Plan it or Wing it?
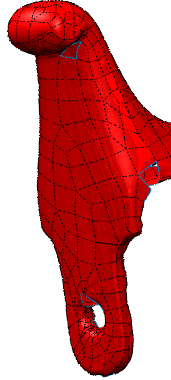
When you start a new model (this can mean either a complex single part or an assembly), do you plan out your approach to the model, or do you just start working? And if you plan it, is it a formal plan or just in your head? To some extent your approach to planning vs winging may be based on your personal style or on your company’s product development process.
I’ll give some examples of how I’ve worked both ways. At one point I did some work for a well-known commercial goods manufacturer, and they wanted to create a line of commercial carts.My role was “the CAD guy”, which to them meant someone that created tool-ready 3d geometry and inspection drawings by integrating the input from various departments, including marketing, product management, pack/ship, industrial design, production, mold tooling, purchasing, engineering, assembly, etc… One person is responsible for the project model(s) from top to bottom in their development process.
These carts had to have drawers, doors, one version with a big lid, one with a fancy handle. This configuration information came from a list of ideas that spawned sketches that the industrial designers came up with as they sat with a product manager and a marketing person. The sketches aren’t as detailed as to contain a parts list, but these guys have been doing product development for a while, so they know that a sketch of a drawer face implies a drawer front, a drawer tray, two slides, a lock, and a number of screws, as well as the tipping prevention mechanism and some sort of a multi-part housing. So even a rough idea is starting to flesh out the details.
Some of the internal structure of the carts had to be metal – sheet metal to be more direct – but the bulk of the cart parts would be plastic. This gave us a lot of lattitude for stylistic elements that are more difficult (read expensive) in metal. Consequently, a good part of what we needed to do was design a stylistic facade with a functional drawer pull and attachment.
So this project demonstrates both planning for the overall structure of the assembly, and winging it, for the individual style of some parts. When you are working on parts, the planning involves a lot of design intent because you know the parts may change in some detail or dimension, but in general, they will hold to the plan. This obviously takes a lot of fore-thought and discipline. One of the parts of planning is a date. My time with this company always had an end date, and I had to get everything done by that time. A finish line. As engineers, we always want to make things perfect, and to keep going until everything is correct, but as part of a product development team whos eventual goal is to sell goods to pay for our salaries, we rarely get the luxury of making a product really perfect.
But what about when an entire project is done on the “wing it” philosophy? I’ve got an example of one of these as well. I did some work for an independent inventor, who was also an anaesthesiologist. I worked on his projects for years, and made several versions and sizes of devices which it might be difficult to visualize how they work or how how they were made. When the doctor first showed me his design, I was skeptical. These devices are hollow and made from highly flexible silicone material.
Because these parts were meant to mate up with internal body organs, the shape was decidedly organic. And because they were also inflatable, they had to be hollow. And the inside had a different structure than the outside, so they were very difficult to visualize, and you couldn’t use simple parametric techniques such as offset surfaces or shelled solids. Every surface was hand made, literally inside and out.
This project had no plan, aside from each design needed four or five sizes. We would visually make a design. 3D print it, try it out on anatomical models and cadavers, tweak the shape (for all sizes) via hand sketches on pdf, and repeat the process. Both the product development process and the modeling process were definitely in the “wing it” regime. The work was frustrating and painful. Just the visualization methods I had to use for the models were time consuming. I frequently had to completely remodel sections because the original approach I used would stop working for new designs. This was when there was very little actual design intent going on, and showed the limitations of parametric methods for organic design.
One of the things I found with winging an organic model in a parametric CAD tool was that often I would get to the end and decide that I needed to redo the entire model to get rid of all that “history nastiness” that happens when you wing it. Anyone who has done organic design in parametric CAD probably knows what I’m talking about here. Feature in the tree that take up rebuild time, but do not contribute to the final model. Reference geometry, unnecessary geometry, geometry related to features you removed last week. This is because you create a lot of relationships that you didn’t intend, can’t figure out, and mysteriously have additional dependencies that you can’t remove without deleting features you want to keep. And you really don’t want a messy model going out with your name on it, do you? So you wind up recreating the whole thing.
Or, sometimes reverse engineering the organic model is the better way to go. It offers a different set of tools sometimes better suited to that sort of work. But that’s a discussion for a different post. Just want to leave you with one thought here – History based tools are ok for winging it if you don’t anticipate making big changes in the way design intent works. If you need to wing it because of the way your product development process works, and you have to work with history based tools, you may wind up making a “development” model and a “production” model.
Synchronous is a great tool for winging it with prismatic models, which covers most of the people reading this article, probably. If you need to work with more organic shapes (like this reproduced part from a brass antique shown to the right), you may need other tools. And we’ll talk more about those later.
Comments