Discover what’s new in Teamcenter Quality 2406
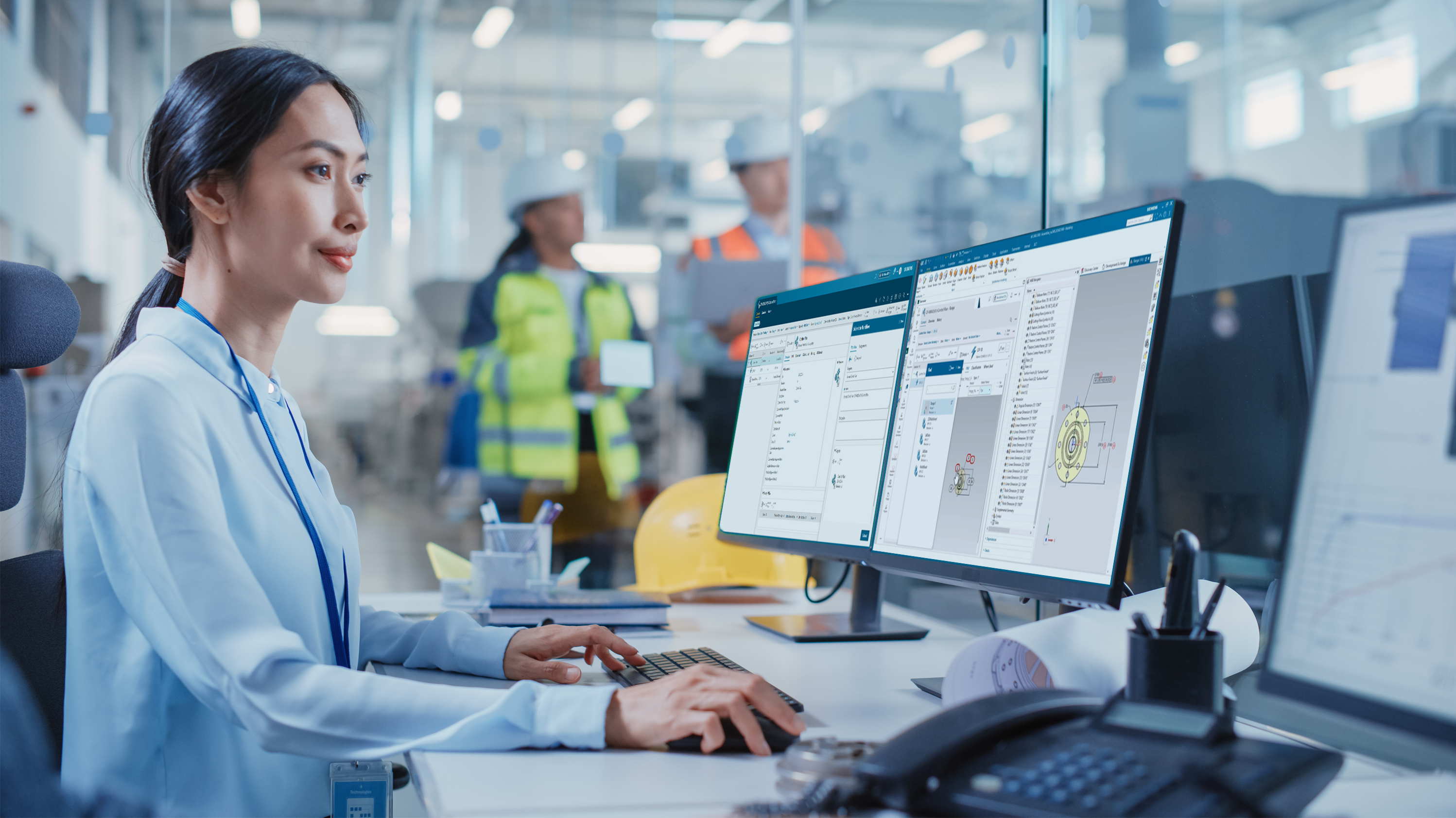
Take your quality management processes to the next level
Are you looking for a solution that supports a closed-loop quality approach from design to manufacturing? Look no further than Teamcenter Quality 2406 software. Built on the reliable Teamcenter product lifecycle management (PLM) backbone, this software enables you to leverage product and process information while sharing cross-departmental workflows, ultimately streamlining core quality management processes. Leveraging Teamcenter Quality, which is part of the Siemens Xcelerator business platform of software, hardware and services, helps you support all quality-relevant processes required in the overall product lifecycle.
The latest Teamcenter Quality 2406 brings a host of enhancements to its quality management system (QMS) modules. Designed to empower businesses with a comprehensive quality management solution, this new release brings a range of enhancements and features that will streamline your quality processes.
Reusing your company know-how with Teamcenter Quality FMEA
Teamcenter Quality 2406 introduces exciting enhancements that aim to streamline FMEA process, saving time and effort. One improvement is the addition of a copy and paste functionality, allowing users to easily duplicate and create new identifications (IDs) within the FMEA hierarchy. This feature enables the replication of various combinations, whether it’s system elements, functions, failures, action groups, or actions. By enabling quick reuse of individual actions or even entire substructures, this feature significantly streamlines the process.
In terms of traceability, audit logs for FMEA objects in Teamcenter Quality now provide complete visibility. Users can track events such as creation, modification, and attachment/detachment, ensuring a comprehensive record of all activities.
Furthermore, Teamcenter Quality FMEA has undergone several usability improvements. These enhancements enhance visibility and optimize the working experience with quality actions. The process of creating actions has been modified for better categorization and organization. Key information is now more visible in the tree view, providing a clearer understanding of component hierarchy and organization.
To align with industry standards, the interface matrix for the design FMEA has been finalized. This update introduces new interface type values, offering a comprehensive view of interfaces and their impact on the FMEA.

Simplifying PPAP with Teamcenter Quality Project Management
In Teamcenter Quality 2406, we have expanded the capabilities of quality checklists, with a specific focus on supporting the supplier production part approval process (PPAP). Users can now add a supplementary, detailed name or description to checklists, providing additional context and information, particularly for PPAP or audit checklists.
To address the issue of users forgetting to define a rule when working with checklists, a new enhancement has been implemented. Checklists can now only be released if a rule is defined. This ensures that this critical step is not overlooked. If a user attempts to release a checklist without a rule, they will receive a prompt indicating the missing rule, prompting them to complete this necessary requirement before proceeding.
To cater to specific industries, such as the aerospace industry, we have introduced a new selection field called the checklist process type. This field is available at both the chapter and question levels, allowing users to customize checklists to meet industry-specific requirements, such as PPAP in aerospace. This ensures compliance and accuracy in quality management processes.
In the Teamcenter Quality Project Management module, a new calendar view has been added. This view enables users to see all programs and projects with a targeted end date. This provides a convenient overview of their responsibilities and deadlines.
Enhance planning inspections with Teamcenter Quality 2406
Using Teamcenter Quality Control and Inspection Planning offers process- and design-oriented inspection planning capabilities combined with control plan management to prevent rework and reduce costs while improving customer satisfaction.
In this version of Teamcenter Quality 2406, we boosted the integration of NX™ software, which is part of the Siemens Xcelerator business platform, and Teamcenter Quality. In the NX environment hosted by Active Workspace, when selecting an inspection definition imported from an NX 3D model’s PMI into a control plan, the system highlights the corresponding NX 3D model’s PMI and vice versa. With this integration, when a user selects an inspection step within the inspection plan, the system highlights the corresponding PMI in the NX 3D model. Similarly, if a user selects a PMI in the NX 3D model, the system immediately highlights the corresponding inspection step in the inspection plan.

Additional improvements are related to the naming convention, users can define characteristic group naming based on the properties of characteristic and free text, and about the possibility to add new characteristics directly via the panel. Additionally, users now can display unreleased characteristics by unchecking the show released only box. Beyond the enhanced ballooning functionality, other enhancements for better usability are available, such as the possibility of using PMI feature control frames and the possibility to release the entire control plan structure, including linked characteristics, using the release control plan workflow.
Empowered problem-solving tools in Teamcenter Quality 2406
Teamcenter Quality 2406 includes enrichments to enhance the management of quality issues and root cause analysis (RCA). We empowered the RCA with a powerful tool “Is/Is Not analysis” that helps teams solve problems by forcing them to think more deeply about what the real problem is. This tool allows the team to focus on what is or is not in scope. Another improvement pertains to functionalities that impact the quality issues and RCA. With Teamcenter Quality Version 2406, we extended the save as configuration, where the user can reuse or create a new problem- solving process by referring to an existing one.
Now, users can perform complex RCA using the Ishikawa methodology and the 5 Whys methodology. They have the flexibility to add a cause as a sub-cause to a cause in the Ishikawa methodology, and a sub why to a why in the 5 Whys methodology. These enhancements also include the ability to visualize the RCA process in a graphical view, including a new nested view for the 5 Whys methodology.

We also extended the problem-solving report by adding a configurable organization logo, including more RCA details, displaying Is/Is Not analysis details and enabling the creation of report spreadsheets specifically for quality issues. And another new beneficial feature is the ability to automatically assign the proposed due date with predefined business criteria based on the priority of solving the quality issue.
Faster evaluations of auditing and assessment results
Teamcenter Quality 2406 introduces several enhancements to improve auditing procedures and performance. These enhancements in the Teamcenter Quality Audit & Assessment module improve efficiency, analysis, compliance, and visibility in auditing processes.
A newly implemented spider diagram provides a visual overview of audit results, showing the performance of first-level chapters. The diagram uses color coding to indicate favorable, moderate, and less satisfactory results, allowing users to quickly assess the audit outcome and identify areas for improvement.

To comply with ISO 9001 and industry-specific adaptations, the module now supports four statuses for the audit plan workflow: draft, amend, approved, and closed. This ensures effective management of internal and external audits within the company.
To enhance usability and alignment with audit standards, two new list of values (LOV) properties, process and subprocess, have been introduced on the audit overview page to map the house of processes. And improved features for layered process audits (LPA), such as new fields for line and shift have been incorporated, allowing the system to adapt and improve based on user input.
The audit detail summary property has been changed to a rich text field, enabling more extensive documentation with images. These fields provide comprehensive audit information and are accessible in the audit overview report. And users can now view all audits with a planned end date in a convenient calendar view.
Improved quality action management
Teamcenter Quality 2406 offers powerful quality action management capabilities. An important enhancement is the ability to add external users who can seamlessly integrate into reminder and escalation management. The calendar view in the Teamcenter Quality Action Management module provides enhanced visibility and organization of action-related tasks.
Benefits of the unique Teamcenter Quality 2406 capabilities
- Reduce time and effort by leveraging your quality know-how
- Simplify PPAP with specific quality project management capabilities
- Enhance planning quality inspection with ballooning and characteristics
- Empower problem-solving tools for efficient root cause analysis
- Accelerate evaluating auditing and assessment results for making informed decisions
- Close the loop with all relevant stakeholders for better action management
Experience the advantages of the closed-loop quality and start your digital journey with Siemens today!
Interested in learning more about the comprehensive quality core processes offered by Teamcenter Quality? We invite you to explore the Teamcenter Quality 2406 software release notes for a detailed list of enrichments and features.
Explore our Quality Management Software solution components.
Take a deep dive into them by reading these product fact sheets:
- Teamcenter Quality Project Management
- Teamcenter Quality – Failure Mode and Effects Analysis
- Teamcenter Quality – Control and Inspection Planning
- Teamcenter Quality – Problem Solving
- Teamcenter Quality Action Management
- Teamcenter Quality – Audit & Assessment
If you would like to learn about Teamcenter X Quality, as cloud-based quality management software as a service (SaaS), please have a look at our infographic!
Find out more about quality management and compliance on our website!
No matter how you choose to deploy Teamcenter,
you get the same proven solutions designed to help you innovate faster.