Defining the Part Bill of Materials
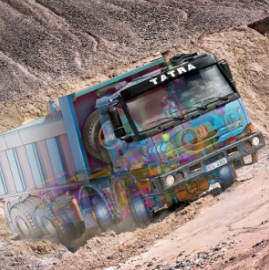
We’ve been exploring bill of materials management from the perspective of configurator on PLM as well as specific discussions about guided production configuration and product variant management. We’ve also had several discussions about an Integrated Product Definition, including an exploration of product master data management and the relevance and importance of managing it within the PLM system. Integral and central to the product definition is the part Bill of Materials that defines the product.
I’ve asked my colleague, Ashok Krishnamurthy, to take a closer look at part BOM management. Let’s expand a bit on some of the considerations that may apply when transitioning to define the part BOM in close association with design data that you may already manage in your PLM system.
Why Part-Design separation?
At a recent conference, speaking with a group of BOM thought leaders from our customers, I was asked – what is a part? And what are the benefits of managing the part distinct from its design?
To discuss this, let’s think about who the primary stakeholders (authors, consumers) of part information are. And who are the authors and consumers of design information?
Of course, the definition of a part centers around uniqueness of form, fit and function.
The part is a business significant entity with a wide constituency of stakeholders within the larger enterprise. The part master needs to record properties that are essential for several enterprise disciplines, including engineering definition, manufacturing planning, costing, service planning, color and appearance planning, procurement, production execution, after sales maintenance, etc.The design information associated with the part records its 3D geometry aspects and engineering significant attributes.
Managing the part as a business entity separate from the design provides relevant stakeholders, within and also outside of engineering, the required independence of lifecycle and associated flexibility to author and access part information and design information and manage their maturation throughout the product lifecycle.
Separation of part and design information has been an established practice at many manufacturing firms. These have usually been managed in separate systems, with the design information being mastered in a PLM system such as Teamcenter within the engineering function and part information being mastered in an ERP or in-house custom application that feeds other production and other departmental applications that rely on the Part BOM.
What are some of the advantages of managing the part in the PLM system?
Engineering departments control formal release of new product definition and product improvements. Design information is central to product innovation and evolution.Mastering all the business characteristics of the product – ie. part information – in close coordination with the product design provides for timely and due consideration of these aspects in synch with the evolution of the core design definition.This can improve the speed of consuming product improvements and changes across the enterprise – importantly in production, after sales and service.
Direct access from the part to its design definition and 3D visuals enables a high definition ‘visual’ BOM. Part and design use in specific product configurations can be qualified using product configuration data that can also be managed within the PLM system. When this type of synchronous evolution of configuration, part, and design information is achieved enabled by a shared change processes and tools under a single system, engineering activities such as design and digital mockup in the context of a physical buildable configuration is possible with greater efficiency and ‘on demand’.
An authoritative single sourced BOM with rich 3D visuals on demand based on product configuration is invaluable to the various consuming disciplines across the enterprise who can not only consume the business properties but also access the exact 3D geometry in an interactive manner.
How to transition to a part – design synchronous release process?
Introducing an Integrated Product Definition into an IT landscape where there is an established Part BOM system with integrations to several external applications can be a multi-phased challenge, but with potentially huge business benefits. Often the question is – how and where do I start on the road to modernization?
A potential first step in this phased approach could be to establish coordinated part and design BOM authoring with common configuration and change tools and processes within the PLM system, while retaining and feeding into the established BOM system in order to continue to leverage existing integrations.
Such a step immediately provides enhanced connectivity between PLM and the enterprise, and a rapid improvement of the information authoring experience, while avoiding the risks associated with having to migrate the integrations with various enterprise applications.
About the Author
Ashok Krishnamurthy is a Teamcenter Product Manager, responsible for Bill of Materials.
Comments