Solid Edge History – V1 to V5
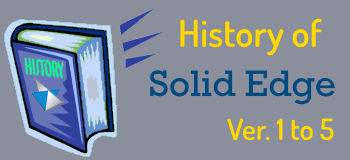
On April 22 this year, Solid Edge celebrated its 22nd birthday and ST10 is the 30th release of Solid Edge, a pretty impressive milestone for a CAD program which originated when most of us were still in high school or had just embarked on a professional career.
Solid Edge was first released by Intergraph which has its roots in a company called M&S Computing that was started in 1969 by a group of engineers who were working for IBM in Huntsville, Alabama developing guidance software for the Saturn rocket. The group consisted of Jim Meadlock and Terry Schansman who are the M and the S in the company name besides others. It was only in 1980 that the name was changed to Intergraph, short for Interactive graphics. This is perhaps also the reason why Solid Edge’s global headquarters today continues to be in Huntsville, AL the home of Intergraph even after being acquired by Siemens AG in 2007.
Before Solid Edge arrived on the scene, Unix was the dominant operating system for CAD with dedicated workstations built around them bundled together as what was then called Turnkey Graphics Systems. Not only were they accessible only to a select few engineers, various components of the CAD systems were not designed and hence not capable of exchanging data with each other without the involvement of a third party neutral format like IGES, STEP or DXF.
This changed on May 9th, 1995 when Intergraph released its path-breaking technology code-named Jupiter which was a Windows-based, object-oriented software development framework. Applications based on the Jupiter technology were software components that seamlessly worked with each other and were compliant with Microsoft’s OLE, short for Object Linking and Embedding. OLE had already taken the software industry by storm with its Copy-Paste or Drag and Drop facilities that allowed features like, say a graph created in Excel, to be inserted into Word or PowerPoint and vice versa.
The distinguishing feature of OLE was when data in the source file changed, the OLE linked objects updated automatically. This suited well for Solid Edge which allowed creation of assemblies as a placeholder for its component which referenced the Part files. The Jupiter Technology extended OLE for design and modeling which came to be known as OLE for D&M. As a result, Solid Edge could offer Part, Assembly, and Draft environment, all in the very first release when contemporary CAD programs were prominently recognized as 2D only for e.g.AutoCAD or Pro Engineer for 3D. A specially designed 3D clipboard format for Windows based on Spatial’s ACIS SAT file format powered the capability for Copy-Paste.
Further, unlike other 3D CAD programs, Solid Edge from the beginning was oriented towards the design of assemblies, a refreshing change from the single-part oriented CAD systems of that time.
So the following remarks by Kaiser Optical System, an early adopter of Solid Edge speaks volumes about the excitement due to the benefits derived by migrating to Solid Edge from their older 2D and 3D systems:
“An important feature is Solid Edge’s assembly modeling capability, which uses linking rather than layering to incorporate components that already exist by telling the system where to find them. Now, when a component is updated, each assembly that links it automatically incorporates the updated version. We also get a robust associativity between models and drawings generated from them. These things have really made a difference.”
The architects of Solid Edge maintained that most problems in design are interference problems. So when assembly is an afterthought, you don’t find those problems until the design is complete. Also adopting an assembly focus from the start means you won’t create the interference problems in the first place. Over the past 22 years Solid Edge has consistently proved this with its prodigious interference checker in the assembly environment.
Fig: The Interference Options dialog from an early version of Solid Edge, not much different from the current one.
As mentioned earlier, CAD and the hardware they worked on were often bundled together as Turnkey Graphics Systems and Intergraph was no exception. But by shifting its focus to become more Windows-centric, Solid Edge not only enabled companies to relish the benefits of CAD on the same machines as office automation software, the computers didn’t become obsolete every time there was an hardware upgrade. They now could just move a designer’s machine to a secretary’s desk. This may seem a trivial matter today but was perceived as a major advantage couple of decades ago.
The Jupiter project provided a platform that could be used to create a number of graphics applications, including 2D CAD, AEC, mapping, P&ID. Another application built using the Jupiter technology was Imagineer Technical, a 2D sketching program that bridged the gap between a basic paint brush style tool and a full-fledged drafting program. It allowed creating parametric 2D objects and further modifying them by pulling handles or by changing dimension or using commands like trim, extend fillet. Other prominent features included creation of multiple sheets and DWG import.
Fig: Imagineer Technical with a sheet tab and an automatic sheet border
Other software based on the Jupiter technology released around the same time was SmartPlant 3D for plant modeling, GeoMedia for GIS, InRoads for 3D road design and SiteWorks for terrain modeling. These along with Imagineer Technical had a striking resemblance with the early versions of Solid Edge since they were all based on a common theme and philosophy and most importantly a common architectural framework.
Fig: Plant Modeling Software – SmartPlant 3D, based on Jupiter Technology
Fig: Solid Edge V3 Draft and Part environments.
So impressed was Microsoft with these developments that CEO, Bill Gates remarked “Intergraph has really captured Microsoft’s vision of the future by creating native Windows CAD applications, and we applaud their achievements. Intergraph’s early commitment has helped make this phenomenon possible”. This also lead to inclusion of Imagineer Technical in a release of Windows that year, something similar to the bundling of Visio Technical a decade later.
In the initial years, Solid Edge also imitated Microsoft Office products to the extent that there was even a Tip of The Day dialog that popped up at startup, though you could turn it off from the Options. But these features were considered cool in the late 90s.
Solid Edge Version 1
Before being announced on Oct. 17, 1995 and subsequently released on April 22, 1996, Solid Edge internally was simply called MD or Mechanical Design. The user interface was Windows compatible so it greatly reducing learning time and which also was its USP or unique selling point. Use of OLE enabled users to insert MicroStation and AutoCAD parts in Solid Edge assemblies besides those created in its own Part environment.
This version had all the basic ingredients of a 3D CAD program like Extrude which was then called Protrusion, Cut, Revolve and Revolved Cut, Expressions now called Variables, Fillet, Chamfer, Rib, Thin Wall and Pattern to name a few.
The dominant CAD programs of those days won’t let users exit the sketcher unless the profile was fully defined or constrained and here you had a brand-new Windows based CAD program which was not only faster to learn and easy to use, it even allowed modeling parts with open profiles once you had a base feature in place. To fully realize what open profile can do for feature creation, read an in-depth tutorial which shows how to model a simple nut that never fails to rebuild. As a quick illustration of the use of an open profile for feature creation, note the extrusion in image below. Doesn’t it look easy, powerful and compelling?
Fig: Open profiles was an industry first introduced in Solid Edge
Sketching tools automatically recognized constraints such as parallel and perpendicular lines and if you start thinking about these things, today we take them for granted but if you step back in that time frame, it was unique and different.
In the assembly environment relationships like Mate, Planar Align and Angle were known to be available.
Version 2
Released in October 1996 Solid Edge V2 used ACIS 2.0 and focused on two aspects of the design process – individual part design and the management of large assemblies
Version 2 of Solid Edge further improved assembly design with new ‘top-down’ design aids, including in-place modeling of assembly components. Designers could create new part models within the assembly, assuring accurate fit and function by directly associating part dimensions and design relationships to the faces and edges of other assembly components. This early technique was further reinforced with InterPart Copy in V8 and the more recent Peer command.
Solid Edge V2 could also create parts starting with disjointed components and then fill in the gaps between these components.
Announced by William H. McClure, VP of Intergraph Mechanical Software Solutions, who had a year earlier also given first public demo of Solid Edge, this version saw some improvements in rounding and creating thin-wall operations largely due to the developments in the underlying ACIS Kernel.
Besides this, V2 also supported Intellimouse, Microsoft’s newly introduced innovative pointing device.
Once installed, the Start Menu had different icons to start the Part, Draft and Assembly environments separately.
Fig: Solid Edge Program folder
and each icon launched Solid Edge in the respective environments with its specific splash screen as seen here from Solid Edge V1:
Version 3
Released in March 1997, Solid Edge V3 also continued with ACIS 2.0 and the minimum system requirements were a 486 Intel processor-based computer with a chucklesome 32 MB RAM, a CD-ROM, 100 Mbytes of disk space running either Windows 95, NT 3.51 or NT 4.0
The requirement for a CD-ROM is especially noteworthy since it was common in those days to distribute software on a bunch of floppy disks. The installation process would pause and prompt to insert the next disk while a message would wait on the screen asking to ‘Press any key to continue…’
Users reportedly dialled 205-730-EDGE asking for help locating the ‘any’ key on the keyboard.
Well, that was only a popular humour few decades back ?
If the setup had a GUI i.e. graphical user interface, then they were expected to click the Next > button after inserting the next floppy disk in its drive. For those who don’t know what a floppy disk is, just look up the Save icon in your current version of Solid Edge ?
The following features were known to be present, though they possibly existed in much earlier releases as well:
A SmartStep ribbon bar, now called the Command bar.
PathFinders
Feature Playback
Feature Reordering
Failed feature indicator in Pathfinder
QuickPick – note the horizontal layout and perhaps the name of the current element appeared as a tooltip.
Fig: Retro QuickPick with a horizontal layout
A more comprehensive list of features added in V3 were:
- Replace Part command in Assembly and relationships were maintained during the substitution right from the beginning which is remarkable.
- Parts placed in an assembly can now be underconstrained.
- Connect Relationship in Assembly.
- Assembly Reports.
- Swept and Lofted Protrusion and Cutout features in Part.
- Ability to mirror copy a feature in Part and it was associative as well.
- Ability to save a part as a mirror copy in Part.
- SaveAs CGM was added to Part, Assembly and Draft since this was the most popular format for viewing graphic files over the internet in those days supported by both IE and Netscape Navigator.
- Ability to mark elements as construction in sketcher.
- Ability to copy and paste profiles was added to the sketcher so users could cut/copy profiles and paste back into the profile environment of either another feature or another instance of Solid Edge. This for the first time allowed copying from profile-to-profile, profile-to-Draft, profile-to-layout.
- Thread Depiction from Hole Feature added to Draft.
- Dimension to intersection of two curves added to Draft.
- Ability to define and use layers added to Draft.
- Value Field Support for Math Operators was added to Part supporting math operators. Users could then start sing (1.5+3)/5 in the value fields when specifying dimensions, etc.
- Several 2D drawing tools that were exclusively found in the sketcher were now made available in the Draft environment too. User could create new geometry other than the drawing views on the draft sheet or in the ‘Draw in View’ mode which was also introduced in V3.
- The 2D Model sheet was introduced though not by the same name.
- Also, the ‘Convert to 2D View’ feature was added, it was referred to as Convert to graphics originally.
The most remarkable addition in V3 was the Revision Manager which replaced the Copy Special, Rename Special and Replace commands. The Revision Manager in turn was replaced by the design Manager later in ST9.
Version 3.5
This was a special release in June 1997. Solid Edge Version 3.5 used ACIS 2.1 and introduced the modeling of sheet-metal parts consisting of features like tab, flange, contour flange, and break corner tools and Flat pattern.
Rendering capabilities were integrated which included prominent features like colored lights, anti-alias options, reflections, textures, background images, and shadows.
Also among the new capabilities were suppressing Part features, renaming features and IGES Import.
Version 4
With more than 150 enhancements, V4 was one of Solid Edge’s biggest releases in November 1997 and also the last one to use the ACIS Kernel. The scope of new features was significant and though unconfirmed perhaps included:
- GoTo for features in the Edge Bar.
- Save As Image.
- A standalone viewer.
- Patterning of parts in assembly.
- Exploded view environment in the assembly.
- Variable radius fillet.
- Bend outside added as a third option in sheetmetal.
- Temporary unbending allowed during bending in sheetmetal.
It was also rumoured that the Helix feature was programmed by the Solid Edge developers themselves in the absence of a feature in the ACIS kernel.
Fig: The Helix Parameters dialog from one of the early versions of Solid Edge
There were also several other limitations with the fillet and thin wall features of ACIS leading to a decision to change the kernel to Parasolid for the next version of Solid Edge i.e. V5 but a ACIS to Parasolid converter was delivered with V4
Meanwhile, here’s the classic Solid Edge cube logo of the early versions and the text before switching to the present Rockwell font. The old font that closely resembled is Haettenschweiler but with slightly narrower inner loops for the letters o,d,g, e and a much slimmer font stroke.
Here’s a much earlier design from around V2 or V3:
Version 5
Released in June 1998 Solid Edge Version 5 was now powered by the Parasolid 9.1 modeling kernel and could run on both Windows 95 and NT. The new release included more than 100 new design capabilities, usability enhancements and performance features. Chief among the improvements were improved rounding, thin-walling, blending, and hidden line removal for drafting. New large-assembly management tools let users define and manipulate select sets with improved performance through unloading non-displayed selections.
Care was taken to have the new version fully compatible with Solid Edge Version 4 data. Version 5 allowed for automatic and batch directory conversion of legacy data files while maintaining associativity, parameters, and a complete feature tree. With version 5 Solid Edge was now also interoperable with Unigraphics which too was powered by the Parasolid kernel.
STREAM technology was introduced in V5 which boosted user’s productivity by capturing solid modeling design intentions through inference logic. This technology was built on the fact that designers spend relatively little time waiting for their computers to process but they spend a great deal of time providing input. With this goal in mind Solid Edge V5 optimized the speed and effectiveness with which it gathered information from the user using predictive input.Logical inference engines within Solid Edge constantly monitored user input via the cursor position, the mouse movement and the task at hand. The goal was to reduce the amount of input the user communicates to convey design intent. With Stream technology, the user could infer quick decisions dynamically which speeded up the design process.
For example, Solid Edge provided the capability of inferring closed volumes variationally with open profiles so user did not have to spend extra time and efforts to close the profile by projecting nearby edges. Intent zones inferred users’ intentions to place tangent and perpendicular relationships, IntelliSketch was extended to capture nine different types of geometric relationships inferred solely by the way users positioned the cursor while the Smart Dimension inferred appropriate dimension formats and orientations from the geometry being dimensioned.
Today we find all these features and commands scattered all over in Solid Edge but they all had a well thought out and researched plan and methodology.
Marvel at these images of the retro GUI of Solid Edge V5. This look and feel and the general arrangement of the UI continued for a long time until release of Windows XP when the icons suddenly started looking super cool.
Fig: Solid Edge V5 Part Environment
Fig: Solid Edge V5 Draft Environment
Fig: Solid Edge V5 Assembly Environment
Fig: Solid Edge V5 Sheetmetal Environment
The kernel change story is equally interesting. Intergraph approached EDS’ Unigraphics Division about using Parasolid as the geometric kernel for Solid Edge in place of Spatial’s ACIS. But the discussions led to a decision to create a new company that would be jointly owned by EDS and Intergraph. Eventually in October 1997, EDS and Intergraph announced that they planned to form a new company consisting of Intergraph’s mechanical business unit, Unigraphics and a small amount of EDS’ consulting activity. EDS would own the majority interest in this unnamed company while Intergraph and the company’s employees would own minority interests. Altogether, the company would have a little over 2,000 employees, 350 from Intergraph and 1,700 from EDS Unigraphics.
In subsequent months the planned deal with Intergraph changed significantly. Instead of establishing a jointly owned new company, EDS restructured EDS Unigraphics in early January 1998 as a separate enterprise called Unigraphics Solutions. This entity then purchased Intergraph’s mechanical systems business unit, which included Solid Edge.
Further in January 2001 the company name was shortened to UGS while Solid Edge kept flourishing and being further developed until UGS was eventually acquired by the Automation & Drives Division of Siemens AG and renamed Siemens PLM Software on October 1, 2007.
Read some very interesting internal stuff from the people who were involved in this transition
Here’s an infographic that summarizes the history of Solid Edge from V1 to V5
Tushar is a Solid Edge blogger and programmer for 23 yrs and manages his single-person consultancy by the name CADVertex Solutions that offers custom solution development using the Solid Edge API.
Do you want to automate any repetitive Solid Edge tasks at work?
Tushar creates good quality apps at affordable rates.
Write to him at Tushar.Suradkar@Gmail.com
Read further journey of Solid Edge from V6 to V10 in next part…
Comments