Are manufacturing data management practices converging with plant engineering?
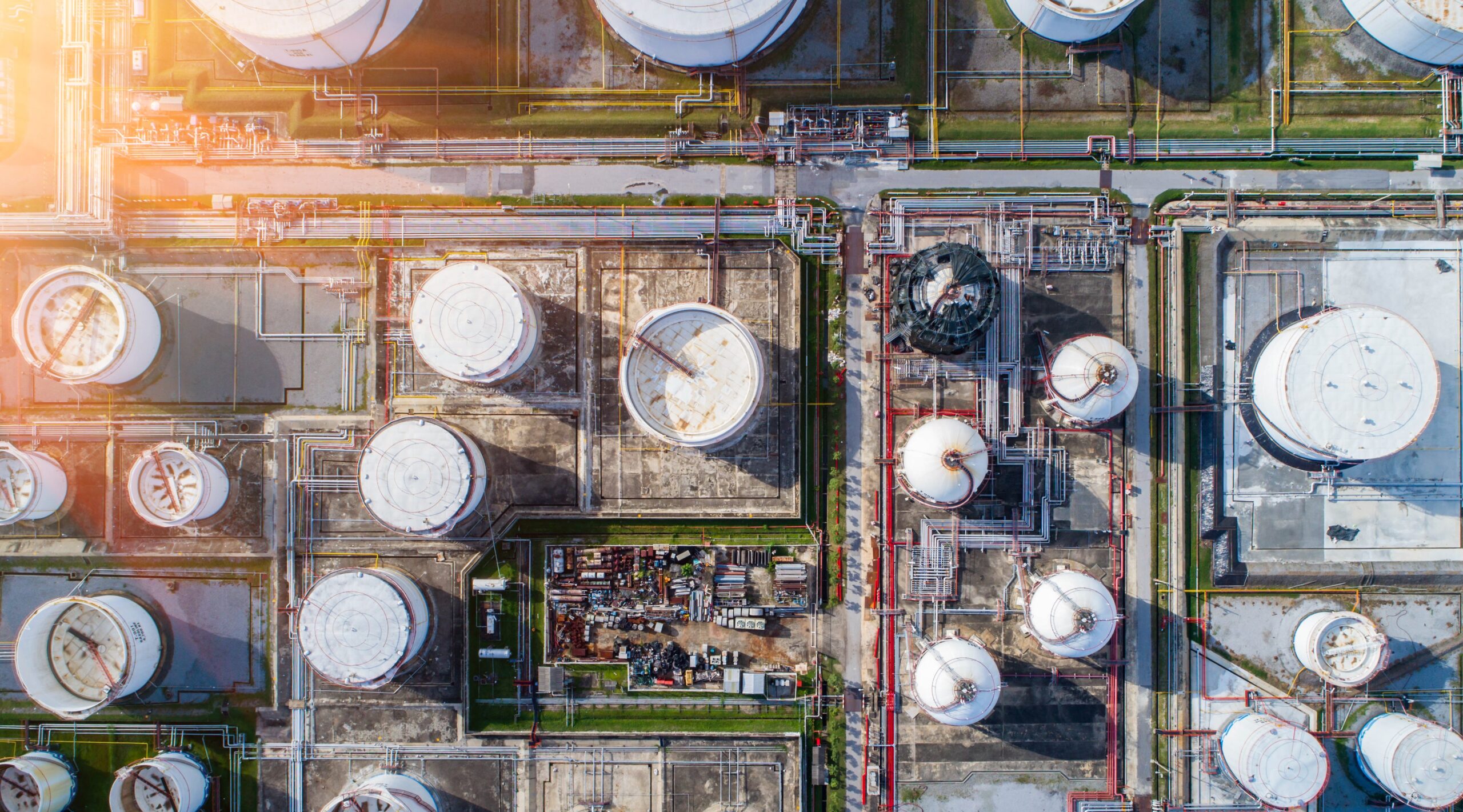
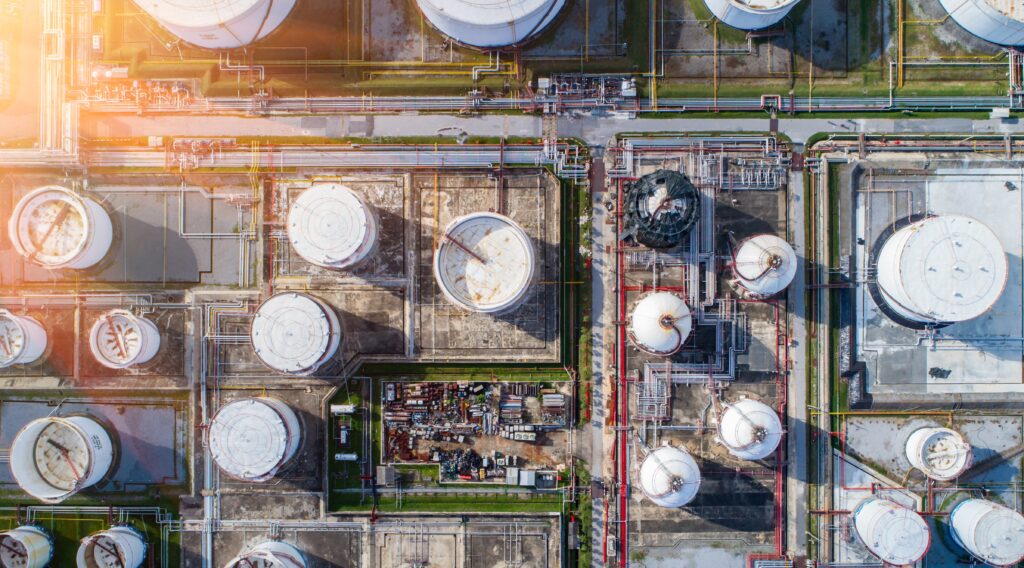
This new decade has brought forth a complex set of challenges as it relates to industrial plant engineering. With increased market volatility, disrupted supply chains, and a push towards more sustainable production, process & discrete manufacturers are seeking more operational efficiency through new technology and through the prioritization of projects where their plants can be relocated, extended, or modernized.
With these rising demands, our customers are pushing the boundaries of traditional software silos and we are seeing demand for the convergence of AEC/BIM, PLM, and Plant software tools and their underlying data in a single environment. The interest we see spans many industries – from automotive and energy to mining and consumer goods. And, to answer this challenge, we introduced our Capital Asset Lifecycle Management (CALM) solution based on the Teamcenter software – a Forrester leader in PLM. With our information management solution, we bring together your data from best-in-class plant engineering / BIM tools and merge it with other information formats and sources such as mechanical and electrical CAD, point clouds, MES, ERP, and EAM. This single source of truth doesn’t just help design and engineering teams, it serves as a foundation to how your organization streamlines business processes such as the management of change as well as your digital handover processes from suppliers. It ensures your maintenance crews, control room crews, and operational systems are relying on accurate information. It also ensures you have the information needed for safety and regulatory compliance.
One of the more notable hurdles standing in the way is variability in the way data is managed and viewed between plant/process manufacturing and product/discrete manufacturing. Plants typically manage assets by “tags”, while discrete manufacturers manage part numbers as part of an assembly or bill of material (BOM). Additionally, the plant data also needs to be viewed in various ways – such as “plant”, “area”, and “unit”. With Capital Asset Lifecycle Management, we’ve accounted for this variability and can deliver both native and third-party integrations to leading tools and systems.
You may already be aware that we can manage 3rd party plantCAD and BIM from vendors such as Autodesk and AVEVA. However, more recently, we introduced our native integration to Siemens COMOS for plant engineering. With this integration you can visualize, search, and cross-probe the COMOS plant hierarchy data with COMOS P&ID data, all within the Teamcenter CALM solution. Using the COMOS integration, design teams can quickly search and access COMOS plant hierarchy and documents to eliminate time wasted trying to find and share information. This solution enables you to make the transition from document-centric business processes to data-centric business processes. By streamlining your business processes, your organization can eliminate unnecessary change orders and improve review & approval time by ensuring everyone is working from the latest design information. And, the same principles can also be applied to how you manage your requirements, enabling you to verify and validate the engineering design to ensure completeness, correctness, and consistency. Lastly, our document management capabilities deliver centrally managed workflows to facilitate the document revision, review and release process.
In summary, we’ve seen an increasing number of organizations looking to increase operational efficiencies and achieve economies of scale through a combination of new technologies and rationalization projects. A large part of this effort centers around the convergence of data from different systems, tools, and domains such as manufacturing and plant engineering. Teamcenter for Capital Asset Lifecycle Management was built to merge these lifecycles in a single holistic view – known as the digital twin. This could include infrastructure information about the facility, the factory & line layout information, plant engineering information, and/or the product information. Most importantly, our solution ensures this accurate information feeds your supply chain and maintenance systems, helping you meet new operational efficiency KPI’s and the increasing demands of this new decade.
Want to learn more about our solution or our native COMOS integration? Click the image below to find out more.
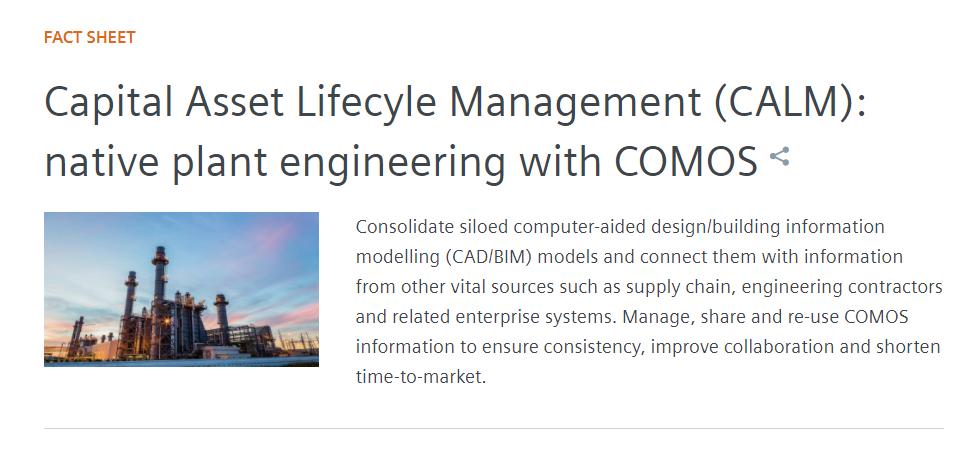