Modern Designs Bring New Heat Transfer and Fluid Flow Challenges
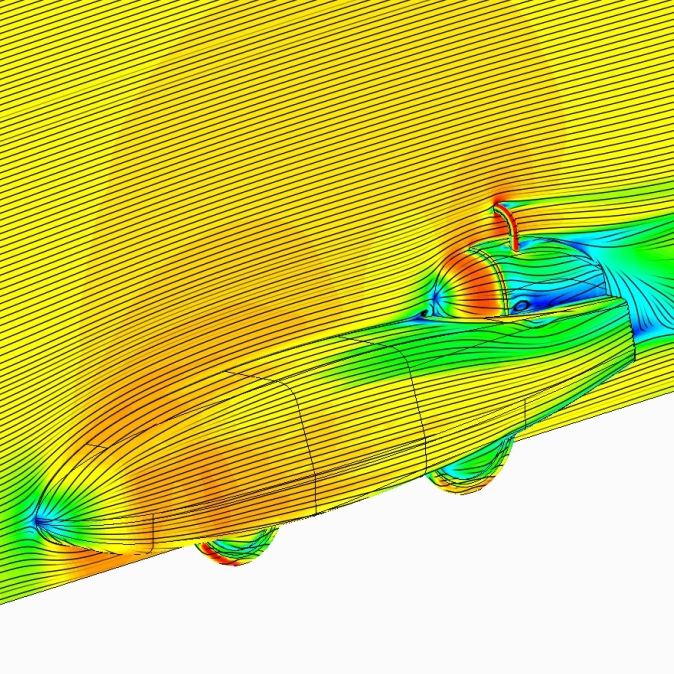
Examples of product designs where heat transfer and fluid flow analysis is essential to optimize performance
As consumer products evolve, so do the heat source, heat transfer and aerodynamic engineering challenges they bring for their designers. And the same is true for nearly all engineered products. For example, smart phones, smart watches and tablets require ever-longer battery life. At the same time denser electronics packaging and smaller, thinner devices increase the risks of failure, and maybe even fire. The original Samsung Galaxy Note 7’s lithium ion battery, for example, was tightly packaged into the smart phone’s casing. The battery was squeezed at its upper right corner, making it easier for its positive and negative electrodes to potentially touch and heat up.
These types of failures, coupled with continued consumer demand for smaller, faster, thinner electronics triggers stricter regulations applied not only to product development but also to testing and in certification standards. The tight packaging of slim smart phones increases the complexity of the heat transfer to cool processors, display and battery. The analysis solutions product designers depend on to solve these complex challenges are vital to engineers, and they need to be at the ready early in the design process.
Heat source, heat transfer and forced cooling are all essential considerations in the design of smart devices
For another example, from the world of the perhaps more mundane: the vacuum cleaner. They’re usually tested against their competition in terms of suction. That’s the reason cyclone-based vacuums are all the rage. They don’t lose suction performance over time. To get to that best-possible product: the vacuum with the greatest amount of suction, or the smart phone with a small, yet safe, profile, engineers need to optimize geometry for heat-transfer and for fluid flow, including airflow.
Heat transfer
Heat transfer is a particular challenge during product design because, while an engineer has many possibilities to improve heat transfer to keep devices operating within safe temperatures, usually all of them come with side effects. The possibilities to improve heat transfer include:
- Use a more expensive material with better heat conducting properties
- Leverage a larger surface area for improved heat transfer into the external environment
- Apply forced cooling flow instead of natural convection
- Use a better cooling fluid, such as water rather than air.
The side effects of implementing these possibilities may include:
- Additional expense
- Increased weight and larger size
- Greater power consumption
- More complexity
- Impracticality (consider a liquid-cooled vacuum cleaner or smart phone!)
Understanding how to make choices and trade offs for best performance without unwanted side effects is a critical challenge for designers.
Aerodynamics
Aerodynamic analysis of vehicles including this Greenpower Challenge electric vehicle is used to improve energy efficiency and minimize noiseAerodynamic design challenges apply to many products from airplanes and cars, to the design of the propeller blades for a household fan, the ducts of an air conditioner, or the cooling fan of a computer.
Fluid flow analysis enables part geometry to be designed so that airflow passes through or over it without high energy losses, while still providing the desired performance for cooling, suction, or pressure.
The Best Design
Engineers who use Siemens Solid Edge can now benefit from FloEFD for Solid Edge from Mentor Graphics. The pairing allows engineers to quickly prepare and analyze their CAD model for optimum heat transfer and aerodynamic performance without the need to translate the data or prepare a separate fluid body CAD model. The analysis allows engineers to determine if their design is subject to excessive turbulence, vortices, or other fluid-flow issues that decrease performance.
With FloEFD, the usually invisible air or liquid flow can be made visible, letting engineers see temperature distribution, flow velocities and direction, and other parameters, which are depicted together and in every area of the product. This depiction points out the problematic areas where changes can be made to improve the performance of the product.
This is the first in a series of posts that will discuss the new design challenges around heat transfer and fluid flow, the FloEFD for Solid Edge solution from Mentor Graphics and a detailed look at the “front loading” design process that enables the analysis to be performed and applied earlier in the design process.
Comments