The Never Do List of Solid Edge Modeling and Drafting Practices
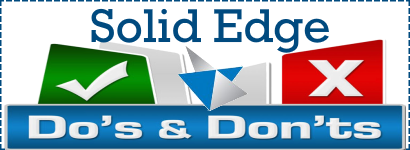
There is no dearth of best practices out there when using Solid Edge. Some of these are implemented as part of the company standards, while others come through self-discipline.
Another category of best practices is the one learned the hard way by making mistakes and learning from them. We make up our own bad habits unknowingly, sometimes to beat deadlines or due to sheer laziness.
This article delves into the absolutely ‘never do’ list or Solid Edge practices. There is a fine line between good practice and a bad one. Whereas downloading and installing the latest maintenance pack from GTAC is a good practice to keep your version of Solid Edge up to date, saving a file from an earlier release into the current version and sending it back to the one who created it originally, even accidentally, though not necessarily a bad practice, is something you should be cautious about.
So what really is a bad practice? It would be something you do today which snowballs into a huge mess or a hairball later. An example would be creating features directly on a solid face. This is a recipe for disaster which you will eventually get a taste of downstream. I like to create planes on Solid faces especially when I create new sketches and adding holes to a part. If I add on a solid face, the hole position will be lost when the face is gone as part of some feature edit and get an exclamation mark or gray arrow in the PathFinder but if I attach the hole to the plane, the surface can change as long as it planar and in the worst case I can isolate the plane and reattach to something else.
Similarly, dimensioning to edges created by rounds or chamfers is a big no-no.
Another case would be to never duplicate geometry within a sketch. Keep sketches simple, and only define a single profile. Use patterns to duplicate the profile’s feature.
Further, if you haven’t yet made the big leap to Synchronous, never slap direct editing features when an edit to an earlier feature can fix it. It is the year 2018 and Synchronous has over the past 10 years has developed into a robust and feature-rich environment for editing geometry directly while still relishing the benefits of parametric. So using synchronous modeling is the way forward.
Or for that matter, never define the color of elements which are same/close to Solid Edge’s default highlight color for selected objects.
And this is not restricted to the end user or designer. Managers should never purchase Solid Edge, then expect to implement it and get full functionality without training, I mean ‘professional’ training.
Then there are folks around who never do nothing but complain about Solid Edge. Pet peeves are acceptable though. And sure it’s fun to poke at Solid Edge and have a good laugh, the reality is, Solid Edge keeps getting better all the time.
This is all fun, but I am not in the Solid Edge haters club. So my advise would be to never skip going to a local Solid Edge user group meet or if your means allow, attend a Solid Edge University near you.
Early in the learning path; especially users migrating from other CAD programs, it is very easy to whine about ‘why this works like this’ when there actually is very constant logic on functionality, you just need to learn few basic things.
Then there lies the inability to see the big picture. It is not always generally understood that Solid Edge is, in fact, one of the most complex computer programs in the world. From complexity and from versatility come great benefits like CAD modeling AND NC programming AND FEA analysis in same infra, but from that complexity come of course certain restrictions to flexibility. Compared to the complexity of bug fixing on such a huge software, I think that Siemens PLM is doing an excellent job.
If you are a CAD administrator, it goes without saying never release a service pack, to the population, before a major test regiment and also never load a service pack just before a major deadline. Not that maintenance packs are bad, it is imperative that you read the comprehensive list of problems that are addressed with each MP in the release notes that accompany it.
Furthermore, never stay away from the Community forum for too long. Who knows browsing through that 9-page, 5-year old thread and the 20 minutes it took could save you several more weeks in frustration. Agree yet?
And if you indeed are a frequent visitor, never forget to first read the documentation followed by searching the forum when everything else fails. Before heading to the community forum never haste, but ponder for a while and never ASSume it’s a bug. One occurrence may not necessarily indicate a problem with a Solid Edge feature. If you cannot duplicate it, it could be pilot error.
As usual, this is an open discussion, so whether you are a seasoned Solid Edge user or a newbie, you know you have had your fair share of bad experiences which now are a part of an un-documented never do list. So chime in with some of your suggestions about things you should never do in Solid Edge when either modeling or drafting, which you might have seen others doing or those you have given up for yourself.
Comments