Thermal management of Electric Vehicles is now a breeze
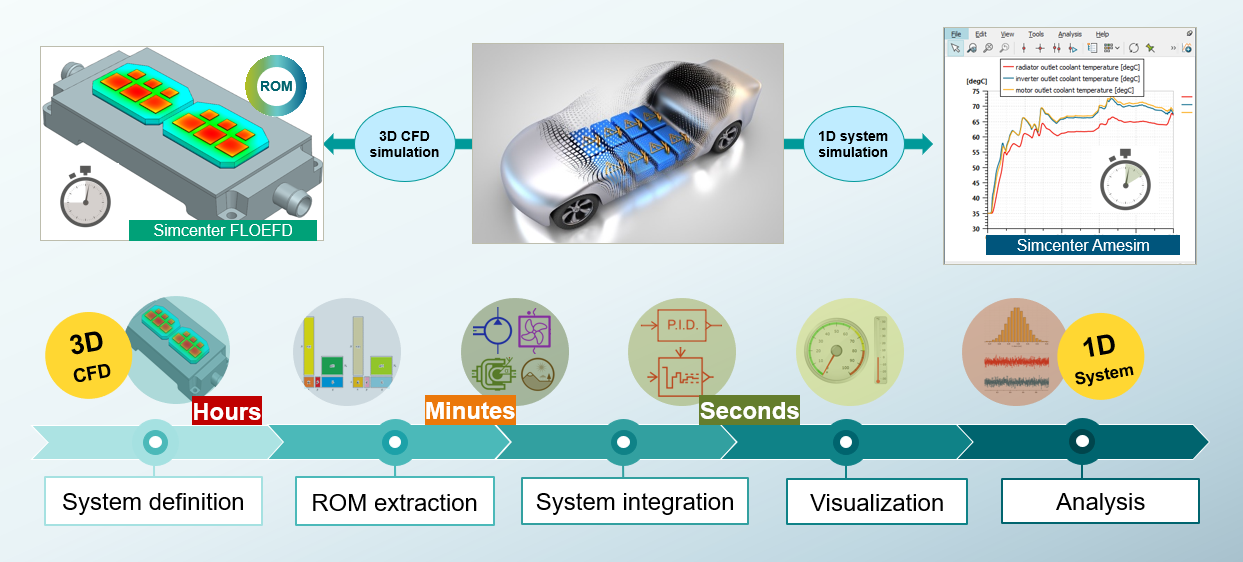
Expanding 1D system-level models with 3D ROM models
The battle between traditional Internal Combustion Engine (ICE) and electric vehicles will one to remember. Due to high levels of technological breakthroughs in the automotive community and a rapid rise of electric vehicle manufacturers. While customers pay attention to performance when deciding between ICE and electric vehicles, the major factors are not just the top speed and acceleration. Range, efficiency, durability and driving characteristics often come into play. To ensure the success of an electric vehicle on the market, it is necessary to reduce delays and improve the productivity between different engineering teams (such as mechanical, thermal, electrical, control and software). Reduced order models from 3D CFD tools can be substituted for 1D System Simulation models to provide more accurate and detailed results, so teams can make an informed and correct design choice earlier.
A Reduced Order Model (ROM) is a simplification of a high-fidelity static or dynamical model that preserves essential behavior and dominant effects, for the purpose of reducing solution time or storage capacity required for the more complex model. The typical steps for the BCI-ROM (Boundary Condition Independent – Reduced Order Model) workflow are illustrated below and highlight how users can directly benefit from their high-fidelity 3D CFD models from Simcenter FLOEFD to integrate them into a wider scope 1D System Simulation model in Simcenter Amesim.

The accuracy of the results is preserved while having a significant CPU speed-up to execute long driving cycles, faster.
Power Electronics Cooling
While even Porsche used air-cooling for their ICE vehicles back in the day, air-cooled heatsinks are not a perfect solution for the modern traction inverters due to the high power density. Therefore, it is not rare for automotive inverters to be liquid-cooled. PCB (Print Circuit Board) assembly can be mounted on a coldplate, which makes thermal management of power-dense components a breeze. A coldplate has flow channels for the liquid to pass through, the mass flow rate and the temperature of the liquid can be controlled via a pump and a fan-cooled radiator.

1D Systems Simulation
Simcenter Amesim is an integrated, scalable system simulation platform, allowing system simulation engineers to virtually assess and optimize the performance of mechatronic systems. It’s used here to represent the complete Electric Vehicle except for the PCB coldplate. The first group contains a longitudinal vehicle, Vehicle Control Unit (VCU) and driver models, which allow the specification of fundamental parameters, such as the vehicle mass (dependent on the mass of a battery pack), rolling coefficients, aerodynamics, wheel dimensions, gear ratio and the driving cycle (SFTP-US06). Power electronics group is composed of a Permanent Magnet Synchronous Machine (PMSM), average 3-phase inverter (so switching effects can be modeled orders of magnitude faster), high and low voltage batteries, sensors and controllers. Cooling pump, radiator, fan, expansion tank and sensors make up the cooling system.

Simcenter Amesim is perfectly suited for creating and investigating system-level models. However, while providing the means to perform 1D System Simulation calculations, it is sometimes more relevant to reuse models from 3D when it comes to electronics and thermal management with some 3D considerations, which are quite difficult to capture with a 1D lumped approach. One relevant example is a 3-phase inverter. To analyze its performance, temperatures of IGBTs and diodes must be monitored to avoid overheating and adjust thermal accordingly.

3D Assembly Modeling
Simcenter FLOEFD is a CAD-embedded solution that allows you to perform multiphysics simulations in the early design stages, helping the engineers to dismiss undesirable design options. It is perfectly suited to perform a full 3D CFD simulation of the traction inverter to calculate temperature distributions in the device, as well as the flow pattern. However, due to the high complexity of the model and computational power requirements, it would not be feasible to solve 3D CFD and 1D system models simultaneously. To overcome this limitation, Simcenter FLOEFD allows you to extract a Reduced Order Model (ROM), making the model very quick to solve (up to 40.000 times quicker, compared to traditional 3D CFD model). Such models are also Boundary Condition Independent, which allows you to vary the thermal environment of the model (i.e. peripheral Heat Transfer Coefficients) without affecting the accuracy of the solution. BCI ROMs can be exported as a Functional Mock-up Unit (FMU), making it portable and easy to embed into other tools.

1D-3D CAE: Combining System-Level and Assembly-Level Models
Simcenter Amesim is one of over 100 tools that support FMU import and export. Once the FMU of the inverter is imported into Simcenter Amesim, the system can be solved. During the solution, the cooling system loop will provide transient HTC values and fluid temperatures to the FMU, while cold plate heat flux and component and cold plate temperatures will be sent back to the system. Since the cooling system is a part of the whole electric vehicle, calculated inverter temperatures will affect the vehicle’s performance, such as range and coolant temperature, at minimum.


Further work may include experimenting with different inverter designs, substituting IGBTs for MOSFETS, and so on, to see what components have a critical effect on the entire system.
Connecting two dimensions
1D System-level and 3D assembly-level designs often differ in terms of the purpose, power requirements and duration of the simulations. Expanding 1D systems with accurate but quick-to-solve 3D models enables the engineering teams to produce more realistic simulations at earlier design stages, ultimately allowing you to reduce time to market. There are several benefits using Simcenter FLOEFD BCI-ROMs with extremely fast execution within Simcenter Amesim:

Combining 1D/3D with ROM is pretty nice, isn’t it?