3 Tips to Help Design Better, Cheaper Products Faster
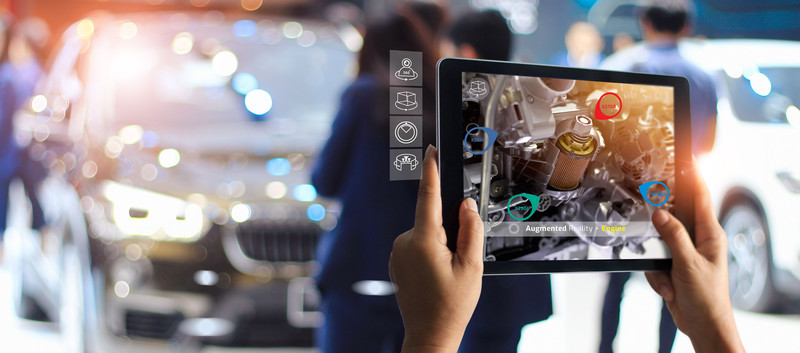
“I want to design better products, faster, and at less cost,” says…pretty much everyone. Of course, these are common goals. The challenge is, how do you actually achieve this? Let’s explore three CAD-related capabilities that can help make these high-level goals a reality.
1. The first capability is Model Based Definition (MBD).
MBD involves embedding product and manufacturing information (PMI) into the 3D CAD model to support downstream processes such as manufacturing, analysis, and inspection. Consequently, there are many ways in which it helps design better products, with greater efficiency, at a lower development cost. First there are significant time savings during product development because by using the 3D model, you do not have to waste as much time creating 2D drawings. Tech-Clarity’s How-to Guide for Adopting Model Based Definition found that engineers spend 33% of design time on drawings. Imagine if you could spend that time on better designs? The research also found that MBD offers several other benefits (see graph).
What’s especially interesting is that all respondents experienced benefits. The challenge, as a user revealed in Tech-Clarity’s research report, The How-to Guide for Implementing PMI, is that, “While easier to understand, in many ways PMI is different… It is an adjustment going to 3D models.” The adjustment is for those downstream users of MBD who have to adapt the way they operate, and may be resistant to the change.
To overcome this cultural resistance, software that makes MBD easier to adopt will help. Training those in manufacturing how to use a CAD viewer can be difficult and may even require hardware investments to view the 3D CAD model. However, if manufacturing can access the CAD model in software they already use, such as a 3D PDF, it can help. This is especially true if the software will work on inexpensive hardware such as tablets.
2. Another area is 2D nesting.
Material cost is one of the most significant cost drivers of a part. Consequently, finding ways to get the maximum number of parts from the least amount of material can be an excellent strategy for reducing cost. Nesting can be a way to achieve this. It optimizes the layout of the cutting pattern on flat fabrication materials such as sheet metal, wood, plastics and textiles to minimize material waste. Imagine the cost savings if you could reduce scrap by just 10%. Not only will you need less stock material to produce the same number of parts, but you also save on shipping and carrying costs. Excess scrap also has an environmental cost, which nesting can also help you avoid.
The challenge is that it can take a long time to figure out how to best optimize the nesting pattern. Plus, as the most experienced engineers approach retirement, the knowledge of how to best design parts to minimize scrap and optimize pattern layouts will be lost.
However, CAD software with 2D nesting capabilities can accelerate the process by automatically calculating the best layout to reduce scrap. This will save engineering time while enabling manufacturers to benefit from the significant cost savings of reduced scrap. Also, as embedded CAD functionality, less experienced engineers can use it as a design tool. If they have better visibility to the optimized layout before production, they may be able to identify opportunities to adjust the geometry for further optimization to minimize scrap.
3. The final capability is augmented reality.
Augmented reality (AR) involves enhancing an existing real-world environment with additional computer-generated information. In a design context, it can involve embedding a 3D digital model that doesn’t exist yet in its intended environment so that you can interact with the model the way you would in the real world. This is different from virtual reality (VR) where everything, including the environment, is computer generated. Typically, AR involves hardware such as a tablets, smart phones, or glasses to allow you to view and interact with the model.
For design, AR is still in the early phases of its adoption curve. However, AR has the potential to fundamentally impact how products are designed in ways that will empower engineers to develop better products. First, the hardware required to support AR continues to drop in price, making it far more accessible. Also, the software continues to become more powerful and easy to use, creating more potential for its use. Now, AR software has become available to work directly with CAD models.
During design, AR can help engineers make better decisions and solicit more feedback to improve designs before physical prototypes are created. While going from 2D to 3D CAD made it easier to visualize a product, AR takes this even further so engineers and potential customers can interact with the product before it exists. Engineers can assess usability and functionality to inform their design decisions, which will lead to better designs. Customers can provide feedback to make the product design even more appealing.
So, there you have it. Three very different technologies, but each can make a significant contribution to help you design better, cheaper products faster.