Transforming the Capital Asset Lifecycle – Part 1
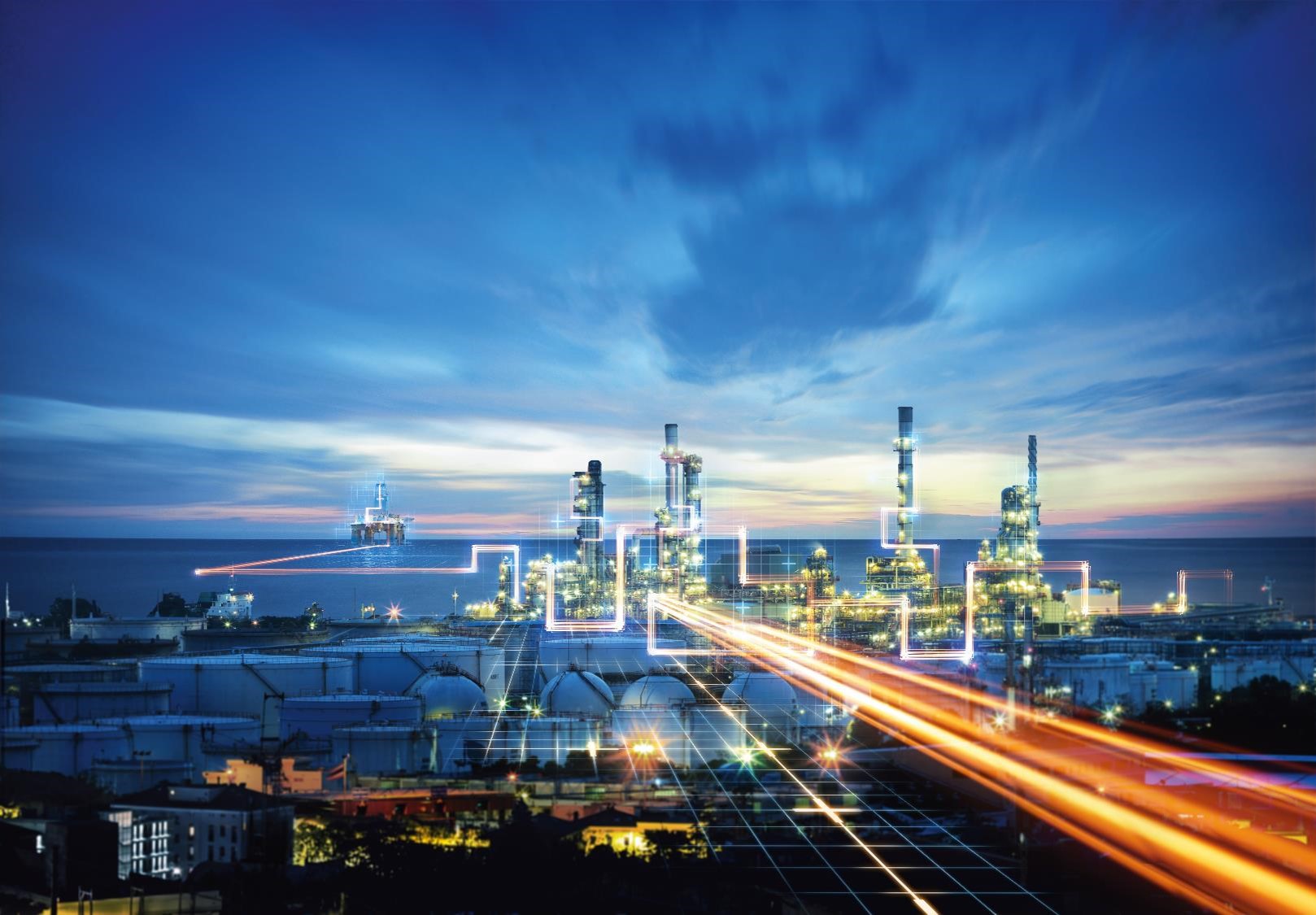
This article, “Transforming the Capital Asset Lifecycle – Part 1″, introduces a new blog series by John Lusty, Siemens Digital Industries Software global marketing lead for Energy & Utilities, focusing on the need for greater efficiencies from today’s capital assets – the plants, facilities, factories, and critical infrastructure that are the foundation of an organization’s operations.
“Innovate or die”. Three years ago, in the global oil & gas industry, this was the dire message communicated from the boardroom to the operating plant as falling commodity prices were hollowing out corporate income statements. The same story echoed through the supply chain as engineering contractors and equipment manufacturers fought for survival – trying to win enough work to remain healthy within a shrinking capital project market while creating greater value from the existing capital asset lifecycle.
The cost-cutting that ensued was ugly, and the job losses were substantial. In parallel, the appetite for innovative ideas sky-rocketed as producers worked to wring out costs and remain profitable at any price. This triggered a new behavior within the traditionally siloed energy industry, for the first-time visionaries started to look to other manufacturing industries for capabilities that could be adapted to their own companies.
What they saw was a shock. Despite years of investing in software and technology, capital asset owners in the energy and process industries still had a long way to go to get full value from their technical information compared to other, more mature, industries. Unlike their business information which, to a greater degree, had been consolidated following two decades of ERP implementations, the technical information supporting their plant assets was still scattered across different locations and incompatible file formats.
To make matters worse, data from multiple projects and facilities used software from a variety of vendors along with their own standards and specifications. Plants that came in through acquisitions and mergers were even more unique.
Owners learned, from other manufacturers, that taking a “lifecycle approach” to consolidating and managing their plant data would be important to improve their process and asset efficiency. The lingering challenge was regarding the lack of interoperability associated with 2D and 3D plant design (“CAD”) information – an industry-wide problem.
The landmark study from the National Institute of Standards and Technology (NIST) entitled “Cost Analysis of Inadequate Interoperability in the U.S. Capital Facilities Industry” demonstrated that in 2004 alone, the problem had cost the industry almost $16 billion, none of which was ever budgeted for. Given the explosion in the volume of data and documentation associated with a capital project, the cost today would likely be much larger.
This was bad news to an industry under extreme cost pressure and, normally, hesitant to deploy new technologies. Certainly, there was an opportunity to lower operating costs and improve the way they worked, but how much risk would be assumed?
Fortunately, the problem of managing the lifecycle of asset and facility information had been solved elsewhere. Companies like Siemens Digital Industries Software had been helping other industries manage the lifecycle of their products, projects, and plants for decades and those solutions had already been technically de-risked. This could allow energy businesses to adopt new capabilities without the challenge of working with brand new technologies. Was the answer to their plant data management problems within their grasp? Perhaps.
Integrating the plant design data remained a challenge, however, and the industry continued to struggle to find the right mix of technology and work processes that would meet the needs of the owner-operator. Siemens had deep experience integrating “Multi-CAD” data from other industries and understood the importance of using open standards to do it. They knew the problem could be solved.
In 2018, Siemens initiated a project that would solve the challenges associated with the capital asset lifecycle so that the energy and process industries could apply what Brian Ferguson, former CEO of Cenovus Energy, called a “manufacturing mindset” to their businesses. Using this leaner approach would enable companies to dramatically improve in areas such as collaboration, change management, process improvement, data re-use and enterprise-wide reporting across technical and business information. By learning from the successes of other highly competitive industries, taking a “lifecycle approach” was coming into focus.
The next article in this series will begin to describe how these challenges can be addressed, so stay tuned for more! Part 2, Part 3, Part 4, and the official Product Release.
About the author:
John Lusty is the global lead for Energy & Utilities Industry Marketing for Siemens Digital Industries Software and is based in Calgary, Canada. John has spent over 25 years working in, or in support of plants and facilities as well as the operators and professionals who are tasked with their ongoing operation. John is particularly interested in technologies and practices that improve the safety, efficiency, and overall sustainability of businesses operating in today’s challenging Energy & Utilities industry.
Comments
Leave a Reply
You must be logged in to post a comment.
Thanks john for the article on Capital Asset Life cycle not detail y but at some point it had explained about transformation in capital asset life cycle.