What’s new in Teamcenter Product Cost Management?
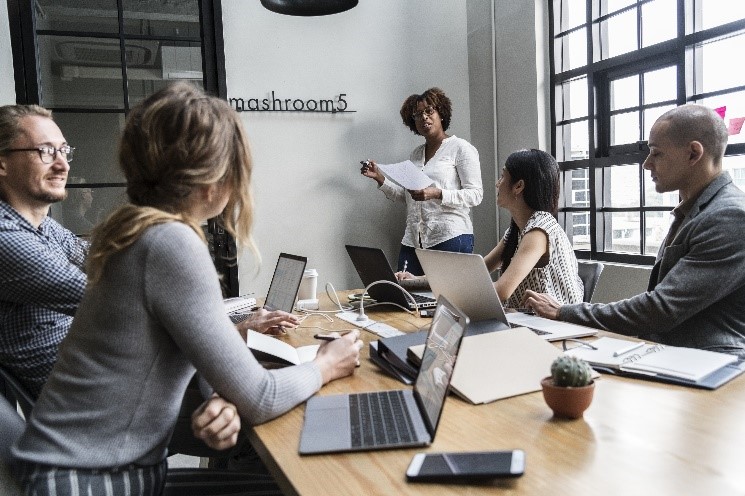
The new version 8.3 of the Teamcenter Product Cost Management solution has one major target – to move your business forward. The cost pressure for companies is increasing across all industries. If you want to continue selling your products successfully and profitably, you need a precise method for calculating accurate product costs. Teamcenter Product Cost Management supports you in influencing your product costs where they occur – in the development phase and optimizing these over the entire product lifecycle. We continuously work to improve our solution, thus with the new version you can benefit from the enhancements for product and tool cost calculation.
More accurate cost calculations by introducing new capabilities to better support the change over time for material costs
Companies that manufacture products that containing a high amount of electronics components, (e.g. automotive suppliers in the area of lighting and multimedia systems) face the challenge of relatively high inflation on purchase prices. Same applies for companies that manufacture products that include very expensive components which represents a large portion of the total material cost (e.g. catalyzer within exhaust system). Which leads to the consequence being that it is difficult to accurately predict and control product costs and profitability calculation – especially in the quotation process. With the new enhancements in Teamcenter Product Cost Management, we support you to overcome this challenge by providing transparency on the change over time of the material cost. In most cases it is not enough to increase the material costs in total, since material groups have different fluctuations and must be treated separately to calculate accurate product key performance indicators (KPIs) for decision making.
The following use cases are supported:
-
- Increase material groups of commodities or classification using increase rates, support of use cases such as: simulate change over time of copper, electronic components, etc.
-
- Manage the negotiated material prices directly in the respective project within Teamcenter Product Cost Management: this provides higher transparency in the project by introducing a single central repository for managing project-specific material prices. You can also increase automation by using master data for negotiated future contract prices. Prices can be imported from the purchasing system into Teamcenter Product Cost Management master data.
-
- Precise consideration of individual material prices to achieve more accurate profitability calculations: especially for very expensive or highly fluctuating purchased parts or electronic parts, it is important to consider the forecast prices or contract prices of individual materials when conducting the change over time. This increases the accuracy of product’s profitability KPIs.
With these enhancements, especially companies from automotive industries and high-tech electronics eliminate cost and price risks and gain more profitable business.
Improved visualization of all cost factors used within a calculation
With the improved visualization of all cost factors within Teamcenter Product Cost Management, we provide a central repository where all the cost factors that are used in the calculation can be viewed and updated in a single consolidated list. For instance, Cost Engineers would be able to visualize within the purchase price analysis with little effort and adjust the labor costs that are used in various production steps.
New tool technologies and profiles
As standard, we already offer a range of tool technologies and corresponding profiles. With version 8.3, we include new technologies, (forging tools) and profiles (additional profiles for injection molding, multiple component injection molding, foaming). Pre-configured tool technologies and profiles enable faster time-to-value.
Extended calculation of workplace costs for tool costing
The “reference tool shops” area in Teamcenter Tool Costing enable the modeling of a complete tool shop including machine and labor costs. Also, it is possible to apply a complete overhead structure which leaves the user with a fully burdened rate for all work centers. Particularly for the “reference tool shops”, we now have a structure in place which allows an easy modelling of such a tool shop with all its work centers. Once the tool shop is modeled it can be “published” as a whole into the master data. When you generate a new tool cost calculation, it will simply select the reference tool shop and then will use all the corresponding machines. The time required to create a tool cost calculation is significantly reduced both for a tool manufacturer in the quotation phase and for a tool buyer in the price validation phase.
Always up-to-date reference data
Information on cost factors such as worldwide locations and suppliers are required in order to continuously increase the value proposition of your purchased or self-manufactured components. Within Teamcenter Product Cost Management version 8.3 several new reference data about production site, knowledge domain and machines are available. This data makes reliable make-or-buy, relocation or global sourcing analysis possible and can be used to reduce manufacturing costs.