insight on your part during testing. Should loads exceed acceptable values, the test can be stopped, protecting the part.
The off-line Model-based System Testing
You can first perform testing and data acquisition, and then augment the test results by deploying Smart Virtual Sensing xDT within Simcenter Testlab Neo. The inputs of the xDT will be corresponding test data, the outputs are virtual sensor channels and estimated loads.

Deployment of off-line Model-based System Testing
We can deploy the Simcenter 3D Smart Virtual Sensing xDT to Simcenter Testlab Neo by simply following the steps below:
Step 1:
Performance test with instrumented physical sensors and Simcenter SCADAS for data acquisition
Step 2:
Deploy the Smart Virtual Sensing xDT into the testing environment by using the dedicated Functional Mock-up Unit (FMU) method within Simcenter Testlab Neo Process Designer
Step 3:
Configure xDT inputs with physical measurement results
Step 4:
Execute xDT to extend your physical measurements with more virtual sensor channels and estimated loads
Step 5:
Perform further test data post-processing based on the enriched test results to provide you the full engineering insight.
The complete workflow has been designed so that the exported Smart Virtual Sensing xDT can be seamlessly integrated into the testing environment. It opens many new opportunities to facilitate the test process.
For example, a few strain measurements taken at accessible places can yield the stress of hot spots and operational loads, supercharging the usability of traditional measurement results. With the estimated loads, you can carry out strength and durability analysis.
Real-time Model-based System Testing
You may feel the off-line approach is good, but you must complete the test first and then perform the test data argumentation. You, therefore, want to obtain the virtual sensing estimation in real-time. With Smart Virtual Sensing xDT embedded into Real-time MBST, you can get the extended virtual test channels, view the full field stress and deformation during the test, and even use this field estimation to optimize the testing process. For example, as previously mentioned, you can decrease the input loads when you meet your safety margin for the critical stress. This can help to protect your expensive or irreplaceable test object.
Real-time MBST can be set up by deploying the Simcenter 3D Smart Virtual Sensing xDT to Simcenter Testlab RT. Simcenter Testlab RT provides the application software and real-time hardware to run the Simcenter 3D Smart Virtual Sensing xDT, feed the physical inputs to the FMU input and get the FMU defined outputs in real-time. This will provide the load estimation and field estimation at the same time as physical measurement. The results of the virtual channels can be displayed as a plot along with the physical channels, the full field estimation results can also be streamed to the visualization tool to get the full field status.

Deployment of Real-time Model-based System Testing
Step1:
Instrument sensors and connect them to Testlab RT through a real-time data acquisition system
Step 2:
Deploy Smart Virtual Sensing xDT to Testlab RT via the web interface
Step 3:
Configure the xDT inputs with real-time test channels
Step 4:
Run the physical tests and execute Smart Virtual Sensor xDT to get real-time virtual sensing data
Step 5:
Stream xDT estimation results to the visualization tool for full-field status monitoring
Conclusion
For both off-line and real-time MBST solutions, it is important to know where to put sensors and how many sensors are needed. Simcenter 3D provides the Optimal Sensor Placement to help with this (new from Simcenter 2406 release).
With Simcenter 3D Smart Virtual Sensing, even the inaccessible spots become measurable. This innovative solution not only overcomes the challenge of placing physical sensors in hard-to-reach areas but also significantly reduces instrumentation time and hardware costs. By creating a Smart Virtual Sensing xDT within Simcenter 3D Simcenter 3D, you can export and embed the xDT in Simcenter Testlab Neo for off-line test results augmentation. Alternatively, you can deploy the xDT in Simcenter Testlab RT for real-time Model-based system testing. These seamless integrations enhance your testing capabilities, providing accurate data and insights that were previously unattainable.
This is not just a small incremental step in your testing capabilities but a revolution to transform your testing processes.
- Measure the inaccessible hotspot from instrument sensors placed on accessible locations
- Get operational loads in a practical way to leverage strength analysis and durability study
- Save instrumentation time and cost when testing large structures by using virtual sensors
- Perform equivalent component testing on a test bench by reproducing operational loads
- Get insight into the performance and interact with the structure through the whole testing process