Best practices for working with faceted geometry and mesh bodies
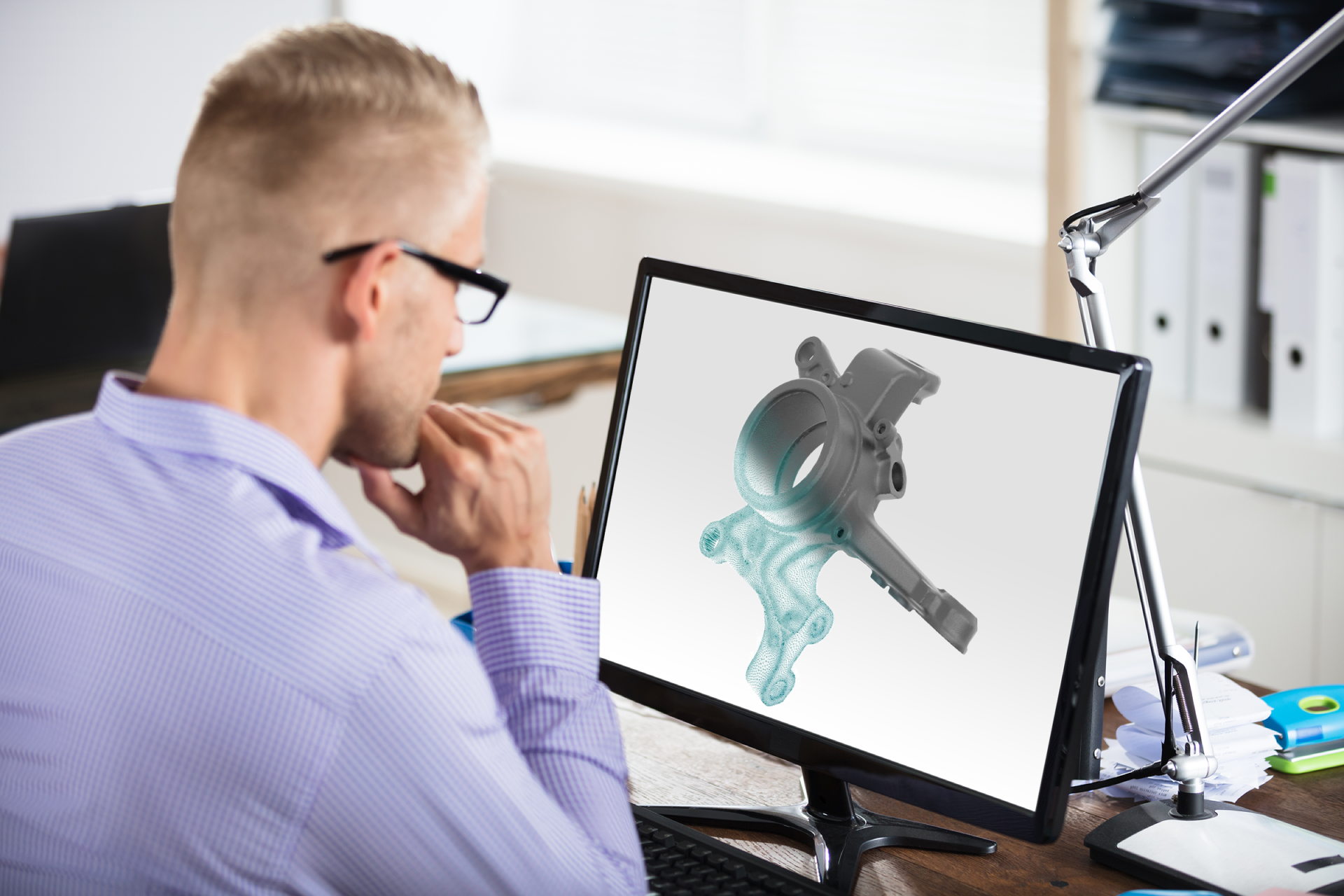
Four capabilities you need when mixing points, triangles, surfaces and solids
It is a new era for design. Engineers increasingly leverage new technologies in their design workflows, including 3D scanning, reverse engineering, advanced simulation, generative design and additive manufacturing to increase innovation and improve design. But working with the necessary faceted geometry mesh models can be frustrating. The inability of CAD systems to intelligently recognize and make changes to mesh bodies causes challenges in the product development workflow. How can you move mesh models seamlessly into your CAD system without time-consuming conversion or remodeling?
Technologies like 3D scanning, reverse engineering, advanced simulation, generative design and additive manufacturing improve our engineering workflows, save time, and result in better models. But the additional steps and tools required to manipulate mesh models for practical use can undo that time savings and hamper innovation. However, with the right capabilities, you can make mesh models work for you – and your CAD system.
The key to successfully using approaches like scanning, printing, advanced simulation and generative design lies in the ability to refine, modify, add to or remove geometry from these mesh bodies. Otherwise, engineers face lengthy, duplicative remodeling efforts. In our latest eBook, we explore the four capabilities you need to ensure every CAD user can work with mesh bodies, fix broken workflows, and ease the adoption of new technologies to accelerate innovation and improve design.
Take product innovation to the next level
Ready to try this new technology for yourself? Start a 30-day free trial of Solid Edge to explore the benefits of our market-leading product development software portfolio. Solid Edge seamlessly combines traditional “b-rep” solid models with triangular mesh models without time-consuming and error-prone conversions. Convergent modeling in Solid Edge allows for traditional b-rep operations on digitally scanned 3D data and models born out of generative design, reducing rework while supporting modern additive manufacturing processes for complex shapes.