Designing precision fabricated products at Mezco Fabrication
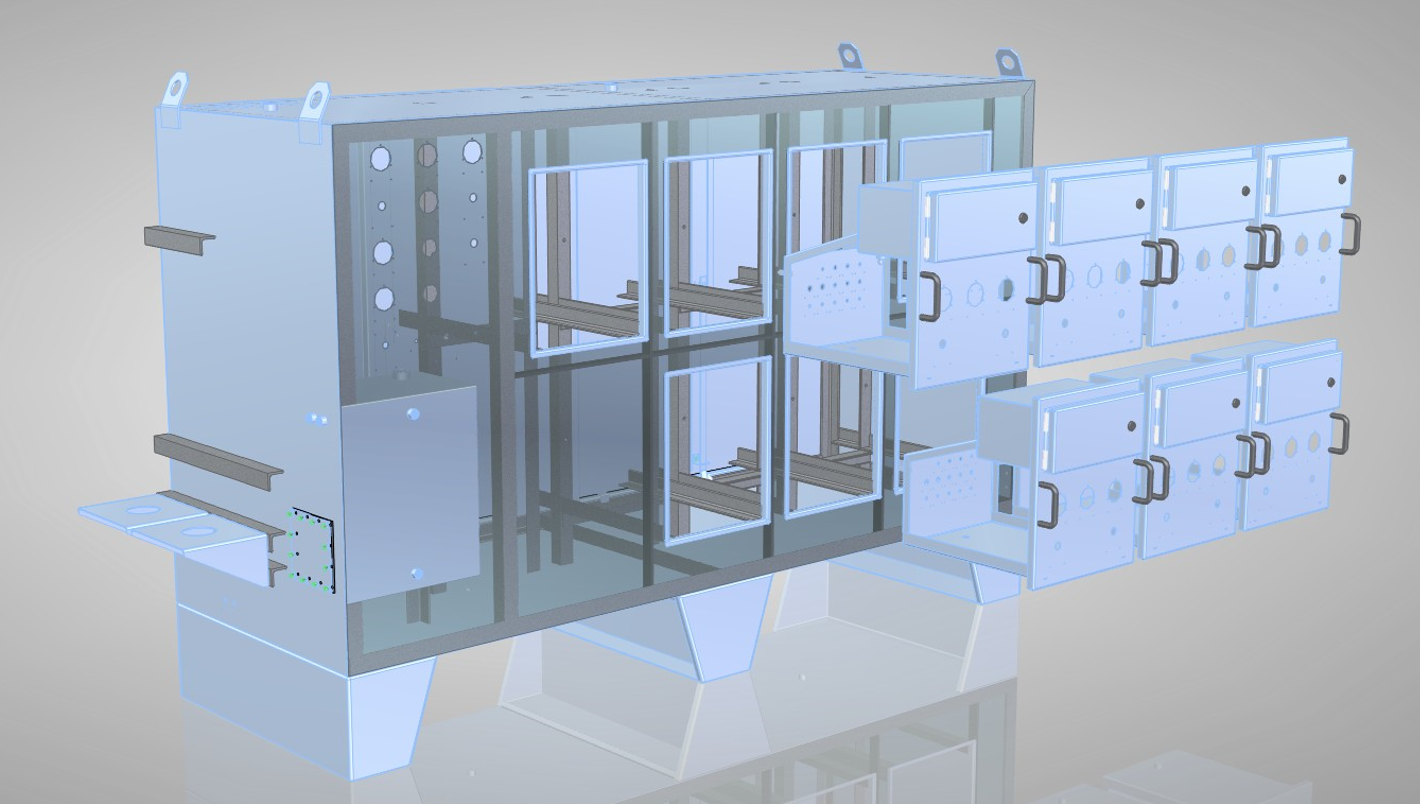
I met with Bryan Lagrange from Mezco Fabrication recently at our offices in Huntsville. Bryan has been a long-term user of Solid Edge and we discussed how he applies Solid Edge to the design and manufacture of precision fabricated products.
Mezco Fabrication recently celebrated its 15th anniversary and is a precision sheet metal job shop based in Lafayette, Louisiana in the USA. Their manufacturing equipment includes 2D CNC cutters (laser, water jet & plasma), CNC machining machines (mills & lathes), CNC press brakes, and comprehensive welding capabilities including FCAW, GMAW, GTAW equipment for welding of aluminum, stainless steel, and steel fabrications. At their primary facility they do cutting, machining, bending, and precision fabrication. At another location they do heavy fabrication work for skids, stairways, pipe welding, and well head landing bases.
As Bryan explained, “Since Mezco is a job shop we do not create products for ourselves but cut and fabricate parts for our customers in the oil and gas, power sports, marine, residential and commercial projects, and consumer product industries.”
Long-term user of Solid Edge
Bryan described Mezco’s long-term use of Solid Edge: “We have used Solid Edge from the inception of the company and I personally have been using Solid Edge since version 7 in 1999. The key capabilities I rely on are its sheet metal and 2D drafting capabilities, importing designs in other CAD formats, and part and assembly modeling environments. Of these, sheet metal and draft are used the most.” Mezco Fabrication are supported by Swoosh Technologies, a Siemens Smart Expert Solutions Partner with specific expertise in supporting manufacturers using Solid Edge.
Comprehensive sheet metal design and flat pattern creation
Bryan emphasizes, “Sheet metal has always been a strong point of Solid Edge. It is one of the reasons why we selected Solid Edge in the beginning. The many sheet metal functions and the ability to create accurate flat patterns are critical to our business. Solid Edge delivers every time. Sheet metal features include straight bends, lofts, rolled parts and features for stamping of sheet metal parts.”
Bryan continues, “The flat pattern capabilities allow you to prep the flat pattern for downstream 2d cutting operations. For example, by removing features such as the outer diameter of countersinks and counterbore holes, and adding break off tabs for bending purposes. Also adding laser slits for relief of features near stretch zones of bends. These features added in the flat pattern do not affect the final formed 3D model.”
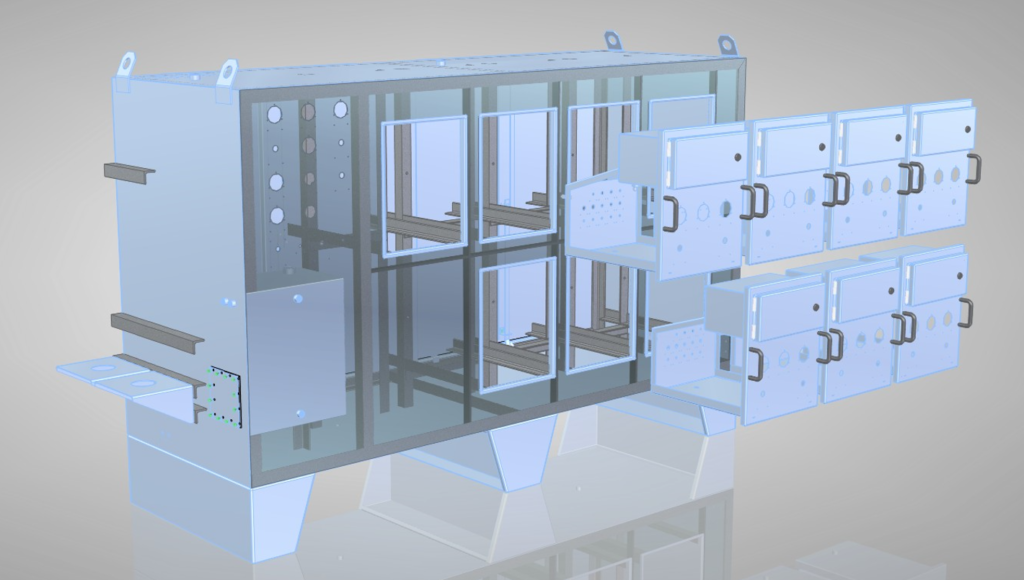
Convert a 3D model to sheet metal
Another key feature that Bryan uses extensively is the “Convert to sheet metal” command. “I can drop a customer’s imported CAD file into one our dedicated sheet metal templates. Then I use the convert to sheet metal tools, and create a flat pattern that adheres to our cutting and bending specifications in seconds.”
2D drafting is still important
Bryan adds, “One item that I believe is one of the best in the industry is the 2D drafting environment. Since we receive many .dwg and .dxf files from our customers, it is critical that we have a 2D environment that supports these file types. The ability to draw in 2D and have a production-ready draft without having to create a 3D model streamlines the process. You do not need a fully featured 3D model if you are creating something as simple as a flat plate with holes in the corners. The output needed for our CAM software is a .dxf file. I can simply sketch the geometry in draft, add dimensions, and export as a .dxf file that is ready for processing.”

Working easily with customer data in 3rd party CAD formats
Working easily with designs in 3rd party CAD formats is also important for Mezco Fabrication. “Solid Edge can open a variety of 3D CAD formats which is key for a job shop. Our customers use a variety of CAD software. I don’t have to ask them to export their work to a STEP file or other 3rd party format. I can open their native files directly, saving them time when communicating with me. Solid Edge has great capabilities for working with these non-native 3D models. Synchronous technology gives me a lot of direct editing commands to push, pull, rotate, and delete features,” said Bryan.
Assembly design
Bryan concludes, “Another item where Solid Edge excels is the interference detection capabilities within the assembly environment. Sold Edge can create the interference area as a solid body. I can use this as a guide to sketch around to fix the interference. For parts that meet at perpendicular or 45-degree angles it is easy to calculate how they need to be trimmed. However, when components are coming from different angles, this is where creating an interference body saves me time. I simply have these items interfere with each other. I use the interference body to show me where I need to trim each part so they fit together correctly.”
