Small and Medium-Sized Businesses Journey To Improve Manufacturing – The Role of Digital Solutions
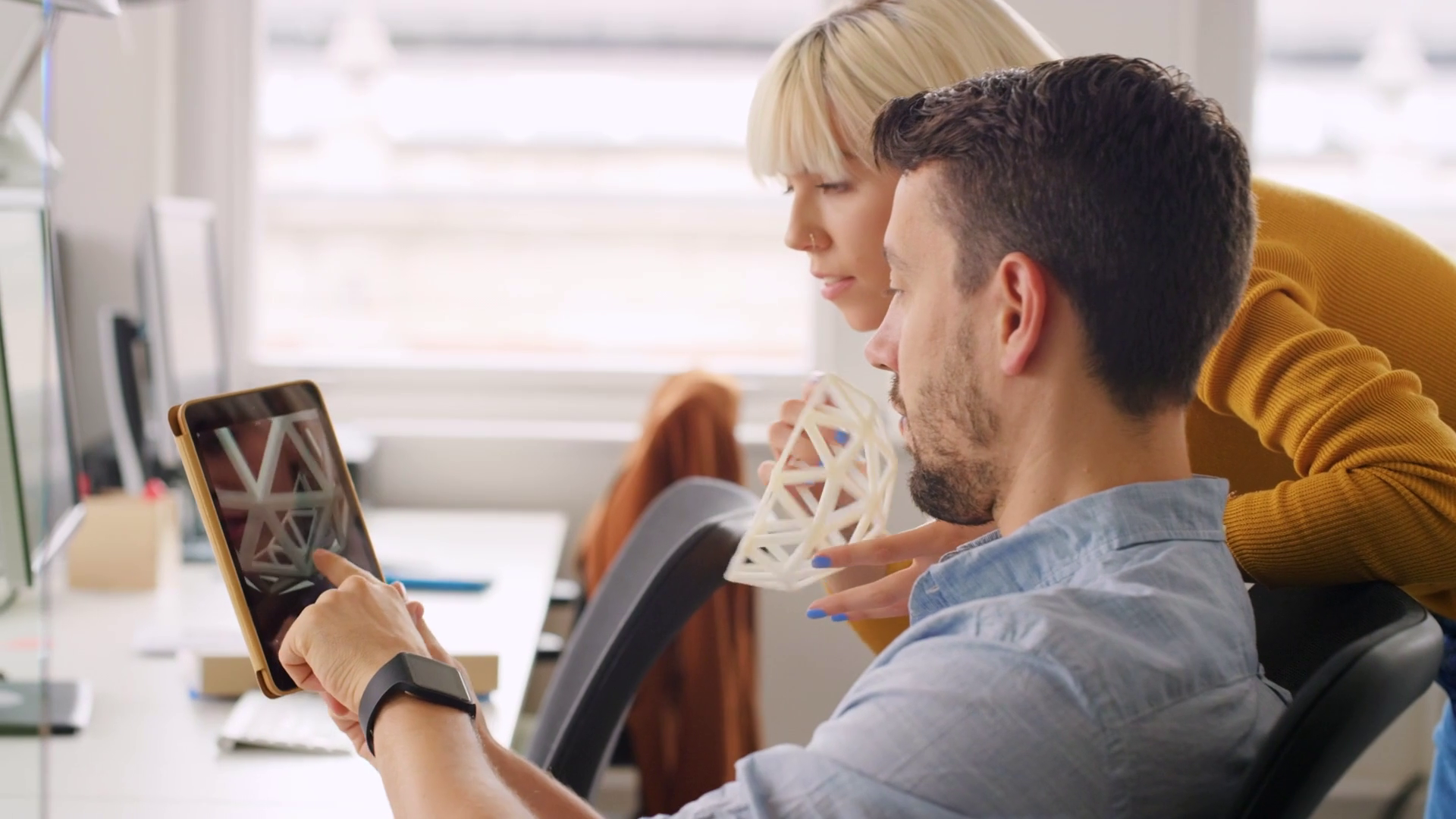
Manufacturers have their work cut out for them to stay afloat in today’s increasingly competitive global marketplace. Lifecycle Insights’ 2022 Flexible Manufacturing Study determined that executives are seeking to improve their manufacturing practices and operations to differentiate products, cut costs, improve quality, increase overall equipment effectiveness (OEE), and speed time to market. To achieve this, companies are increasingly looking toward digital transformation, particularly manufacturing-specific digital solutions.

Improve Manufacturing—Why Bother?
There are many ways organizations can improve manufacturing processes and operations, and it’s a worthwhile endeavor. Such improvements can result in better quality of products, higher production through automation, and data collection that increases the OEE of assets in production facilities.
Lifecycle Insights’ 2022 Flexible Manufacturing Study sought to understand what types of digital transformation initiatives organizations are undertaking to improve manufacturing. Survey respondents’ top initiative involved implementing manufacturing-specific digital solutions.
This post highlights how these digital solutions are helping companies make targeted improvements. It also details the benefits companies are seeing after deploying them.
Interventions to Improve Manufacturing
We’ve established that manufacturing improvements offer companies many benefits. But executives in small- to medium-sized businesses (SMBs) don’t have the luxury of investing in new initiatives without doing their homework first. They need to be sure that potential interventions will help them achieve their goals.
The 2022 Flexible Manufacturing Study revealed the top three interventions that progressive companies in the SMB space are using to improve their operations. Unsurprisingly, implementing new, manufacturing-specific digital solutions topped the list (48%). But this was not the only intervention of value. Forty-six percent of survey respondents also noted that they hired new talent to usher in improvements in manufacturing and 43% had made essential changes to their organizational structure.
This post is devoted to discussing the role of the top intervention: manufacturing-specific digital solutions. Since these solutions were the most popular way to improve manufacturing, it is crucial to understand what problems they can address—and how they differ from traditional approaches.
Manufacturing-Specific Digital Solutions to Improve Overall Equipment Effectiveness
Manufacturing organizations, especially SMBs, face a variety of production-related challenges. To begin, they must protect their production assets, including machines, factories, and other equipment, from unexpectedly breaking down.
Traditionally, companies would manage this task by performing periodic maintenance services. However, this approach involves shutting down production for days at a time. Organizations may also have followed a preventative maintenance policy calling for replacement of a few critical components in the factory, even if those components were still in working order. This meant extra spending that may not have been strictly necessary.
But when organizations use manufacturing-specific production tools, they can avoid maintenance shutdowns and extra costs. They can stream continuous product data, including quality, output, energy consumption, machine downtime, maintenance operations, and other key information, to an edge device or to the cloud. The solution monitors that data and performs analytics. Modern solutions even employ artificial intelligence and machine learning capabilities to help predict problems before they occur. These progressive solutions forewarn company executives about potential problems and allow them to correct them with minimal disruptions to production.
Manufacturing Specific Digital Solutions To Address Rapidly Evolving Customer and Market Needs
Manufacturers also need to be able to respond quickly to market needs. This may involve the addition of new machines or changes to existing manufacturing processes. It is important to be able to make such changes without disrupting current operations.
But traditional methods for adding new machines to the existing assembly line and changing existing processes left much to be desired. In the past, organizations used two-dimensional layouts to reorganize the factory floor. While these layouts allowed them to identify and fix space constraint issues, they offered no information about throughput or human-machine interaction issues.
Progressive solutions provide 3D simulation capabilities that allow users to visualize the entire manufacturing line—and its new machines and processes—on a computer. Such solutions can identify potential problems, allowing users to run multiple simulations to find the best fixes. In addition, because the solution works in 3D, users can also correct potential human-machine conflicts and ergonomics issues. Then companies can introduce new products or make necessary changes to the production set-up quickly, and with limited disruption to production.
Manufacturing Specific Digital Solutions to Improve Quality and Increase Output
Staying competitive today requires SMBs in the manufacturing space to produce higher quality products and increase output—all while using existing production facilities. Traditionally, companies relied on spreadsheets to monitor quality and other production-related parameters. But those spreadsheets can quickly become unwieldy, making it difficult to extract meaningful information to support decision-making. With multiple, large spreadsheets, executives are unlikely to spot trends or understand the origins of various problems.
Progressive digital manufacturing solutions, however, allow organizations to monitor production output and quality continuously. These solutions can aggregate data over the entire history of a product or facility to help executives identify patterns. Furthermore, such solutions automatically collect other essential data points, including energy consumption, temperature, tool wear, and maintenance routines. This can help executives better establish causal relationships and observe patterns that will help them resolve quality issues and improve output. Ultimately, when companies leverage these progressive tools, they can deliver superior products to customers while also enjoying higher profitability.
Conclusion
Today’s manufacturing organizations are looking for innovative ways to make targeted improvements to their manufacturing processes and operations. Lifecycle Insights’ 2022 Flexible Manufacturing Study demonstrated that progressive organizations are finding success by implementing manufacturing-specific digital solutions. By deploying these solutions, they can improve OEE, address rapidly evolving market and customer requirements, and improve product quality and output. Leveraging these tools is a particular boon for SMBs, who are looking to stay competitive by making improvements while maintaining their bottom line.