The New Science of Digital Materials
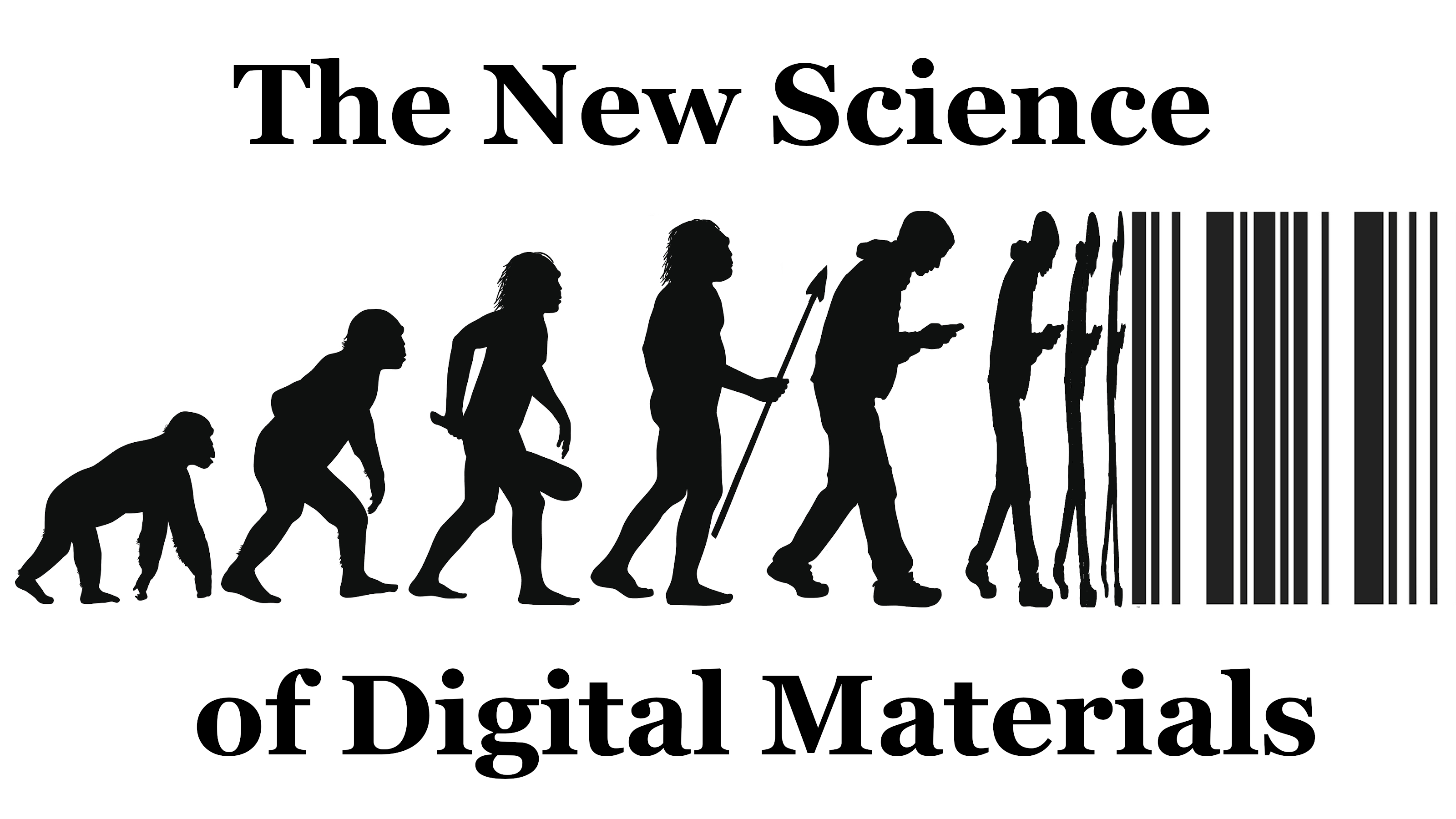
As engineers, we tend to take materials for granted. In most engineering projects materials are “a given”, defined at the start of the design process, and rarely changed throughout it. We are prepared to tweak every single geometric parameter in the search for optimal engineering solutions, but materials are treated as a constraint rather than a degree of freedom. The recent development of “digital materials” that can be designed, analyzed and optimized via simulation changes this paradigm forever and unlocks endless possibilities for technological and cultural development.
Every significant advance in human civilization has been driven by revolutionary (rather than evolutionary) developments in material science: from the Bronze Age to the stone age to the Industrial Revolution, to the current “Silicon Age”, developments in materials technology have heralded new eras of technological and cultural progress.
However, until recently, the pace of development in materials science has lagged behind the rate of product development innovation, because of the time and expense required to develop and test novel materials which often requires the experimental investigation of hundreds (if not thousands) of possible variants of microstructural configurations and chemical recipes.
Engineering and materials science
Large technological advancements are almost always dependent on the creation (or discovery) of novel materials. Revolutionary developments in material science enable the next generation of technological advancement. The full exploitation of those technologies (by engineers) will often require further investment into the evolutionary development of those materials.
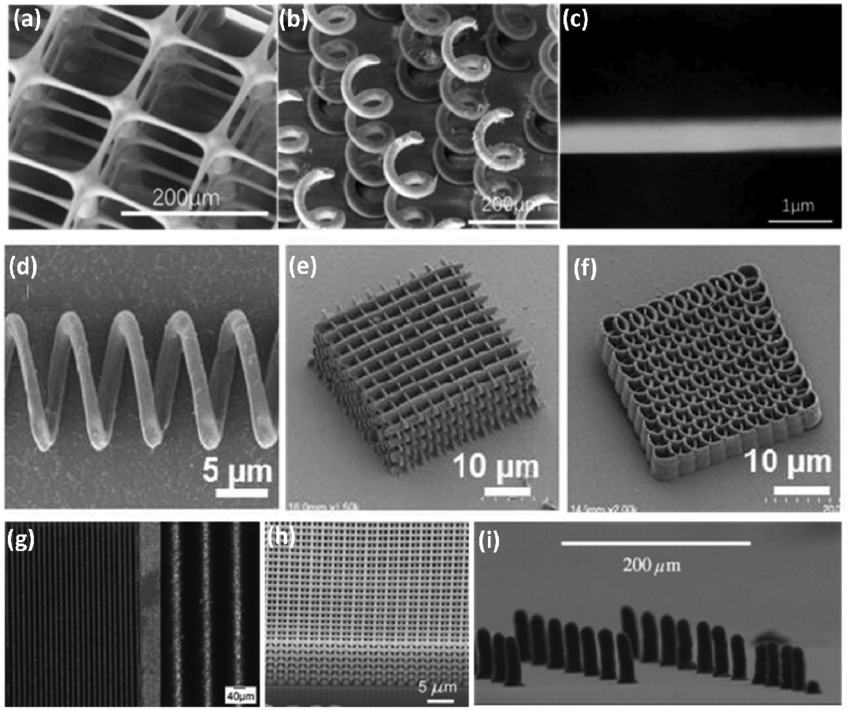
So, although engineers and material scientists inspire each other to new levels of innovation via a sort of “virtuous arms race,” engineering and materials science have largely been separate disciplines. Co-operation has always been limited by the fact that, although the bulk of engineering design has moved towards CAE simulation, developing novel materials is usually done in the lab rather than a computer. This makes it time-consuming, difficult and expensive.
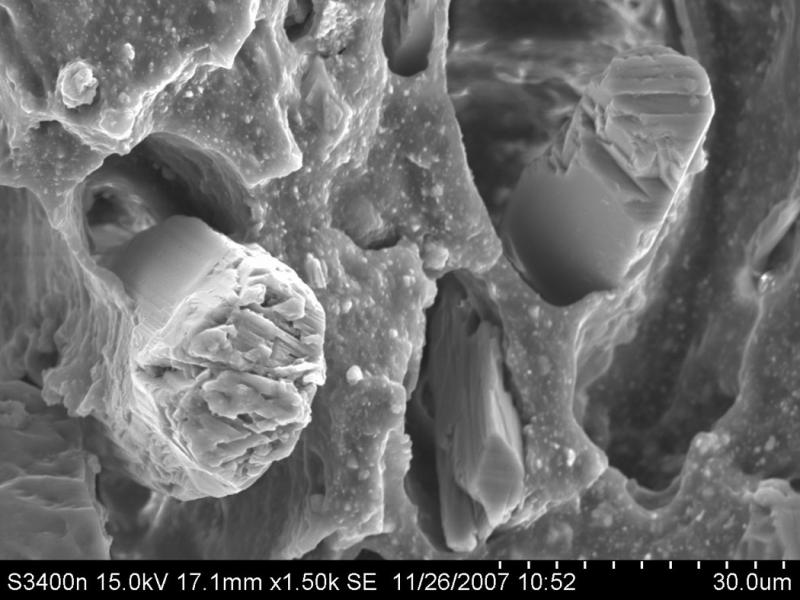
The job of engineers is to progressively improve the performance of a product with regard to objectives such as stress, temperature, fatigue, sound, cost or sustainability, by making incremental design changes. Sometimes those are manually driven, but increasingly through a process of automated design exploration where AI determines the next improvement from the results of previous simulations. While there are obviously constraints, engineering progress depends on the exploitation of every possible degree of freedom, tweaking every geometrical and mechanical parameter until an optimal solution is found.
However, this process typically starts with the selection of a commercially available material (from an online database or pdf catalogue) and the design process will optimize performance based on the material already chosen. So, while the design process might alter any number of geometrical parameters, the materials remain fixed throughout. In other words, the material is a constraint, rather than a degree of freedom.
Digital materials: a new paradigm
The recent acquisition of MultiMechanics Inc by Siemens changes that forever by giving Simcenter users (and the wider engineering community) to test and optimize novel materials from the comfort of their computer. And more importantly, offers the opportunity to make material design part of the design exploration process. Put simply, MultiMech allows you to predict (and therefore perfect) how the microstructural properties of an advanced material affect its engineering properties and performance.
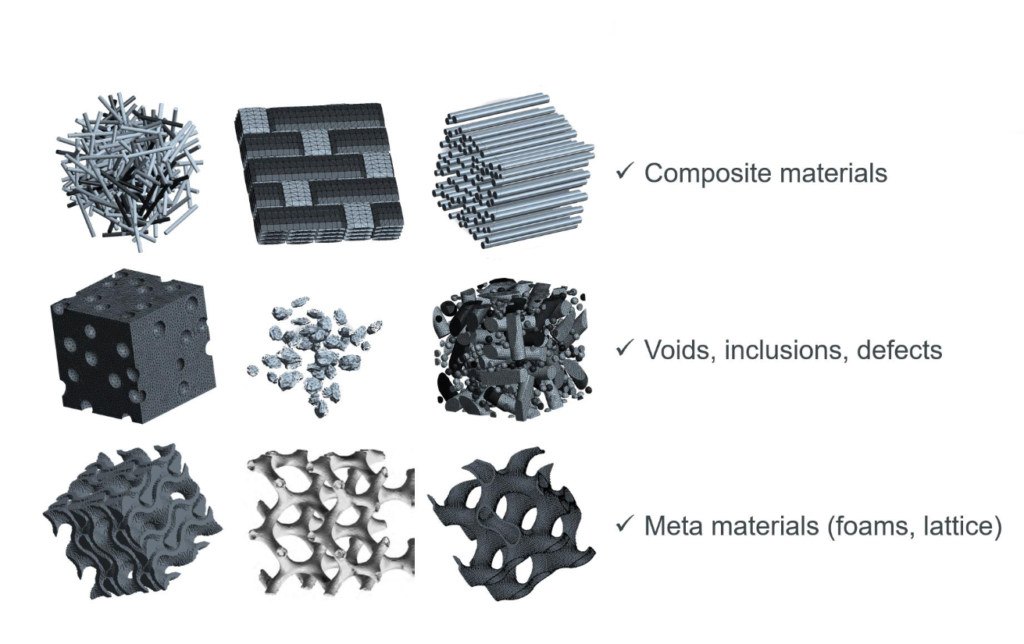
However, this is only half the story. With millions of potential variants, the potential design space is huge. To include digital materials in our automated process, the design exploration algorithm needs to make intelligent choices about which variants to test next. Materials data is complicated and difficult to share and organize. What is missing is materials-aware Artificial Intelligence, to help engineers (and automated design exploration algorithms) navigate the materials design space. Of course, that is never an absolutely free choice. It doesn’t make any sense to design a tailored material that is un-manufacturable, or only at a prohibitively high cost.
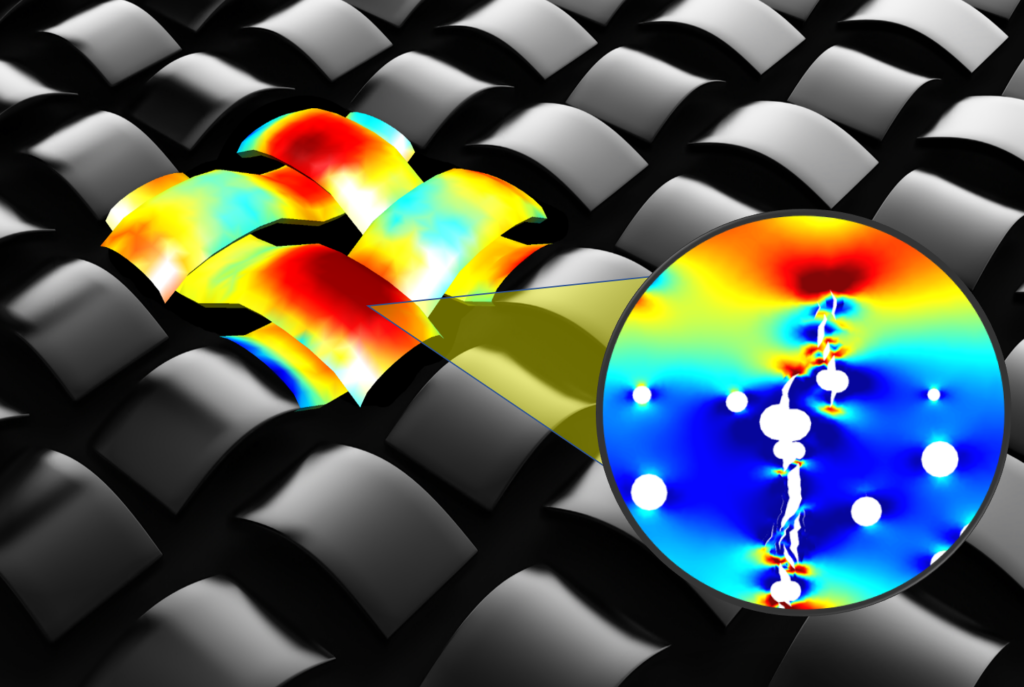
To solve that problem, Siemens has partnered with Citrine Informatics, the industry leaders in materials informatics, which combines data science, materials science, and materials-specific machine learning that assists in the design and exploration of advanced materials.
Citrine has built the first enterprise materials informatics platform for data-driven materials and chemicals development. Their platform combines smart materials data infrastructure and AI, which accelerates the development of cutting-edge digital materials. By combining this capability with product design simulation, it unlocks materials design as a degree of freedom for design engineers.
Of course, not all engineering materials are rigid. Siemens also recently acquired computational chemistry company Culgi. This technology allows engineers to predict the chemical and thermodynamic properties of fluids, and so-called “soft-materials”, whose macroscopic behaviour depends on interactions at a microscopic, and even quantum scale.
This is nothing short of a paradigm shift: for the first time in the history of our species, materials development can progress at the same pace as engineering innovation. This has the potential to unlock unprecedented collaboration between materials scientists and product design engineers, and to develop the right material for the right application, every time.
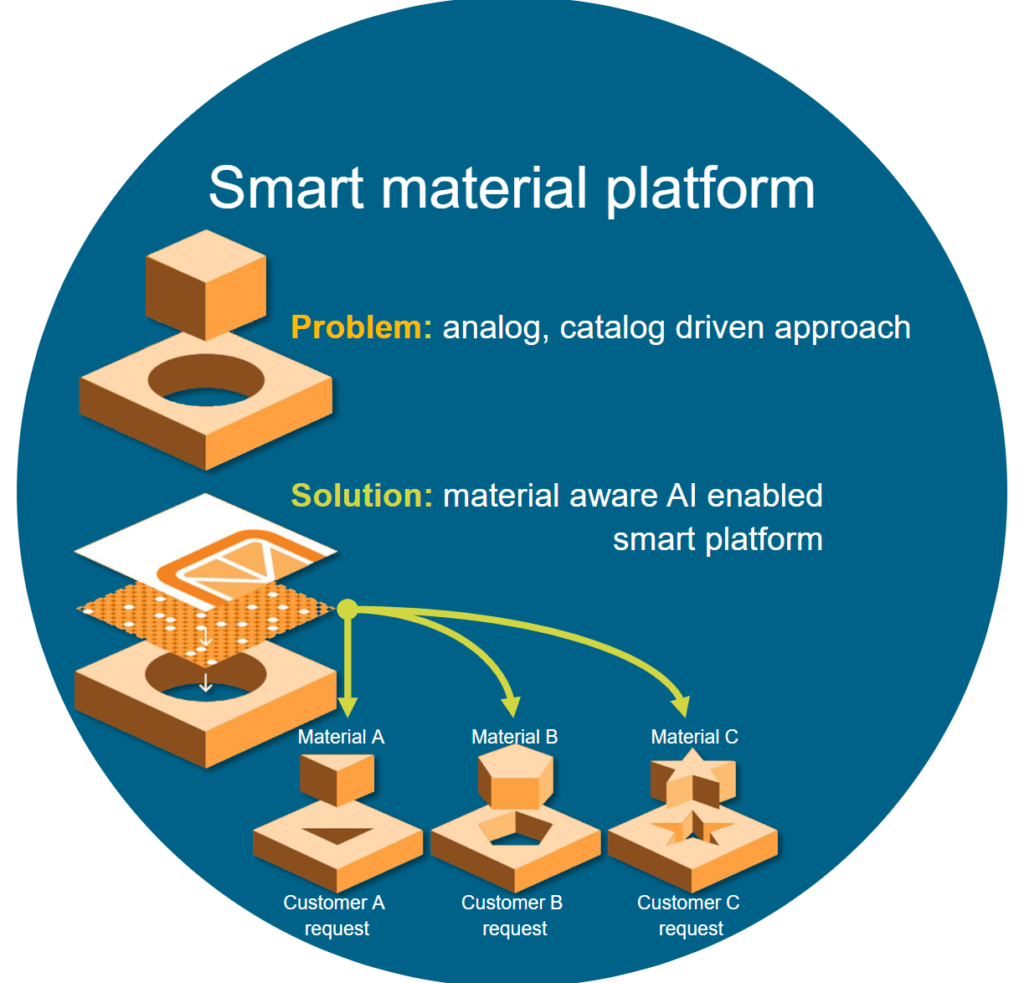
Digital materials of the future
I started by talking about how material science has been at the heart of every major cultural, technological and economic benefit that our species has experienced over the last 6000 years. In lots of ways, the cadence of that development has been driven by the pace of development of novel materials that allow engineers to solve the challenges that we face as a species.
I think that it’s fair to say that as we try to avoid the catastrophic consequences of climate change in the next 20 years, it will require a much tighter coupling between the materials science and engineering. As we strive to build a clean energy future, we will need less-polluting methods of transportation, lighter weight alloys, biodegradable plastics, better batteries, more efficient wind turbines, solar panels and nuclear reactors. We will also have to find alternatives for many of the rare earth elements that have been depleted by industrialization and globalization.
It’s time to exploit materials as a degree of freedom and to stop treating them as a constraint.