How advanced planning and scheduling systems can support supply chain management
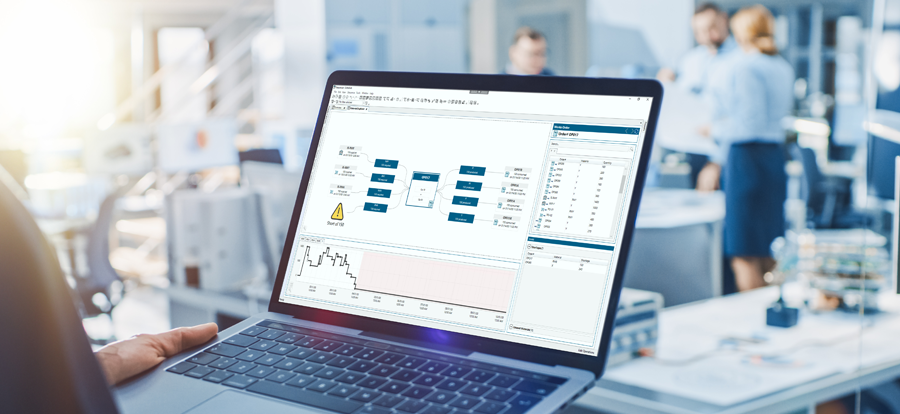
Even in the best possible conditions, production planning and scheduling are complex. Manufacturers constantly must worry about raw materials shortages, equipment breakdowns, strikes and other disturbances, and the ongoing COVID-19 pandemic has only added another layer to supply chain management challenges.
A holistic approach to supply chain management, often called the control tower approach, can help manage and mitigate risk and keep operations running smoothly even when disruptive events occur. However, special consideration should be given to the manufacturing operations segment, which can adversely impact both internal and external disruptions. Because of this, manufacturing operations are often considered the linchpin of supply chain management.
So how do you manage manufacturing operations to maintain a healthy supply chain? The answer is through advanced planning and scheduling.
Advanced planning and scheduling for supply chain management
Today’s advanced planning and scheduling software is designed to support a holistic approach to supply chain management. APS supports production planning in the following ways:
1.) Modeling the complex relationships and interactions within manufacturing environments
Manufacturing production has several factors that impact the planning process, such as warehouse space, machine availability and departments’ maximum work capacity. APS systems model these factors and their interactions to understand the most efficient production plan possible.
2.) Evaluating different scenarios quickly
An APS system allows you to test various scenarios and add constraints and boundary conditions to understand the impact on production. You can analyze how different scenarios impact key performance indicators and evaluate how supply chain disruptions affect manufacturing operations. Before they arise, you can understand the implications of all the possible “what-if” scenarios.
3.) Breaking down silos and fostering collaboration
Modern advanced planning and scheduling systems can manage inquiries from departments across the enterprise. APS systems can connect to the shop floor, enterprise resource planning, manufacturing execution systems and warehouse and logistics. They can provide planners with up-to-date information to make reliable predictions and collaborate with planners in different areas or plants.
Interested in APS for planning help in a complex supply chain?
Today’s complex and volatile manufacturing environment makes it vital for companies to take a holistic approach to planning and scheduling. An APS software solution, like Siemens’ Opcenter APS, can empower planners to model the impacts of supply chain disruptions and test scenarios to manage them. Download our free ebook to learn more about APS software for supply chain management.