Sustainability in Practice with Solid Edge
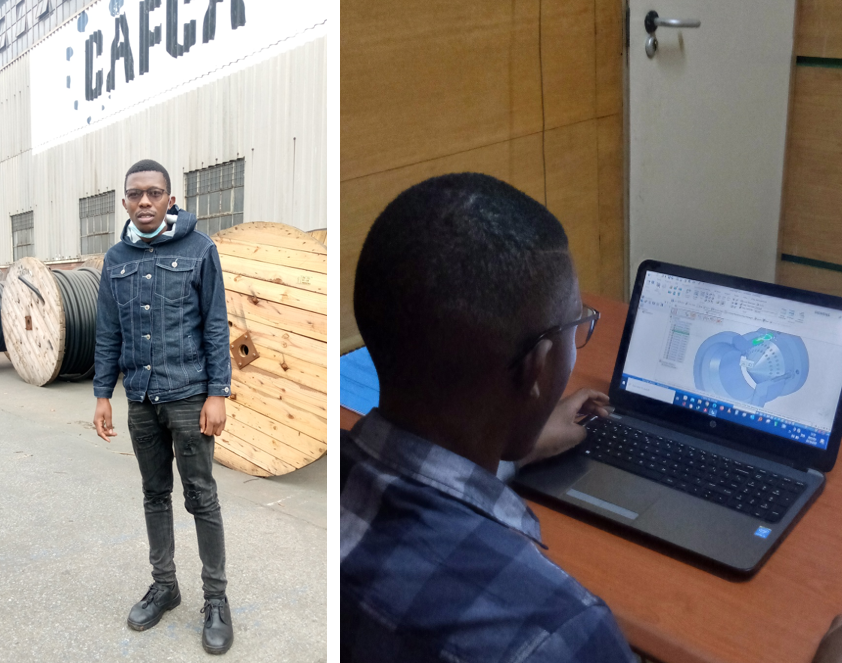
Wisdom James Murombo has been using Solid Edge throughout his engineering studies at the National University of Science and Technology (NUST) in Bulawayo, Zimbabwe and to support his internships at local manufacturing companies. We previously blogged about Wisdom’s use of Solid Edge for generative design.
As part of his internship at CAFCA, a manufacturer of electrical cables in Harare, Wisdom designed components needed for manufacturing plastic hosepipes. According to Wisdom, “We saw an opportunity to recycle PVC chips that are a byproduct of the process used to add protective plastic covers to electrical cables. We looked for a suitable product to manufacture and decided on a flexible garden hose.” Working with Steven Mabika, CAFCA’s recycling champion and plastics specialist, Wisdom designed a new die that could be installed on an existing extrusion machine.

Key design considerations
An important consideration for this project was to design a longer inner die channel to reduce swelling of the polymer as it exited the die face. Swelling occurs due to the “memory” effect of the polymer melt. Splines were also added to the die to create ribs along the axis of the hose that aid the grip of the end-user. Engineering drawings were created to communicate the design to the CAFCA die shop.

After manufacturing a sample batch of hoses, a survey of end-users was conducted that confirmed the effective operation of the hose. One user reported issues on the ovality and occasional collapse of the hose. These issues are being investigated. A cost benefit analysis was conducted that showed manufacturing the hose using recycled PVC chips resulted in a significant cost savings compared with using virgin plastic materials.
Improving sustainability by using waste materials
The second project also involves the recycling of waste PVC material. In this case a process was designed to create standard size PVC pellets that could be used by existing extrusion machines. This project had these key requirements:
- Create a die design with multiple holes for high volume chip creation.
- Ensure pellets are created separately and to the right size.
- Design a containment system for the cut pellets.
- Design a cyclone to facilitate drying and collection of the pellets into a collection bag.
- Contribute to sustainability of electrical cable manufacturing at CAFCA

A layout of the overall design is shown above. Molten polymer material is extruded through the holes of the die face and cut by rotating blades powered by a motor. Wisdom designed the die using Solid Edge. The die has 59 holes to create a high volume of pellets to the correct size. Solid Edge Simulation was used to conduct an FEA analysis of the polymer melt pressure onto the die and to ensure that the attachment bolts were correctly specified.

Solid Edge: A key resource for college design projects
Wisdom says, “Having access to Solid Edge has helped me considerably in executing these projects. Not just for designing the components, but also for creating the 2D drawings for manufacturing. I could also perform stress analysis to validate the strength of critical components.”
According to Steven Mabika, “Wisdom’s design skills gave us a huge stride in completing these two projects. He was able to produce the 3D models and working drawings very quickly. This made it easy to communicate with and make informed decisions when working with other team members in the workshop.”
Siemens strives to be a world leader in sustainability and is excited to have students like Wisdom using Siemens software solutions to solve real-world design challenges. In this case, using Solid Edge to design systems that use recycled materials and that decrease the consumption of oil-based plastics. Solid Edge Student Edition is available to students globally, and we encourage you to download it and try it out. We are interested to hear more stories from students who are designing sustainable solutions using Solid Edge; you can contact me here.