Leveraging academic creativity for new product development
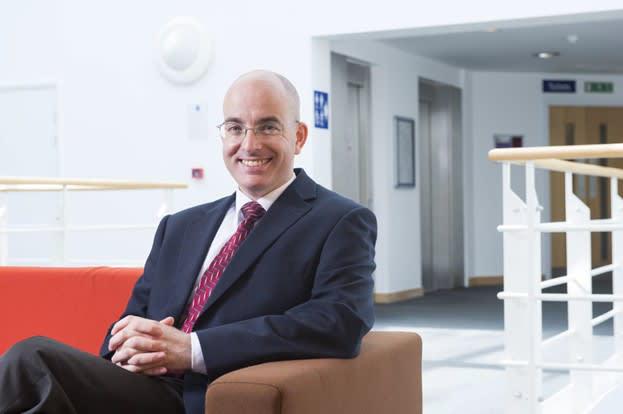
Surrey Sensors uses off-the-shelf components to create smaller, smarter sensor systems
Crossing the divide between academic engineering and creating products for profit can sometimes be a nonstarter for lots of truly profound ideas. After all, many businesses have a vested interest in creating products that make money, while academia is often rooted in concepts and research.
But there are businesses that have successfully bridged the chasm between academia and the market.
David Birch, Ph.D. is an instructor at the University of Surrey in the U.K. and the director of research at Surrey Sensors Ltd., which was spun up out of the university.
“At the University of Surrey, we host the National Facility for Atmospheric Boundary Layer Simulation,” Birch explained. “It’s a unique facility that allows us to work in a wind tunnel and reproduce the conditions that you get in the atmosphere. This includes variations in speed and temperature with height. Because the facility is unique, in order to make measurements inside it, we also had to develop entirely new ways of measuring things.”
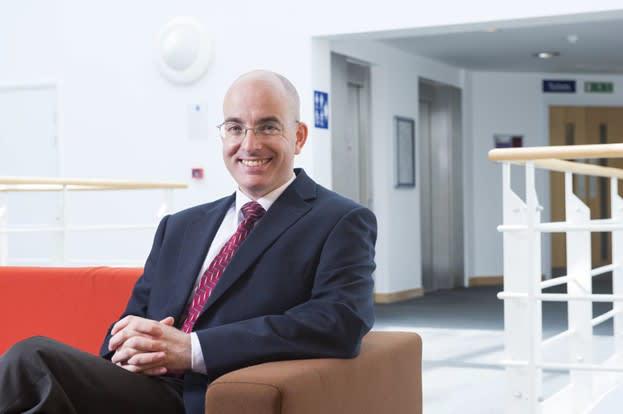
Surrey Sensors Ltd. was formed back in 2015, as a spin up out of the university that was using their IP and know-how to make it possible to use mass market components to create extremely sensitive and unique measurement tools.
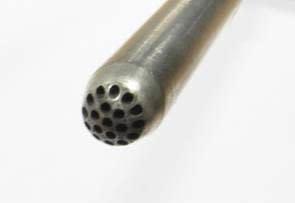
“One of the specialized instruments that we build is used for measuring the air speed and the direction from which the air is coming,” Birch said.
“These multi-hole pressure probes have been around since the 1920s, though they have advanced over the years,” Birch explains.
“We’ve found a way of packing all of the plumbing and electronics into really small spaces. We’re also building them out of sensors that are not particularly expensive so we can offer them at competitive prices.”
Using Solid Edge to develop new sensor technology
Birch explained that Surrey Sensors’ use of Solid Edge spawned directly from the University environment. “We teach using Solid Edge here at the university, but it had a valuable addition to our company as well.”
Much of the work that Surrey Sensors does involves making things as small as they can possibly be. “Thanks to the latest advancements in additive manufacturing and 3D printing, the geometry of small, complicated parts is no longer constrained by the limitations of conventional CNC machines. With a 3D printer, if you can model the part, you can make it,” Birch said.
“We have some extremely complicated geometries; things like manifolds that fit in a very small part and have to take multiple pressure lines from one point to another in a very, very tight space. We now design these parts in Solid Edge with very complicated cutlets. For the sort of work that we’re doing, it’s not sophisticated assemblies; it’s not complicated machinery. Part of the value of Solid Edge is that it is intuitive. When training people to use it, it takes very little time. We hire an engineer and within a couple of days, they’re able to jump in very quickly.”
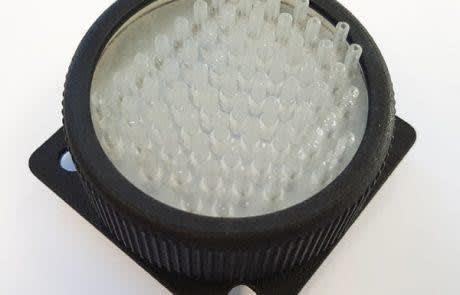
“It seems that regardless of what platform they’ve been trained on, our design engineers seem to pick up Solid Edge relatively easily. The transferability from other platforms is pretty straightforward.”
David Birch, Ph.D., Surrey Sensors Ltd.
For more information about Solid Edge for Startups and how to get a free trial of Solid Edge, visit solidedge.siemens.com.
Comments
Leave a Reply
You must be logged in to post a comment.
Thank you for sharing your story with us, David!