EASA: trends in aircraft certification regulations
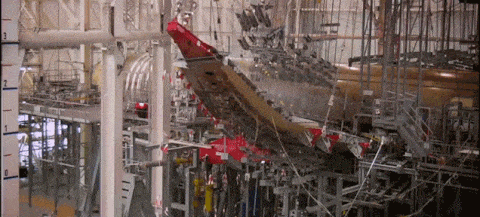
During our GVT Master Class, we had the pleasure to host Elena Garcia Sanchez, Structures Expert at the European Aviation Safety Agency (EASA). She gave a presentation on how to comply with aeroelastic stability requirements for aircraft certification regulations.

Can you briefly explain the responsibilities of EASA?
EASA is the single regulatory authority for civil aviation safety in Europe, consisting of thirty-two member states. It was established in 2002 as an agency of the European Union (EU) responsible for civil aviation safety. The organization assists the European Commission in the drafting of aviation safety regulations. It also certifies and approves aeroplanes, propellers, engines, and organizations with exclusive competence. The regulations are derived from ICAO (International Civil Aviation Organization), a worldwide authority.

What is your role within EASA?
I am a Structures Expert within the Large Aeroplane Department of the Certification Directorate, and my work involves fixed wing product certification and continued airworthiness. Together with the Product Certification Manager and several experts of other disciplines, I help review and approve the requests of companies that seek to certify a new aeroplane design or a modification according to regulations, such as airworthiness and environmental certification (part-21) or large aeroplanes (CS-25). We also address in-service events that could potentially affect safety.
When a company wishes to certify a new aeroplane design, it must comply with a set of rules. The certification team investigates the design and verifies whether it complies with regulations. The certification process usually starts with a familiarization meeting with the applicants, where they introduce the design of the new aeroplane and its characteristics, as well as the proposed means for regulation compliance. We then engage in further discussion to understand and agree upon critical aspects of compliance. I may ask questions such as “how do you define the load cases applied in the aeroplane static test?” or “how will you analyze the gust response of the aeroplane?” Actually, the more novel and complex the design or the means of compliance, the more time we need to spend on investigating if nothing will go wrong. This is part of the “Level of Involvement” principle, which also takes the design organization performance into account.
How would qualify the designs that you received for certification? Do you see more novel designs? Are more newcomers entering the market?
There are several new and very innovative ventures in the general aviation world, and indeed also some new developments in the field of large aeroplanes. For large aeroplanes, however, the novelties tend to be more an evolution than a revolution. Most applications come from established players in the aviation industry, where designs are in continuation with their predecessors. They rely on their past experiences to propose designs that integrate innovation while still linking to previous designs. There are also examples of manufacturers entering the market of large aeroplanes. This typically requires quite a significant launching effort. For instance, think about the expense of testing a brand-new large aircraft design at all levels—from thousands of coupon tests, to full aeroplane specimens. Depending on previous experience, it may be necessary to recruit experts, develop certification expertise and establish new organization procedures in order to be aligned with certification demands.
What is the most challenging part of certification procedures?
Some structural disciplines are relatively more challenging than others in terms of complexity, test difficulties and reliability of analysis prediction. Static strength evaluations need to be comprehensive and either rational or conservative. However, it can be considered as relatively straightforward. Fatigue strength evaluations are less intuitive, but still part of the regular activity of small organizations obtaining Supplemental Type Certificates (STCs, third party changes). I’d say that the next step in complexity is predicting sudden decompression, flutter behavior, and in general, complex evaluations with several highly non-linear aspects—such as ditching or crashworthiness assessments. A refined rational analysis is always trickier than a simple conservative approach.
A typical test called GVT to predict the flutter behavior of an aircraft
Which role does simulation play in the certification process?
Today, it is not possible to certify a new aircraft based on simulated data only. Applicants rely more on simulation than before, as they benefit from the increased computational power of modern PCs and have a better understanding of typical phenomena. However, they always need to validate their finite element models through physical tests. We insist on the fact that a physical test reference is still needed, as it is easy to lose track of reality. We have seen problems occur due to errors in the model or oversimplified analysis. I remember a situation where a failure mode had been forgotten in an aeroplane simulation model. The wing of that aeroplane failed in a static test. Luckily, the static test was performed and the issue was discovered in a laboratory and could be managed and corrected efficiently. For that reason, a test reference of sufficient similarity and representativeness is always a must in the certification process. A good guide for structure and similarity proof can be found in the AMC to CS-25.307.
Maximum wing bending test of an A350 XWB, Airbus
How do you see regulations evolve?
The trend is towards performance-based regulations, which are less prescriptive but maintain the level of safety. We wish to be able to respond with agility to changes in the world of aviation and to the novel designs that are brought to us. The intent is to achieve a balance between flexibility and a firm reference to ensure a level playing field, and mitigate possible risks and uncertainty.
How do you feel about working at EASA?
Before joining EASA, I worked as a stress engineer in private companies, contributing to the analysis and test of space and aeroplane structures. I familiarized myself with certification processes; at that time, from the applicant side.
At EASA, I have had a chance to work with different colleagues who had an industry background like me, deep academic knowledge or regulatory expertise. As an EU agency, we strive to follow a harmonized multidisciplinary approach, and to benefit from the varied certification experiences. I like to engage in advanced technical discussions with my applicant counterparts, who bring their knowledge and different perspectives on practical engineering challenges.
If you want to know more about the certification process for flutter and how to use physical testing for verification for aircraft certification regulations, follow our on-demand webinar.