Link Conflict Minerals and Design for Environment to Organizational Profitability
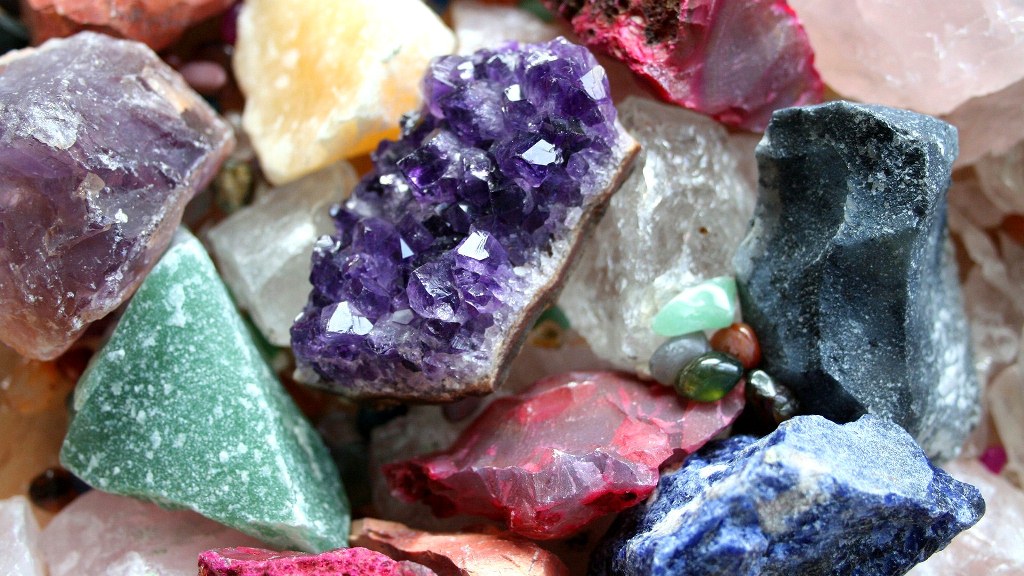
As an industry leader in manufacturing, you can’t go very far these days without hearing about conflict minerals and the regulations governing them. While complying with conflict minerals requirements is important, it is only one aspect of product compliance, design for the environment, and product stewardship.
In this post, we’ll explore how to approach conflict minerals requirements and link compliance with the bigger picture of design for the environment and, ultimately, organizational profitability. Let’s focus on suppliers, as they are both keys to conflict minerals and product compliance in general. We’ll look at the initial steps for engaging suppliers in conflict minerals and materials compliance programs, as well as strategies for meeting conflict minerals rules and improving materials compliance programs.
A Brief History of Conflict Minerals Requirements
In 2010, the sweeping Dodd-Frank Wall Street Reform and Consumer Protection Act included a centerpiece that imposed strict reporting requirements for publicly traded manufacturers that create products containing materials originating in the Democratic Republic of Congo (DRC) and its nine adjacent nations.
The minerals of initial focus are the ores used to produce these metals:
-
- Tin
-
- Tantalum
-
- Tungsten
-
- Gold
The impetus behind these regulations is the notion that mining profits related to these minerals are supporting armed conflicts associated with significant human rights abuses. The rules call for affected manufacturers to provide annual disclosures on whether they use the materials, where they came from, and whether or not they are considered conflict minerals. That’s putting it simplistically, but at this point, if you’re a global manufacturer operating in some of the industries associated with conflict minerals—the most obvious being consumer electronics—you probably have some understanding of what the rules are and what they mean to you.
The requirements were in the offing for a long while, and though some companies took note early on, in many cases it has been an afterthought. It is worth acknowledging that there has been some skepticism over conflict minerals rules and the implications associated with noncompliance.
First of all, the deadline for affected manufacturers to submit Conflict Minerals Reports was effective in June 2014 and has since repeated in 2015. Yet in both years only a small fraction of companies have actually reported, and a very small fraction of reports have been audited. Additionally, few firms submitting reports have specifically named their materials’ sources. There’s also a provision in the regulations that could be considered a bit of a loophole at this point: it allows reporting organizations to report, yet simply say they ‘don’t know’ where materials originated. Also, there is the fact that the regulations as they stand don’t seem to have much bite when it comes to the consequences of noncompliance. This will change as the regulatory requirements evolve, but for the time being some manufacturers wonder why they even ought to comply.
Now is the Time to Act
In addition to the fact that requirements—and consequences of non-compliance—will only become more severe, the buying public at large is becoming increasingly aware of the role of conflict minerals in the production of the materials they use on a day-to-day basis, such as smartphones. Intel, a leader in this space, was among the first to provide a conflict minerals report and with the objective to be ‘conflict-free’ by the end of 2014. It is also notable that other jurisdictions, including the EU and China, have followed suit with the American regulation.
Now is the time to act, as opposed to when penalties are in place, and the market response to adverse events and the costs of noncompliance will be too great to bear. Though it seems like one might get away without reporting, for now, preparing for actual compliance can take a long time. The benefits of proactive compliance and improved product stewardship overall present an opportunity in terms of building efficiencies, improving supply chain collaboration, and boosting profitability.
Those who have yet to either streamline materials compliance or engage in conflict minerals reporting seriously need to start by engaging suppliers. There are a variety of capabilities needed for streamlined conflict minerals reporting program, just as there are a series of requirements for a robust materials compliance program. What we find over time is these sets of requirements align very well.
The Importance of Supplier Material Disclosure
It begins with suppliers. Supplier integration is the cornerstone of an effective reporting program, for, without ongoing, real-time insight into our suppliers and constant communication, we cannot sustain an effective reporting framework. Then there’s the fact we have to manage materials, smelter information, and approved smelter lists, all the while supporting well-known industry standards like IPC-1755 and the Global e-Sustainability Initiative (GeSI).
Part of the problem we see a lot is the fact that though we tend to have a high level of contact and communication with systems integrators, risk partners, and those involved in systems design, often we do not have that level of interaction and integration with those that provide standard parts and suppliers that directly source materials affected by conflict minerals requirements.
What is needed is automated solutions that identify all supplied parts from a bill of material (BOM) and automate the issuance of requests for required declarations to particular suppliers. It’s also important that such requests support industry-specific formats (e.g. CMRT, IPC-1755) in order to automatically import, validate, and process the associated data.
Integrated Material and Substance Management
Beyond conflict minerals, product compliance regulations such as REACH and RoHS require a detailed understanding and documentation of material composition down to the substance level. This requirement has a big impact throughout the product lifecycle, from development to end-of-life.
As a result, a workable framework should consider the following best practice advice:
-
- Culturally Collaborate with Supplier Teams: There’s a messaging component in all this. If you are to effectively collaborate with suppliers, they will need to be on the same page. The value of continued business relationships with affected suppliers should be at the center of your communication on conflict minerals rules.
-
- Define the Process: Conflict minerals aren’t going to go away tomorrow, and the processes you define today will determine how you relate to suppliers in the future. As you implement a system of materials management and collaboration with suppliers to gather material declarations with suppliers, don’t do it with haste. Your approach will need to be scalable and adaptive. As conflict minerals regulations evolve, you will need to have easily adopted processes in place to respond to growing requirements. The technology you implement is important, but will only take you so far. Processes will help make reporting scalable in the long term.
-
- Speedy Rollouts and User Adoption: This is always a factor with any organization seeking to implement any collaboration tool across its supply chain, and for good reason. The suppliers you need to engage will also need to have tools that are easy to use and require a low level of training. This will enable them to engage with the supplier collaboration tools you implement easily, as opposed to being dragged down by cumbersome implementations and awkward user interfaces.
There is a strong potential for the scope of the Conflict Mineral requirements to be expanded over time. For example, cobalt is now receiving attention as a candidate to be added to the list of regulated minerals. This shows why companies should develop flexible processes and procedures to manage risks in their particular supply chain, rather than focus on narrow compliance with the regulations. Effective supplier integration and materials management will go much further in generating a more sustainable business—and building a more sustainable supplier network and materials database—in the long term.
About the blogger:
Matthew Littlefield co-founded LNS Research in 2011 and is now President and Principal Analyst. In this role, Matthew oversees LNS’s coverage of the industrial value chain, including EHS, MOM, APM, and QMS. His personal coverage includes digital transformation and the Industrial Internet of Things. As a recognized industry expert he contributes to the widely read LNS Research blog as well as many other industry publications. Matthew is also a sought-after public speaker and continually advises manufacturing executives on how to best leverage technology in their operations.