What Is an Optimized Product Design?
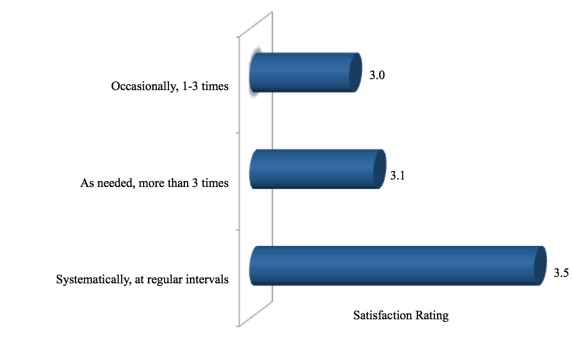
In my previous post, How Should You Use Simulation, I discussed how optimization is the top way Top Performers use simulation. Top Performing companies are those who, when compared to their competitors, are more efficient, design higher quality products, do a better job meeting cost targets, and are more innovative. See the post titled, Announcing New Research on FEA Simulation Bottlenecks for more information on how Top Performers were defined.
Products have become so complex, evaluating multiple design criteria, which may even conflict, can be very difficult. Identifying the right options for the best design is extremely hard. Simulation software makes this easier by simultaneously evaluating multiple variables, against multiple values, and coming up with the best solution for an optimized design. The software can very quickly come up with results that would take hours to calculate manually. This is why simulation is such a powerful tool for optimization.
But what exactly are companies optimizing? What does optimization mean exactly? Given its importance to Top Performing success, it is an important term to fully understand. With our recent study, Addressing the Bottlenecks of FEA Simulation, we dug into this a little further. We asked respondents how their companies define optimization. Figure 1 shows the results.
Figure 1 – What Does Optimization Mean Figure 1 shows that optimization most often means improving engineering performance. Companies are using simulations to guide decisions to help them make their products faster, better, stronger. Superior
engineering performance will help products stand out from the competition.
Companies also look to optimize their products for better economic performance. This is about improving product profitability. It means ensuring products have the innovative features that will drive customer demand and increase revenue as well as take costs out of the product. Companies use simulation to look at the best way to add new features while considering cost effective ways to implement them. Lowering costs may involve removing material or evaluating more economical material options, without compromising engineering performance. It may also involve adjusting geometry and topology to lower manufacturing cost or improve cycle time. There are many opportunities to take cost out of products, but without understanding the impact on performance, it can be difficult to identify the right ones. This is how simulation helps.
Better reliability is another top way companies optimize their products. By using simulation, they get better insight into when failures will occur. Optimization allows them to look at multiple criteria and make adjustments to avoid failures, which will lead to higher quality in more reliable products. Companies benefit from this by associating their brand with superior reliability to improve competitiveness.
Another area companies associate with optimization is innovation. Looking at multiple options means more ideas are evaluated. Expanding the funnel of considered ideas lead to greater levels innovation. You can build off of those ideas with simulation guiding the way, providing insight into what works and what doesn’t.
Light weighting is another important trend in product development. Less weight will improve energy efficiency. This can be an important way to make products more competitive because lower fuel consumption will lower the cost of ownership. In addition, tighter fuel economy regulations, such as what the automotive industry faces, require companies to look at multiple ways to improve fuel consumption. Reducing weight is an important strategy to accomplish goals for compliance. Lower weight can come from removing excess material or from using lighter weight materials. However, companies must make sure that when they do this, they are not sacrificing quality or compromising performance. Simulation can be a powerful tool to help consider all of these criteria to produce an optimal design.
The more you use simulation throughout the design process, the more opportunity you have to optimize your design. If your use of simulation is limited to looking for problems at the end of the design process, you miss out on opportunities for an even better design. In fact, people who use simulation more regularly tend to be more satisfied with it. We asked respondents how satisfied they were with the number of simulation iterations they run on their product lines. Then we compared that to how a regularly they run simulations. The results in Figure 2 show that those who run it systematically rate their satisfaction more highly.
Figure 2 – Satisfaction with Simulation Frequency What’s interesting is that although those who use simulation systematically rate their satisfaction with simulation frequency higher, there is still room for improvement. On a scale of one to five, with five being the most satisfied, they rate their satisfaction a 3.5. This shows that even they feel there’s opportunity to use simulation more. It is because of this, that it is so important to understand the bottlenecks that slow down simulation. By overcoming these bottlenecks, companies can use simulation even more and increase their satisfaction rating that much more.
For more insights and findings for ways to overcome these bottlenecks, you can download the complete report here (free of charge, registration required).