Vehicle aerodynamics CFD simulation in Simcenter STAR-CCM+
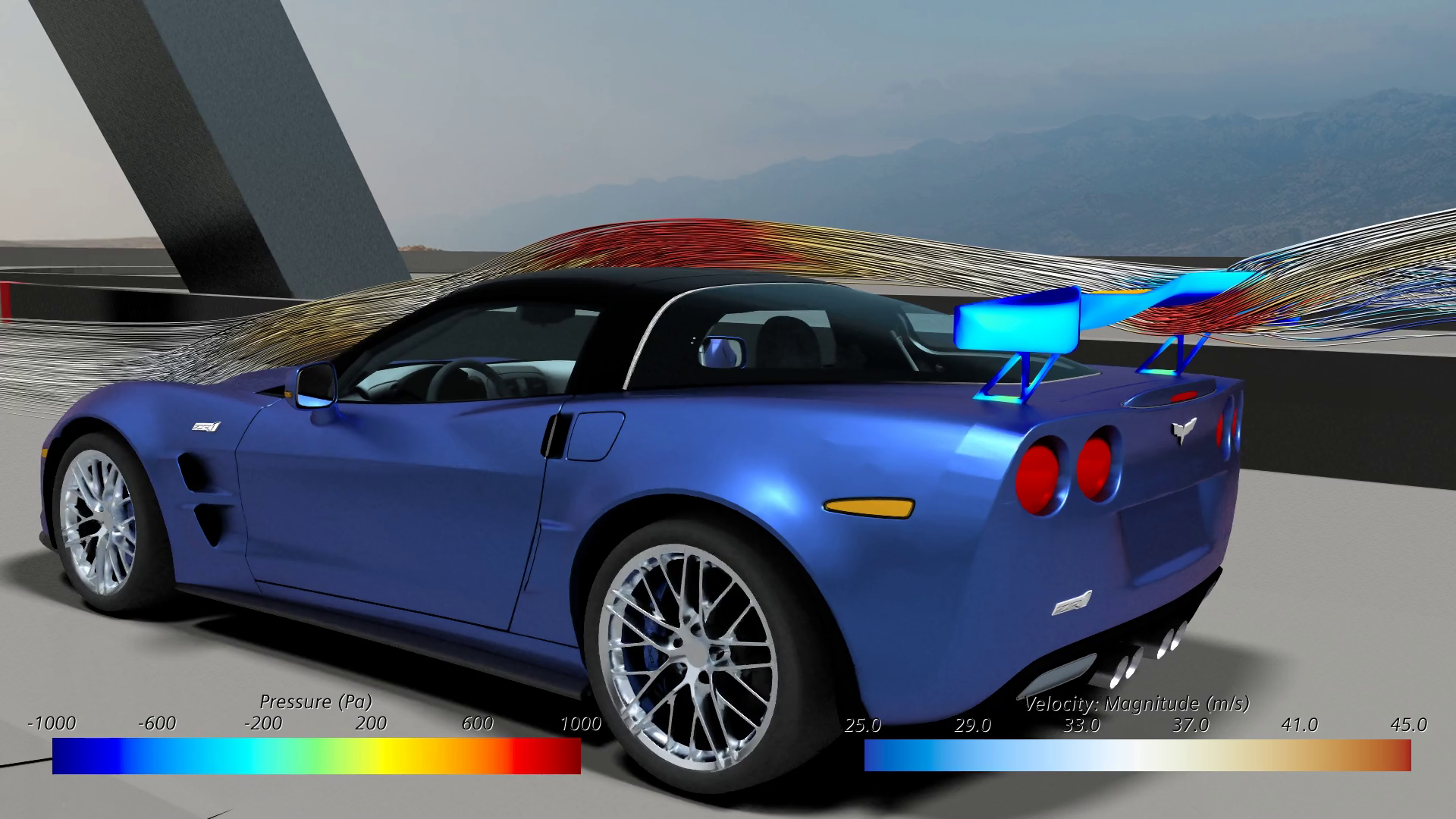
It’s no secret that the automotive industry is undergoing one of the biggest disruption in history. In the race for efficient, sustainable, yet attractive individual mobility solutions vehicle aerodynamics CFD is an important factor already today. And it will become even more relevant in the future.
Reducing energy consumption requires an analysis of all aerodynamically relevant components for World harmonized Light-duty vehicles Test Procedure (WLTP). Moreover, the electrification of vehicles comes along with a need for further reduced aerodynamic resistance in order to extend driving ranges and recuperation efficiency due to lower drag. This implies the development of active aerodynamic devices to adjust for different driving conditions. Likewise with less noise stemming from the powertrain, aeroacoustics will play a major role for cabin noise and hence passenger comfort. And with the continuous establishment of autonomous drive systems it is a mandatory safety requirement to keep sensors and cameras clear from soiling under all weather conditions. A topic directly related to water management coupled to aerodynamics. In consequence, all this adds up to a further significant increase in vehicle development complexity.
Therefore, the key for any automotive company is to turn this complexity into a competitive advantage. Something that can only be done by leveraging digital product development.
Accelerate innovation with fast and accurate vehicle aerodynamics CFD simulations
Without doubt physical wind tunnel tests remain a viable tool for any vehicle assessment. It is crucial as the ultimate validation tool late in the development cycle and relevant for early singular prototype assessments. However, with high operating cost on the one hand and the need to assess thousand of aerodynamics variants and conditions on the other it needs to be complemented by virtual development methods.
Computational fluid dynamics CFD simulation is the key technology to predict and understand real-world aerodynamics behavior. Based on that engineers can explore many design variants in search for optimum solutions in the most cost-efficient manner. However, precondition for such virtual aerodynamics engineering is an accurate prediction of drag and lift forces. This includes the precise quantification of the performance impact of components such as wheels, mirrors, spoilers, etc. Furthermore relevant aerodynamics CFD must allow for the assessment of innovative aerodynamic concepts early in development. Based on that CFD has to report the aerodynamic impact of optional equipment which is a requirement for WLTP certification.
Simcenter STAR-CCM+ is a multiphysics computational fluid dynamics (CFD) simulation software that allows
users to build a high-fidelity, comprehensive digital twin. The latter allows to assess and optimize the aerodynamic performance of a vehicle before building any physical prototype. It uniquely integrates every step of the simulation process, from geometry preparation to volume meshing, solving and postprocessing. It thereby enables engineers to quickly assess the impact of configuration or design changes on aerodynamic performance.
Quickly prepare complex geometries for vehicle aerodynamics CFD simulations
Simcenter STAR-CCM+ offers the ability to handle even the most complex geometries, including complete vehicle assemblies of thousands of parts with minimum user effort. CFD engineers can leverage a tight link to CAD programs for bi-directional data transfer including parameters and meta-data. Alternatively you can use a high-quality neutral or native CAD import.

You can further reduce the preprocessing time for an aerodynamic CFD simulation using a fully automated meshing pipeline. Surface wrapping is a robust and fast surface preparation approach that converts complex input geometries into a clean, ready to volume-mesh, watertight surface.
The trimmed cell mesher offers great scalability even on high core counts and low memory consumption. In conjunction with the prism layer mesher that is easy to use and robust to generate low y+ meshes on exterior surfaces, it is the first choice for external aerodynamics simulations. For further fidelity you can easily refine the volume mesh in critical areas such as wakes with user-defined shapes. Parallel meshing for all cell topologies (poly, trim, prism) helps to generate meshes quickly.
All this results in reducing preparation time for a vehicle aerodynamics CFD simulation from weeks to hours, freeing up the time of the CAE aerodynamicist to the thing that really matters: Engineering superior aerodynamics solutions.
Increase throughput with fast and accurate vehicle aerodynamic CFD simulations
Even the fastest process is of no value if the results are not accurate enough to drive valuable engineering decisions. For external vehicle aerodynamics CFD Simcenter STAR-CCM+ offers industry-relevant validated physics models, getting consistent and accurate results. A full suite of turbulence models allows engineers to accurately capture skin friction as well as separated flow dynamics and turbulent structures in the vehicle wake. Density-based coupled solution of mass, momentum and energy equations ensure robust convergence. Low y+ meshes on crucial surfaces accurately capture boundary layer phenomena and enable the prediction of flow separation.
Simcenter STAR-CCM+ offers two simulation approaches: A steady-state Reynolds-Averaged Navier- Stokes (RANS) allows for faster running simulation used for design studies.

While more computationally expensive, you can use unsteady Detached Eddy Simulations DES when detailed insight is needed about transient flow phenomena. This enables engineers to run high-fidelity, transient vehicle aerodynamics CFD simulations.
Ultimately the tool offers all required capabilities to create a validated digital wind tunnel for your vehicle aerodynamics development work.
Maximize your throughput through proven scaling and automated solver adjustment

To speed-up aerodynamics CFD simulations Simcenter STAR-CCM+ offers parallel volume meshing and excellent solver scalability on computational clusters up to very high core-counts, ready to leverage CFD in the cloud. The built-in solution acceleration features make the coupled solver robust and yet fast without any user intervention or tuning. On top grid sequencing initialization provides more accurate initial conditions to further boost the time to results.
Save engineering time by automating vehicle aerodynamics
Built for process automation, Simcenter STAR-CCM+ is reducing setup time with a end-to-end workflow within a single environment. Based on this aerodynamic engineers benefit from using a dedicated vehicle aerodynamics workflow or macro-based automation. This enables you to easily generate aerodynamic databases without requiring any user customization.

Explore the possibilities through integrated Design exploration and surface sensitivities for drag
Based on a fully-automated CAD-to-result end-to-end solution the – again fully integrated – intelligent design exploration tools make it easy to run automated design exploration studies. Leveraging an unbeaten hybrid and adaptive search algorithm, aerodynamics CFD engineers can explore designs that minimize drag while maintaining constraints on aerodynamic balance. All this without being an expert in optimization and without the need for any external software tools.
On top, based on the adjoint technology aerodynamicists get immediate detailed insight into surface sensitivities with respect to drag coefficients for a given design variant. Those insights could be used to identify areas of high relevance to the aerodynamic performance that then could undergo design exploration studies or could be directly used for local design refinements.
Go beyond aerodynamics in one integrated CFD software
Today’s vehicle aerodynamics can no longer be taken out of context of various other engineering challenges associated to it. When designing a vehicle, engineers need to balance aerodynamic performance in terms of lift and drag, impact of wind loads on structural mechanics, thermal management, water management and aeroacoustics.
And even if these disciplines might be tackled by various expert teams due to their respective complexity, it is a key for any automotive company to ensure the best possible software platform for this cross-domain collaboration. As a multiphysics computational fluid dynamics (CFD) simulation software, Simcenter STAR-CCM+ offers a unified solution that allows to capture the whole range of associated engineering challenges.
Assess structural impacts with fluid-structure-interaction FSI
Execute fluid-structure-interaction (FSI) simulations to calculate the deformation of components due to pressure loads
Improve vehicle safety through water management
With a huge range of multiphase models Simcenter STAR-CCM+ allows to extend aerodynamics simulations to complex multiphase scenarios to investigate water management including soiling, wading, wipers etc.
Balance and optimize cooling performance and aerodynamics
Within the same tool, engineers can not only asses single phase fluid dynamics or multiphase water management: Simcenter STAR-CCM+ also handles solid components for any Conjugate Heat transfer problem. This includes cabin comfort, powertrain thermal management or any other cooling problem, like the brake cooling problem above.
Increase passenger comfort thorugh aero-acoustic simulations
Based on high-fidelity aerodynamics CFD simulations, engineers can take it even further to analyze aeroacoustics phenomena such as side mirror noise.
Learn more about Simcenter STAR-CCM+ vehicle aerodynamics CFD simulation in this Webinar series