Advanced manufacturing techniques to accelerate CNC machining
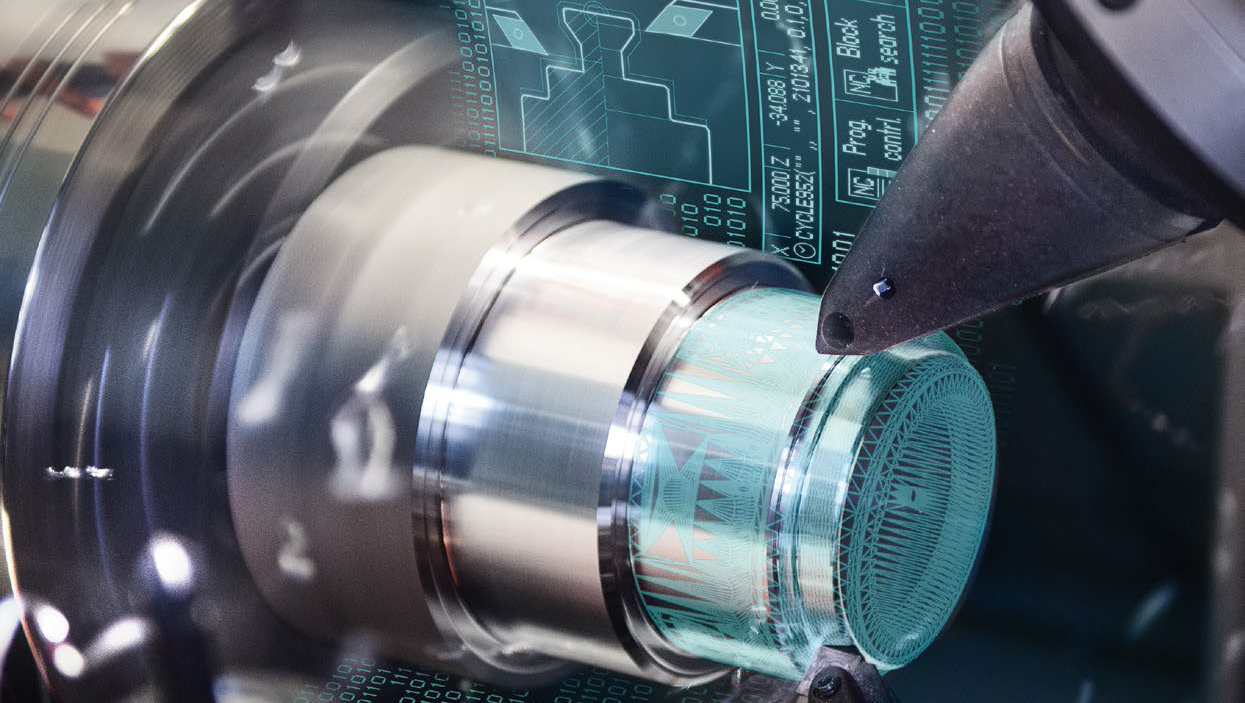
Computer Numerical Control (CNC) machining has become increasingly common in the manufacturing world. CNC technology offers a versatile, automated means to produce large-volume runs of high-quality parts. The high levels of accuracy and repeatability offered by CNC machining processes make it an ideal tool for most manufacturers.
In general, CNC machining refers to one of many reductive processes that take material away from a workpiece to fulfill a design. CNC processes use computerized controls to handle the entire machining process from start to finish, ultimately producing consistently precise parts. CNC machining equipment can follow the same sets of instructions over and over again to facilitate small or large production runs of identical pieces.
CNC machining is used to create parts and components for almost every industry and application. This includes the aerospace industry and other highly complex industries that need machining work on large parts. Manufacturers can use this process on substrates such as composites, foam, glass, metals, plastics, and wood.
This method of machining is particularly advantageous due to its automated functionality. Automation allows the machines to operate self-sufficiently, requiring less human labor to produce accurate parts. A growing industry shortage of skilled machinists and laborers has been a primary contributor to the advancement of CNC technology in recent years. The predecessor to CNC machining—numerical control (NC) machining—used punched tape cards and rudimentary commands. CNC machining follows more complex commands and uses a greater variety of controls. These systems both instruct the cutting and forming tools that remove, but CNC machining equipment can follow complex, customized sets of instructions that come from complex computer-aided design (CAD) or computer-aided manufacturing (CAM) designs.
Accelerating CNC machining jobs
How do you speed up CNC machining without sacrificing safety or control? Time is of utmost importance for machine shops; the faster they complete jobs, the higher their revenue. For NC programmers, that not only means producing toolpaths quickly, but producing toolpaths that run fast.
At the end of the day, machine shops are only as profitable as the number of jobs you complete. But taking on too many orders and failing to complete them – or to meet customer specifications – can cause long term damage to your trust and credibility. The only way a job shop can assure profitability is to fill its roster, perform quality work, and move each job through in a timely manner. This straightforward formula for job-shop success puts NC programmers under pressure to get toolpath creation done quickly and done well. Programmers and the manufacturers they work for have long relied on CAM software, but now they’re asking more from their CAM programs than ever before.
In our latest eBook, we explore the key trends driving the need for speed and new advanced techniques and capabilities that can help you achieve your machining goals. These include high-speed machining, feature-based machining, toolpath simulation, and working associatively with your designs from any CAD application.

eBook
Better, faster machining
How do you accelerate CNC machining without sacrificing safety or control? Advanced machining techniques embedded in modern CAD/CAM software applications can help you significantly speed up machining and reduce time-to-revenue.
Choosing the right CAD/CAM solution for CNC machining
We explore this in greater detail in the eBook, but it’s worth noting that improving profitability isn’t just about creating toolpaths fast – it’s also about creating toolpaths that run quickly. This is how you shorten your time to payment. Advanced CAD/CAM applications provide you with critical capabilities that help in this regard.
High-speed machining supports new machining centers that run at higher rates. Feature-based machining applies sets of toolpaths with embedded best practices to accelerate machining. Modern CAD/CAM applications must support both.
Automation is important, but control is paramount. Your programmers need to have the ability to change toolpath parameters at a high level, but they also need to have the capability to change individual moves in the toolpath. This is another area where modern CAD/CAM applications have to support both needs.
No machine shop can afford broken tools, jigs, and fixtures. Simulations virtually run toolpaths to check for collisions so they can be addressed before they are run in the real world. That eliminates costly mistakes on the shop floor. This is yet another area where modern CAD/CAM applications offer these key capabilities.
Machine shops get models in a huge range of CAD formats. Modern CAD/CAM applications must be able to open all those models so they can build out toolpaths to machine them.
Address your CNC machining requirements with Solid Edge® CAM Pro
You can address all types of CNC machining requirements and provide the right tools to manufacture today’s products faster and more easily with Solid Edge® software. Solid Edge offers comprehensive solutions for machine tool programming, from simple NC programming to high-speed and multi-axis machining.
Solid Edge® CAM Pro, a capable, proven computer-aided manufacturing (CAM) solution from Siemens, features a rich set of tools to help you finish the job right the first time. Solid Edge CAM Pro is a modular, flexible configuration of numerical control (NC) programming solutions that allows you to maximize the value of your machine tools. CAM Pro provides powerful NC programming with a low total cost of ownership and is easy to deploy, learn and use.
To learn more about Solid Edge, download the eBook or visit solidedge.siemens.com.