Auto suppliers should be using advanced planning and scheduling software (APS). Here’s why.
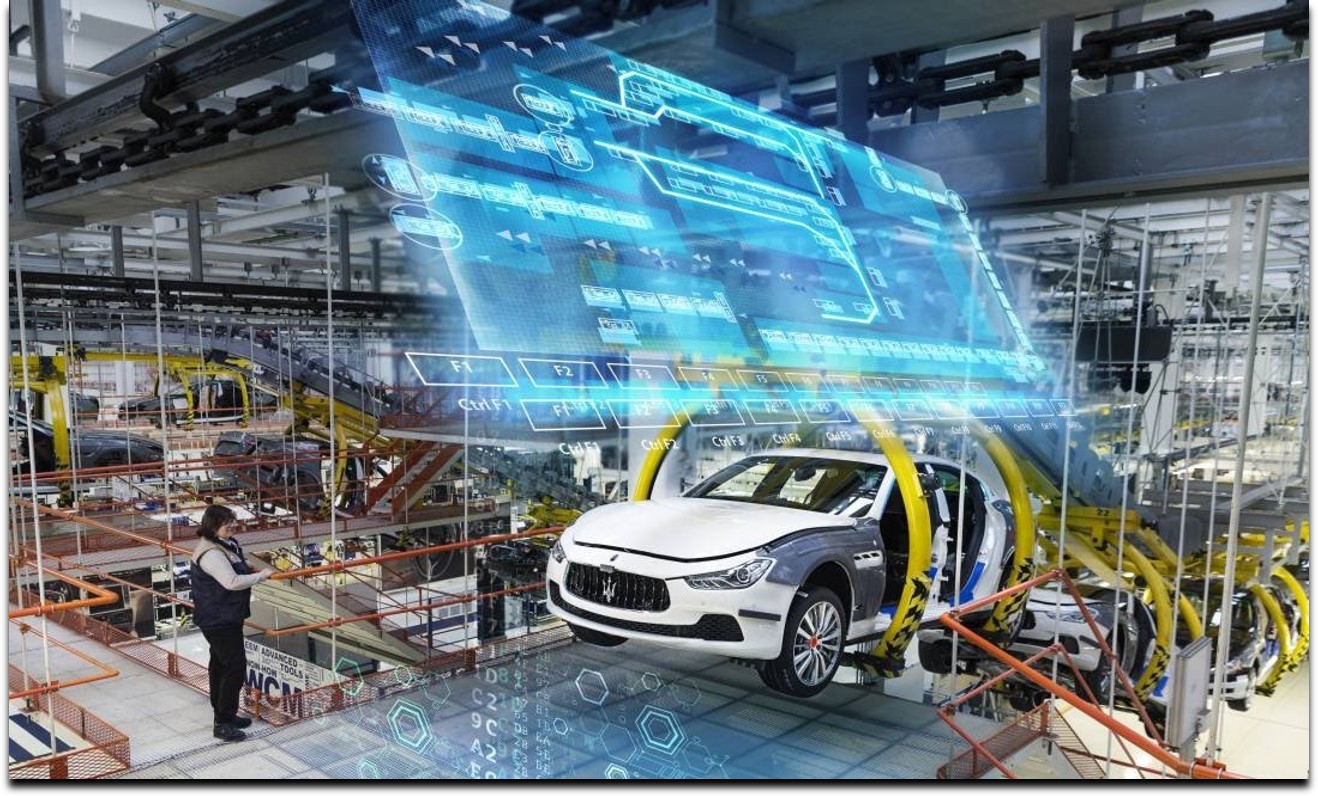
The automotive industry is experiencing a digital transformation that’s changing how cars are designed, built, and manufactured.
It’s up to every organization in the supply chain to adapt and adjust quickly to remain competitive.
Raw material providers, components companies, parts suppliers, and the manufacturers themselves are struggling to overcome the challenges the industry is facing.
Auto suppliers are adjusting with changes
The automotive industry is moving quickly, and it’s resulting in a number of new challenges:
Technological changes: Can our organization sustain a technological transformation?
Stricter regulations: How do we manage incoming changes while simultaneously staying ahead?
Customer demand: How do we plan production effectively and efficiently with fluctuating demand?
Limited resources: How do we make the necessary investments for the long term while remaining profitable in the short term?
Automotive suppliers large and small can overcome many of these challenges by using a holistic planning and scheduling approach.
A real-time scheduling system is a key element to achieve best-in-class results, higher process flexibility, precise on-time delivery, inventory reduction, and effective, efficient production.
Watch the original on-demand webinar in its entirety to learn more about APS software, how auto suppliers are using it, and how it compares to other solutions.
Think you can plan better than software? Try this interactive planning and scheduling game!