What’s New in ST10: Generative Design
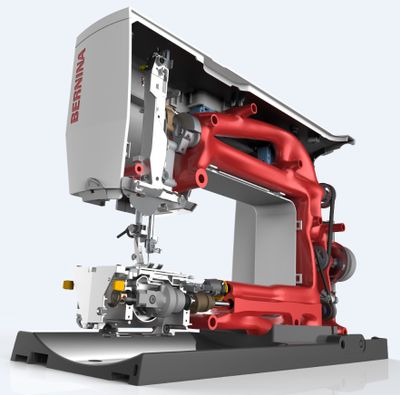
Imagine inputting the requirements for connections to other parts, loads, materials, and whatnot into your computer, and having it spit out the part already designed and load optimized for you. That’s essentially what Generative Design is. It does a stress analysis based on your input, and returns only the areas of the part that are supporting the load.
The official image for this function is the sewing machine frame, which I’m sure you’ve all seen a hundred times by now, and I thought I’d come up with something on my own.
In this part, the transparent blue body is the block I started with. I knew that the result was going to be inside this volume, and I just wanted the software to sculpt away the unnecessary material in the block.
The red areas are defining material that I know needs to be preserved, in this case material around the holes to support the connections.
The opaque body inside the transparent body is the result that Solid Edge Generative Design came up with as my mass optimized finished model. Realize that this is based on loads and constraints that aren’t shown here.
“You know how much it’s gonna cost to machine that part???” you say. Well, part of what this process is meant to help you with is to help visualize what is actually needed for strength, and you still have to make the necessary decisions to make it manufacturable.
If you are looking to cast or 3D print this part, you can work directly from the data that Generative Modeling provides, which, if you have been paying attention to this blog for the past couple of weeks, you might know is a mesh.
As a reminder, Convergent Modeling is the umbrella which brings together Generative Design, Reverse Engineering, and the ability to work with mesh data.
Generative Modeling brings a new tab into the Solid Edge interface, with a new set of tools that help you establish a workflow.
The Generative Design panel helps you keep track of what’s going on, much like the Pathfinder for model features or the panels for Simulation or Sensors. You can create multiple Generative studies to try out different inputs.
The primary point of this is to be able to visualize where the material is needed, so that you can build around it for manufacturing purposes, but a secondary point is for the generated shape to be used directly. Because it’s a mesh, you can 3D print the shape as it is.
There are companies already using this technology to save weight or material on extremely large castings, where even saving a few kilograms adds up quickly in material and manufacturing costs.
Because this is a process much like FEA, there are some things to watch out for. My first attempt at creating something ended in a study that was too complex, and didn’t finish running within the time I had allotted to writing the article. Remember in the background, the computer is creating an FEA type mesh, applying the boundary conditions, and solving the model. But on top of that, it also must remove all of the low stress elements.
When you set up the study, you can specify the study quality, which is probably controlling the size of the mesh elements. You can also specify how much you want to reduce the mass of the input body. (I would have expected this to produce a hollow result, but in the cases I have worked with, it hasn’t – perhaps I didn’t set it to reduce the mass enough.)
The technology has been around for some time, but what is being used by Solid Edge for the Generative Design tool is state of the art, and gives a smoother, more realistic, almost organic type of result. I’m a firm believer that in the future, product shapes are going to become more complex. Even machine design (dare I say “especially” machine design?) will take on this type design paradigm because of its need for efficiency. The factor that keeps todays parts so prismatic is the limitation of manufacturing techniques, but ST10 is taking a broad view on the future of design and manufacturing with the belief that additive manufacturing will continue to push into the mainstream. Just the fact that additive processes not that many years ago used to go by the name “rapid prototyping” says something about the progress made in those areas moving toward manufacturing with the material properties and in the volumes required for real world application. We are not there, yet, but with ST10, the pace quickens.