Design for Environment (DfE): Supply Chain Interaction for Sustainable and Compliant Product Design
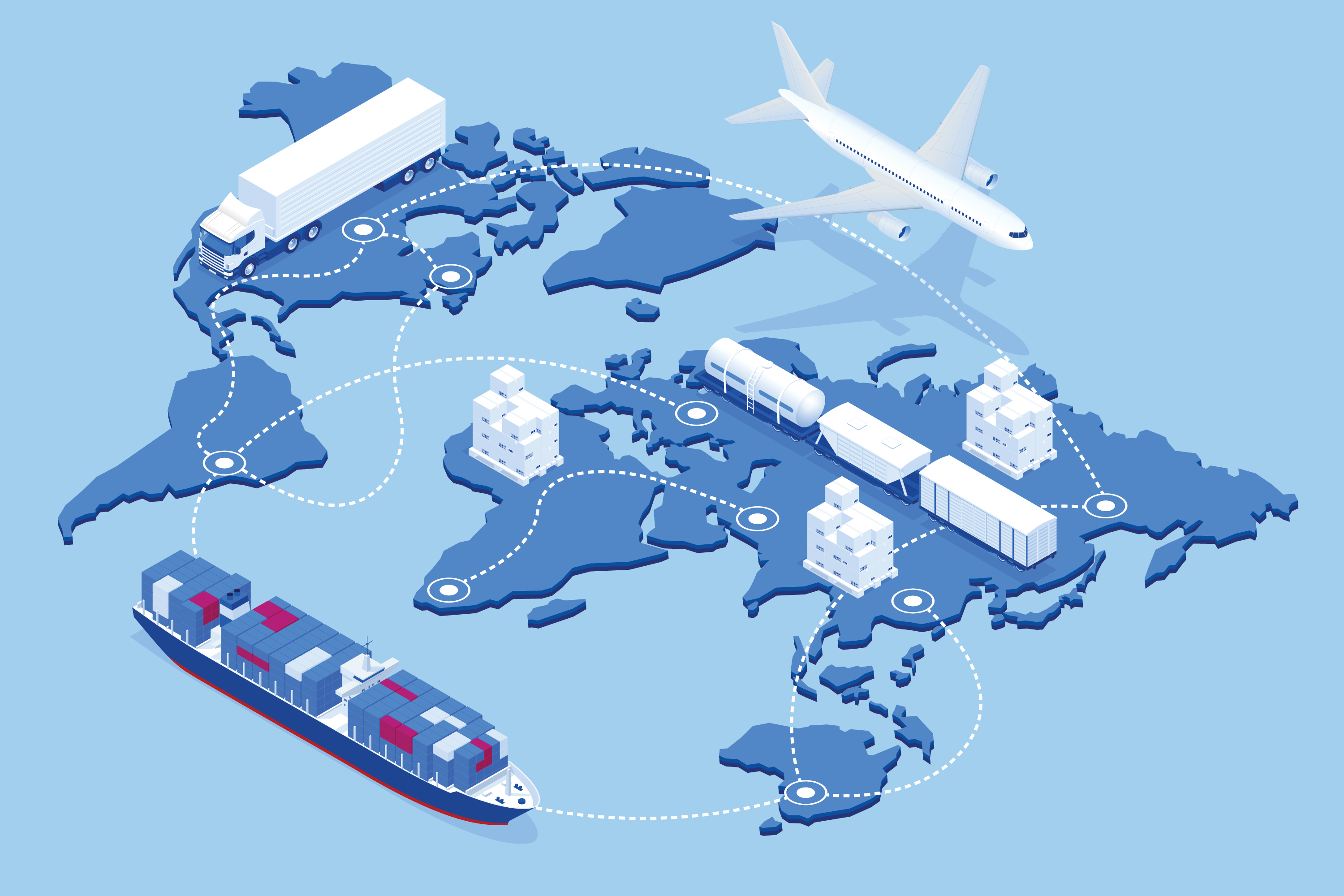
Design for environment (DfE) and product sustainability topics continue to top the charts these days both in the news and on the agendas of leading manufacturers. According to a study performed by McKinsey&Company, CEOs are twice as likely as they were in 2012 to say sustainability is their top priority. They have valid reasons for putting sustainability high on their lists. Company leaders know that if they do not reach their sustainability goals and compliance requirements, they could risk loss of market share or being denied entry into new markets, fines for non-compliance against regulatory directives, and possible damage to their brand.
In a recent Fast Coexist article, “Starting Now, All Intel Microprocessors Are Conflict-Free: Here’s How The Company Did It,” Intel CEO Brian Krzanich talks about the importance of improving supply chain transparency to address corporate social compliance initiatives around conflict minerals. By working to identify the source of supplied materials and what smelters were used, Intel can now claim that every microprocessor that they ship will be made entirely with conflict-free minerals. When I talk to customers about social and regulatory compliance, I am not surprised to find that one of their biggest challenges is getting accurate and complete data from their supply chain.
On average, 80% of manufactured products today are comprised of components sourced from suppliers. This means that if a manufacturer’s goal is to become more transparent and understand how sustainable or compliant their product is, they must have material and substance information on the supplier parts in addition to their internally manufactured parts. This is required before doing any type of analysis around sustainability or regulatory compliance. This is no small task, especially for manufacturers dealing with 100s or even 1000s of suppliers and supplier parts in a deeply tiered supply chain. The increased need to sell products in global markets, where a large portion of the product contains components sourced from around the world, coupled with the trend for higher product complexity adds another layer of challenges for manufacturers trying to gain a holistic view of their product portfolio and ensuring compliance against regulatory and industry directives.
Perhaps the most complex and tedious part of achieving compliance and sustainability goals often resides in the process of gathering accurate and complete data from your supply chain. When I say tedious, I mean people/resource intensive, which translates to very expensive. I have actually seen examples of this process taking manufacturers up to a couple of years to complete. Based on this example and numerous others, I believe it is critical for manufacturers to require full material disclosure from their suppliers, more on this point later.
Manufacturers will need to focus on supplier interaction and automation of their supplier processes by using a multi-faceted and “best-practice” approach, which could include a combination of the following functions:
Email automation to include:
- The process of requesting supplier declarations via email
- The process of polling and processing the email server for supplier responses
- Automatic tracking of suppliers responses
- Tracking supplier declaration expiration dates
- Initiating a re-request process when a supplier declaration has expired or has failed validation
Web portals that enable suppliers to receive PLM process requests and submit their deliverables:
- Integration to on-line databases such as IMDS, BOMcheck, Total Parts Plus to get accurate and complete data from suppliers
- General PLM framework capabilities to enable the exchange of different document types while supporting multiple standards including IPC 1752, 1755, 1753, IEC 62474, EiCCGeSI and others.
Note: Be aware that when choosing which industry standards to embrace, more is not always better. The more options you give your suppliers the more your support costs will increase.
Using an enterprise PLM framework such as Teamcenter to automate the process of gathering and managing supplier disclosure data, manufacturers gain a more complete and accurate understanding of their product. With a more holistic view of their product BOM, manufacturers can be confident in the results they receive when running compliance checks, analysis or any other type of function during the development process. This in turn will help them achieve their sustainability goals, gain a competitive edge, and ultimately win in the market.
About the blogger: I am the Teamcenter product manager for the Substance Compliance and Integrated Material Management solutions.