Configurator and Service Organizations
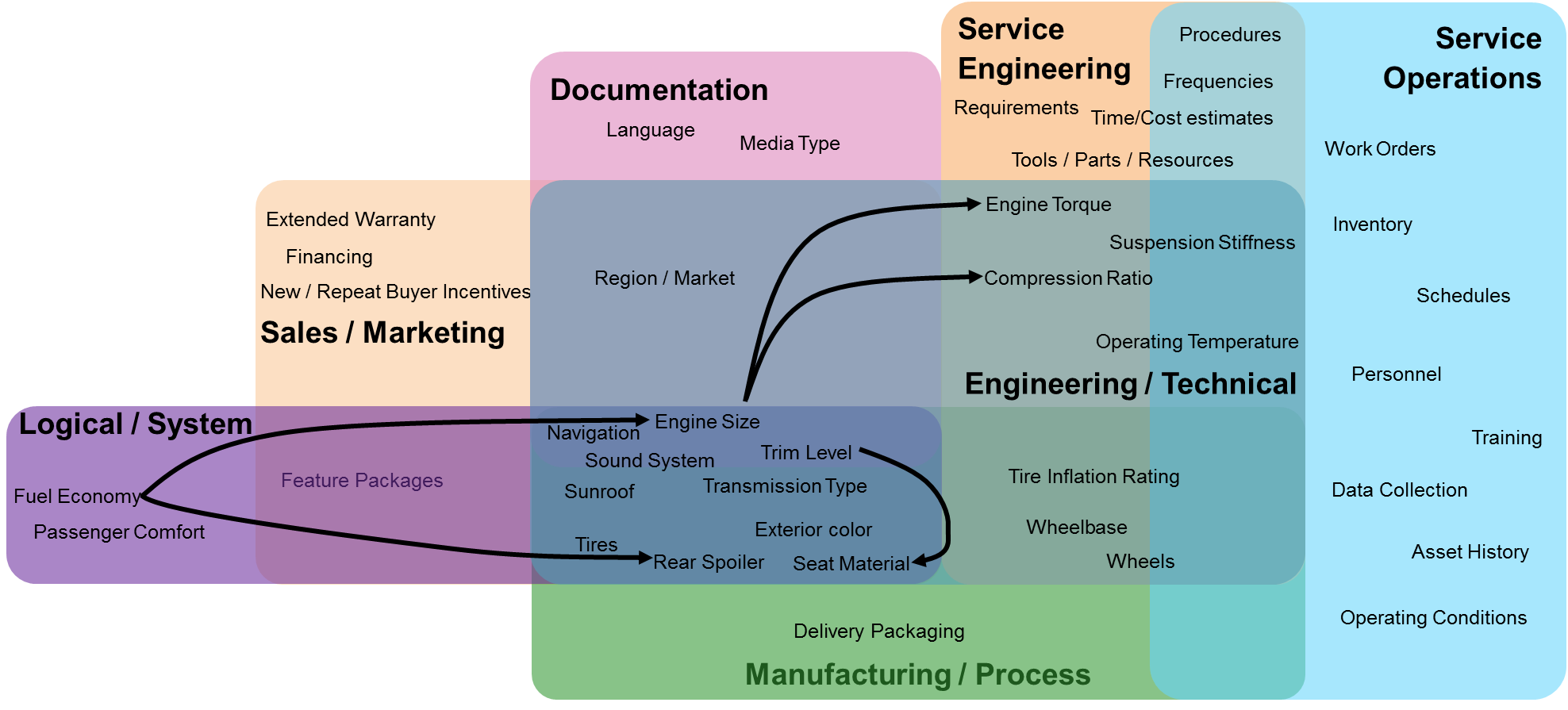
Managing product variability for a service organization poses several unique challenges and opportunities. Over the last couple months, my colleagues have explored many aspects of variability management in the series Beyond Product Configurator Software: Total Variability Management. I’d like to continue that discussion, focusing specifically on service organizations.
The Complexity of Product Variability for Service Organizations
To operate efficiently and effectively OEM service departments operate in parallel with product engineering during the development of a new product.As a new concept is being planned, product development determines the functional, safety and environmental requirements of a product while service adds in the RAM (Reliability, Availability, and Maintainability) requirements of the product.These requirements define the preferred and alternate parts, suppliers, and downstream maintenance frequencies for the final assets delivered to the customers.
Today most OEMs are providing increased flexibility in their product offerings allowing customers to configure their assets based on a selection of options and modules to meet their specific needs. To the service department this expanded complexity requires additional planning to maintain these assets needing to know:
- What options were selected for a specific unit?
- What was actually built? Were any alternates, substitute or deviated parts installed?
- Which parts are allowed to be used together? Are there incompatibility considerations?
- What is the applicable service required?
- Are there any upgrades, recalls, or service bulletins required?
The end result is to deliver the most efficient and effective work package to the technicians to ensure service work is done correctly the first time.This requires the correct parts, tools, procedures, documents and instructions to perform the required work for that specific asset, while staying compliant with the mandatory maintenance requirements ensuring that the asset remains in an optimal and safe state of operation.
A full lifecycle BOM and configuration management system becomes a critical tool to ensuring that service work is based on the actual asset and not on a generic service plan.
We first introduced a variation of this image to help illustrate the ability of the configurator capabilities in Teamcenter to support specialization and subsetting of options to meet the needs of different user communities. I expanded that view now to include Service Operations.
Leverage Engineering Data
While product development is underway, the service engineers can refer to the engineering data such as BOMs, drawings, schematics, and specifications to plan the service work leveraging the knowledge that only the OEM has.
- By planning off of engineering bills of material and 3D data the service engineers can understand the interfaces, layouts, and position of the parts to be maintained. This ensures the service engineer knows which parts and tools to use, if there are any obstructions, and properly plan the procedure to perform a service task.
- Leveraging the initial RAM requirements for the product along with the risk analysis and Failure Mode Effects Analysis (FMEA) information service engineers can plan appropriate frequencies and periodicities to perform routine maintenance.
Product configuration for physical units offers the service teams an accurate list of parts to plan against.This not only defines the replacement parts and tools when doing work, but also can give guidance on how the work procedure and steps will performed based on the 3D visualizations.
Stay up to date with design changes after delivery
Engineering changes occur during both product development and continues during the operation of the fielded units.This may be based on product improvements, safety updates, or simply a change of suppliers. When these changes occur it is critical to understand the impact:
- What fielded assets require a critical service bulletin?
- What is the impact to the service requirements and service procedures based on these changes?
- Will this change cause upgrades to fielded assets?
- Are any parts obsolete or conflicting?
Whether during the design phase or for fielded assets, the BOM can be a moving target of engineering changes that will impact the service requirements and resources. The configuration management system keeps the teams synchronized with up to date and relevant information to ensure that the final asset can be delivered to the customers on time, and fielded assets are current on the latest approved configuration.
Understand the available options
Product configurators provide the flexibility to customers to get exactly what they want, by selecting the compatible options that they need to meet the purpose of the asset.
- These options need to be understood by the service engineers to make sure that they plan the service that is applicable for the installed components. Also, different options may change the service intervals of the asset.
- The service requirements need to be able to adapt and possibly be configured accordingly based on the options and configuration of the built units.
- Customers may want to upgrade the fielded units with the latest options and modules. This may be a simple part replacement in the shop, or a scheduled overhaul to the units. To plan this, the configuration system needs to reconcile what is currently installed on the asset against the new “To-Be” configuration to identify what needs to be replaced, or added.
A product configurator interfaced with the configuration management system can help keep alignment between the service offerings and requirements with the available options offered by engineering.Also, it can provide insight and “what if” scenarios allowing the comparison of these products and assets to new configurations.This allows both the service team and the customer to understand the impact of changing the options installed on the asset.
Configured service work packages
The end result is to deliver an accurate work package to the maintenance teams taking into account all of these variables above to define the service work required on a specific asset.This is where configuration management plays a vital role identifying the final tasks, parts and tools.The configuration will also be validated that the updated asset is compliant with all of required work and consists of authorized parts to operate safely and in optimal state.
By effectively managing the configuration of your product definition tied with your service definitions, the increasing complexity of maintaining highly configured products can be reduced.This ensures that the service requirements, procedures, parts lists, and resource requirements stay up to date with the evolving nature of these product line.
Other discussions in this series include:
Beyond Product Configurator Software: Total Variability Management
Configurator for Product Management and Planning
Configurator for Engineering and Manufacturing
Configurator for Enabling Customer Choice
After-sales BOM and Configuration
Accelerating Lead Times for Engineer to Order (ETO) Processes