Best practices for complex shape design
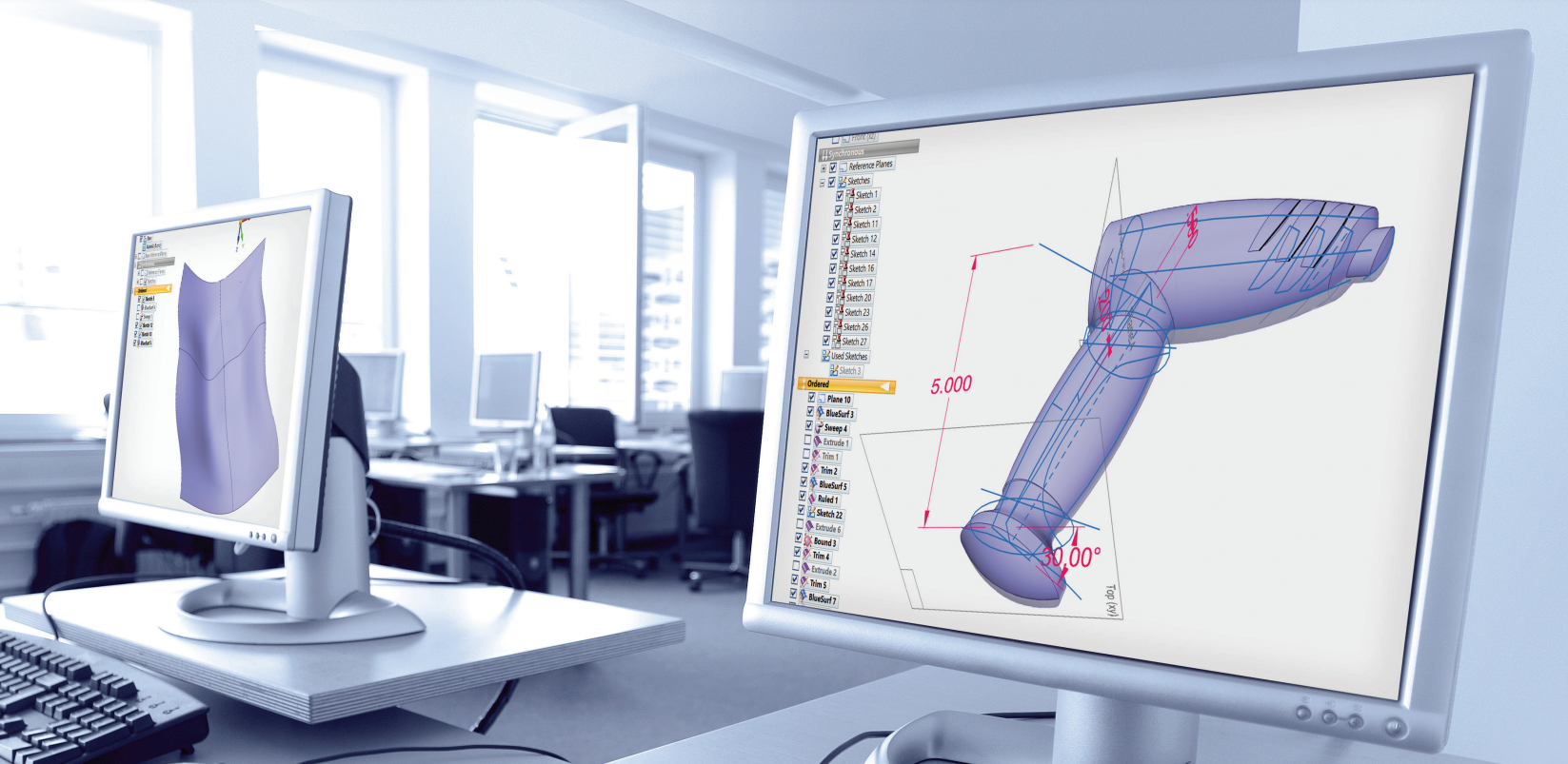
What are the best ways to design complex shapes with CAD tools? Computer-aided design (CAD) provides the ultimate medium for communicating concepts – but complex shape design can be challenging for many designers. Best practices can differ across industries and between companies, so it’s hard to find consensus on rules and guidelines. Fortunately, some general principles for complex shape design are nearly universal, or apply in many cases. Recommendations of any kind should be taken a grain of context: designing automated machinery is different from designing medical equipment.
Design happens in the mind
New concept design requires practical communication skills – visualization, modeling, requirements, aesthetics, ergonomics and regulations. CAD provides the ultimate medium for communicating concepts – CAD data accelerates engineering and manufacturing and can improve efficiency throughout the product lifecycle. Complex shape design is an essential skill for concept design.
CAD details the specific shape and properties of each part and how they go together. The data is used in downstream applications that range from rendering to repair. The one constant is change, yet change is the most difficult thing to plan for. Design intent is the process in CAD that helps with planning for change, and while much has been written about design intent in both history- and non-history based systems, it’s still an elusive beast for many users.
In our latest eBook, we introduce universal principles and best practices for complex shape design that you can implement in your projects today, including layout and master model techniques, best practices for ordered modeling, as well as simultaneous workflows and data management. Download the eBook →
Experience the power of cloud-enabled 3D CAD
Solid Edge is a portfolio of affordable, easy-to-use software tools that addresses all aspects of the product development process – 3D design, simulation, manufacturing, data management, and more.
Solid Edge has a complete set of history-based tools and offers legendary capability in the areas of sheet metal design and 2D drawing and drafting. In addition to these traditional history-based tools and techniques, Solid Edge also has the unique capabilities of synchronous technology, a set of order-independent enhancements on top of direct editing. Parts can be entirely or partially built using either synchronous or history-based methods, and these features can be edited in the context of an assembly. With the option to move between synchronous and history-based paradigms, Solid Edge delivers the unique capability to tailor best practices to the specific type of work a company needs done today.