Business Intelligence Reporting Tools Help JCB Dig Out Details for Innovation
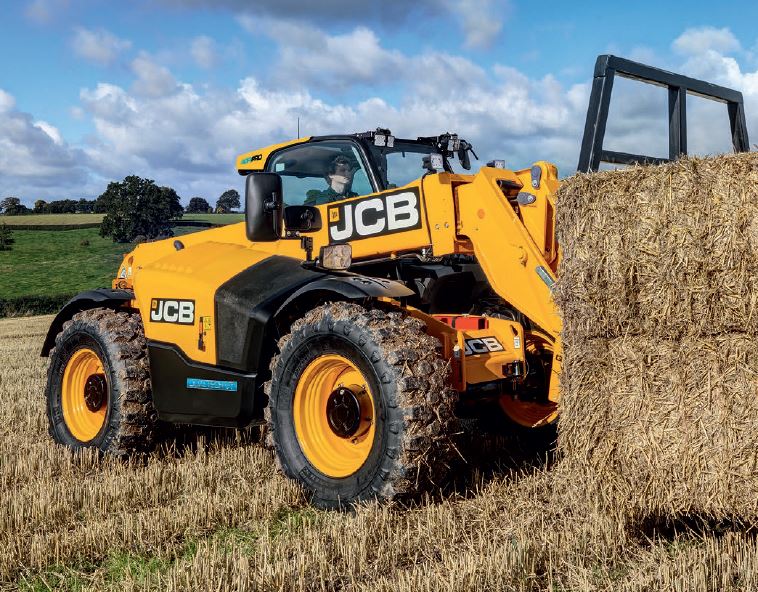

How do business intelligence reporting tools help JCB? Where do Teamcenter, NX and Geolus from Siemens PLM Software fit into JCB’s product development strategy?
JCB has become a household name across the world for its distinctive yellow loaders, excavators and tractors. Within the company’s innovation studio, the focus is on new product development as researchers, designers and ergonomists explore issues such as health and safety, driver comfort, functionality, reliability, fuel efficiency and maintenance costs. The studio iterates with engineering teams who use NX to design parts, and once a concept design is approved, Teamcenter manages the release of all data and generates bills of materials (BOMs). Geolus, the 3D geometry search engine, supports simple language and consistent naming.
“Geolus Shape Search helps us to find parts much more quickly and helps us to redesign and re-use already existing components,” said Andrew Lodge, head of engineering systems.
Developing an efficient product configurator 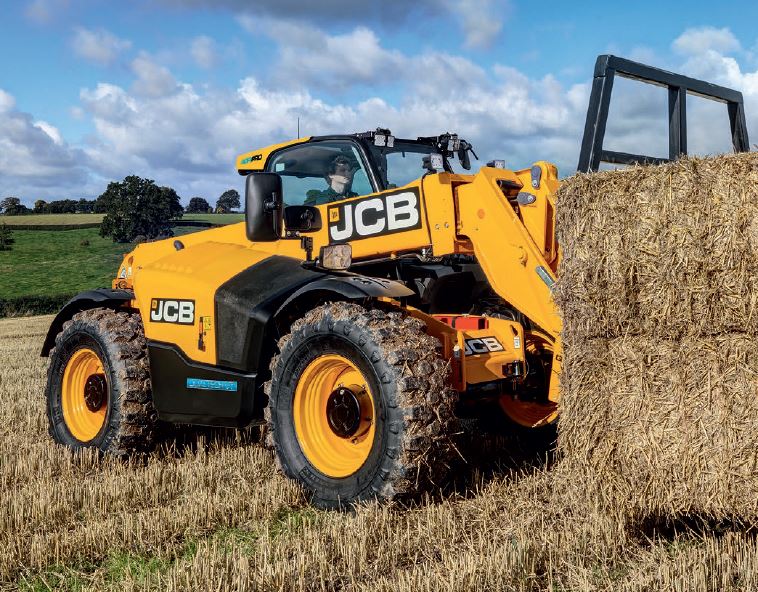
With 200,000 possible product variations, product configuration is a very complex process for JCB. Configuration had historically been accomplished using an array of spreadsheets, which required careful management by one key operator. With this manual method of specifying different parts it was not possible to identify issues that could arise when assembling them all together. There was also no easy means of checking for simple errors such as specifying air conditioning for a cold climate or for an open cabin without any glass. This was the opportunity for JCB to marry its extensive know-how on all product options and variants with the technical expertise of the Siemens PLM Software consultants in order to implement Teamcenter Product Configurator. This brings all the possible product options and variants together in one place, creating the equivalent of a 600 percent BOM per product range or family and enabling the accurate selection of every item needed to configure any variation for a given product order.
“We’ll be able to commonize build across the business units and control our configuration and variants with much greater ease,” said Lodge. “This is going to allow us to check and validate our variations and our build before they hit the shop floor.”
A clear view with business intelligence reporting tools
“We have all the information, and we are working out where it is and how to bring it into Teamcenter,” explains Lodge. “We have a clear roadmap for transferring our extensive, labor-intensive legacy data into Teamcenter, and once everyone is doing the same thing, reporting will become easier and quicker. We’ll learn from each other and we’ll be able to respond more speedily. We will be able to track problems and countermeasures on a global basis, use Geolus to identify parts that need to be investigated, work out common causes and share the results through Teamcenter.”
Watch this JCB case study video for more information, and read the JCB case study for the complete story.