Vehicle NVH integration: how to combine test and simulation
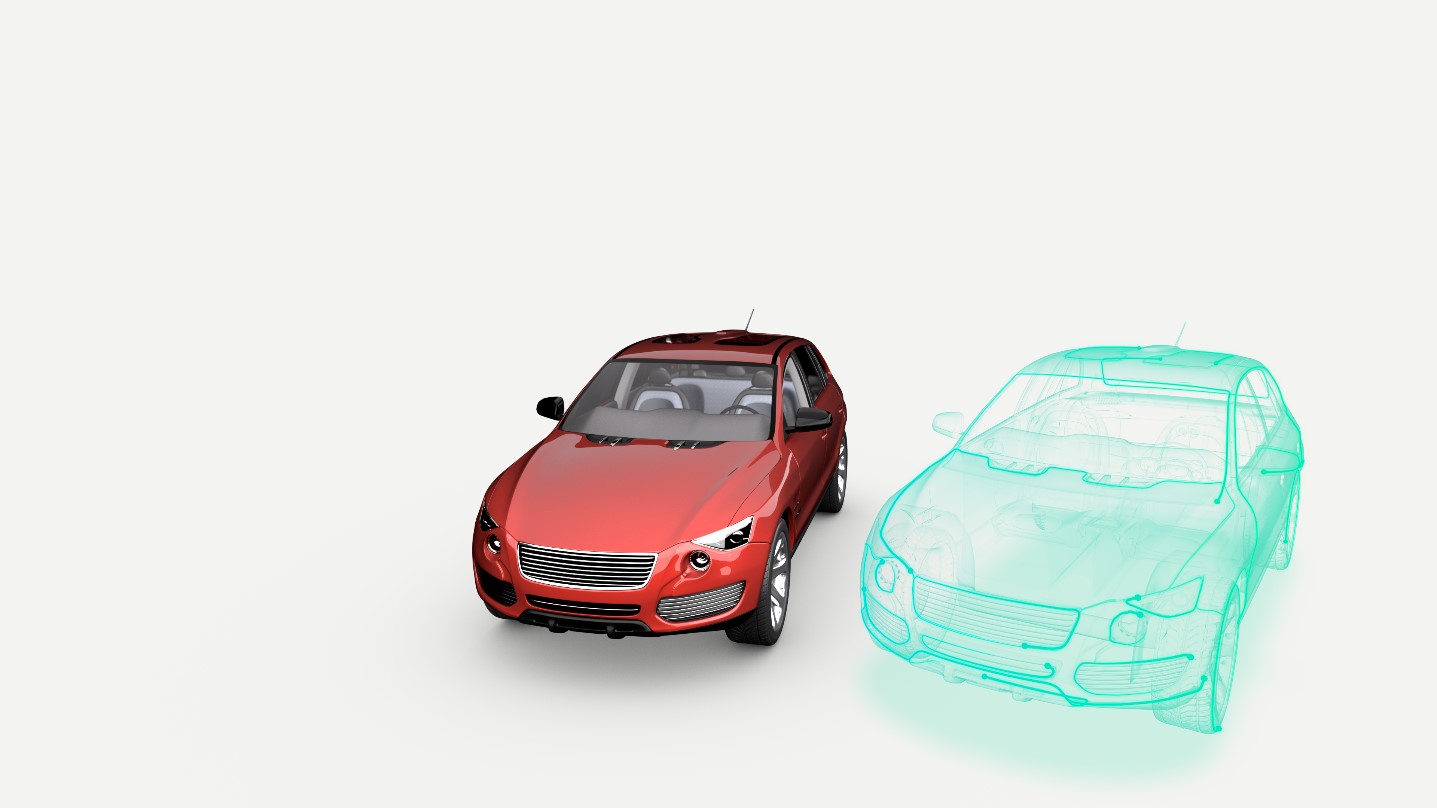
This article was co-written with Ricardo Sales, Business Developer Manager for Simcenter Automotive Testing Solutions.
The first time I drove a fully electric car, I admit I got almost scared.
It was a Tesla Model X 75D (not even the most powerful version), and I remember I was thrilled by the acceleration I could get by pushing full-throttle on a straight road. Even just holding the steering wheel was a ‘vibrant’ experience: I had the feeling that some sort of traction control was constantly adjusting the torque between the front wheels to be able to handle the enormous power coming from the electric drive unit.
At that moment, I wondered how auto OEMs manage to integrate those huge sources of power in their vehicles and still ensure that, while you drive, you have a comfortable experience and you don’t jump over the seat.
The Quest for Integration
As an NVH engineer, I want to know as soon as possible if the vehicle I’m assembling will be pleasant to drive or not.
But when placing the different pieces of the puzzle together in such a complex system, it’s hard to predict the outcome.
Carmakers know this very well, and it is still a challenge to close the gap between who designs the different parts (be their internal departments or external suppliers) and who integrates them.
So the question is: is there a way to understand as soon as possible if a combination of components will make my vehicle sound better or worse than another one?
The answer is Vehicle NVH Prediction.
Ok, but what is that?
If you have never heard about it before, take a look at this blog:
If you are still here, the short answer is: it is a method that allows creating a vehicle assembly in a virtual environment, using test and/or simulation data to build the different components. You can then use that digital twin to synthesize its noise and vibration in different operating conditions and evaluate the effect of modifications or other components designs.

Well, this sounds like the answer to my initial wonder: OEMs can use this technology to assess the impact of integrating different types of electric drive units on the same vehicle and evaluate how the overall NVH perception will change.
Looking for synergy between test and simulation
This ‘sounds’ great, right? But how to make it happen?
The key to success is a good synergy between the physical and the digital world.
As I said before, component models can be coming from tests or simulation, depending on where we are in the development cycle and which data are available. Having a user-friendly ecosystem to combine those two sources of information is paramount for this approach to generate value.

Let’s integrate our Electric Drive Unit into the vehicle.
Now, let me give you a practical example of how to leverage this hybrid approach in Simcenter Testlab Virtual Prototype Assembly (VPA) to predict the NVH performance of a vehicle when integrating the Electric Drive Unit (EDU).
To do that, I will discuss 3 scenarios:
- Scenario 1: Full test-based approach, coupling EDU and vehicle test data
- Scenario 2: Hybrid approach, integrating the same EDU in different vehicle variants from CAE
- Scenario 3: Full CAE-based approach, coupling alternative EDUs to the vehicle
Scenario 1: Validating the methodology with existing components
First thing first: if you are picky like me, you want to start by setting up the process and ensuring the methodology works using elements that you have physically available. Hence, we will characterize an existing vehicle with pure test data.
We extract the e-drive loads (both structural and acoustic) from test-bench measurements using the component-based TPA methodology.
The next step is to gather frequency response functions (FRFs) measured at different levels on the ‘passive side’ of the vehicle (i.e. all the components downstream of the motor, such as the mounts, the axle-carrier, the vehicle body) to describe the transfer from the electric motor loads to the target noise in the car cabin.

These passive components are assembled together based on their FRFs with the frequency-based substructuring technique.
Finally, the noise sources extracted from the bench tests are applied to this assembly for predicting the in-cabin noise.
As you see in the results below, the synthesized noise matches very well with the measured one.

Now that I have given you some technical details, how can we practically use this model?
For example, to know if the noise we hear in the car is due to a pure acoustic problem or is caused by excessive vibrations of the drive unit.
For that, we look at the partial contributions of the structural and acoustic paths to see in which frequency range one is more relevant (and thus needs to be mitigated) than the other.

In this case, we have an overall strong acoustic contribution throughout the entire frequency range, with some specific peaks caused by structural loading.
Scenario 2: What if I change the vehicle trim?
Well, if I do that, I expect to hear a difference in the noise in the car, right?
Let’s see if my expectations are met.
For this second scenario, I built a vibroacoustic model of the vehicle in Simcenter 3D to simulate the FRFs from the EDU to the cabin. In this example, I have simulated a car without trim (just a regular firewall), and another with the trim included.

Then, I have coupled these two virtual vehicles with the same EDU characterized in my previous tests. And as expected, I see from the results that I need to add trim to the firewall to lower the cabin noise at high frequency (above 1kHz) and match the results I had from the original car I tested.

Scenario 3: Simulate design changes of the EDU
I’m still not satisfied: I want to see what happens if I change the design of my EDU.
As before, this is something I need to do in simulation.
Thanks again to Simcenter 3D, I can compute the acoustic radiation of the new e-drive and couple it with both vehicle configurations from the previous scenario.
In the CAE environment, I can move from current towards electromagnetic loads and near-field acoustic pressure to acoustic loads, and I can do that for all the design modifications I want to evaluate.

The power of this methodology is that potentially all sorts of combinations can be evaluated just by combining component designs from different sources, being them measurements or simulations results.
Towards subjective NVH evaluation.
In my examples, I could predict the vehicle interior noise target curves. However, that does not fully answer my original question: how will I perceive this car when driving it?
For that, I need to go one step further and listen to the car’s sound.
And yes, we do have an answer to that too: by loading the predicted noise results in our Simcenter NVH Simulator, I can just virtually drive the vehicle behind my desk and make a subjective NVH evaluation.
After all, following my first experience, I want to know in advance if I will be thrilled to drive that car or not.

Vehicle NVH prediction is already a reality.
So this ‘marriage’ between simulation and testing is happening, and we should be sure we are invited!
This is more than necessary nowadays to move to the next generation of vehicle NVH development, where relationships between the different test and CAE departments at the car manufacturers and component suppliers are crucial to ensure we (end users) will be pleased to drive cars in the years to come.
What’s next?
More reads, of course!
If you want to know more about this topic and how we address it in Simcenter, I suggest, as usual, a couple of nice resources you can consult:
Here, I’m discussing more in detail Road Noise and how vehicle NVH prediction can be used in that context:
This Webinar treats the component-based TPA method that is one of the building blocks of the technology I presented today:
Stay tuned for more!