Design Collaboration: ECAD-MCAD Co-design
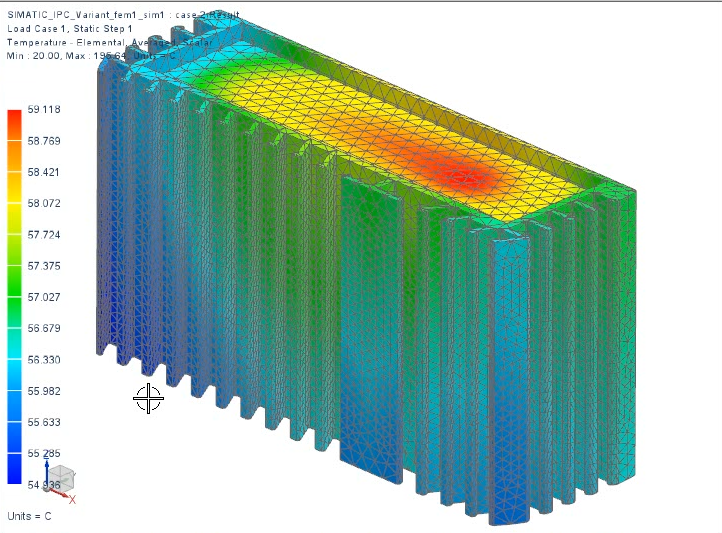
ECAD-MCAD Co-design … where design collaboration is optimal!
Learn more by watching this webinar, “Cross-domain design collaboration,” as part of our webinar series on strategies to streamline product innovation.
When we think about today’s high tech products they typically involve a collaborative ECAD-MCAD design process between the Mechanical and Electronic design teams. This is important because ECAD-MCAD co-design processes can be spread out across multiple geographically dispersed locations. To be effective, each domain must work closely with one another in the timely exchange of design information to ensure the product can be designed, will function as the requirements dictate and will meet both the mechanical and electrical constraints.
Operating in their PLM environment ECAD and MCAD design teams can keep their designs in sync while sharing information on the initial design or collaborating on changes as the design evolves. Changes, or updates to the design can be shared on an incremental basis (verses having to pass the entire design). Both the ECAD and MCAD designer can accept or reject changes, as well as incorporate change notes or comments into the information being shared.
To facilitate true ECAD-MCAD co-design and support the sharing, collaborating and cross-probing between the ECAD-MCAD design data requires the establishment of a common ECAD/MCAD part library definition. The Siemens PLM ECAD and MCAD tool integrations support “items as a part type” which enables a single item definition for all representations of the part including the ECAD footprint and symbol and the MCAD 3D view (i.e., PRT and JT), as well as any common or specific ECAD and MCAD attributes.
In addition to sharing the information across the ECAD and MCAD design processes, the same design information can be shared with the CAE engineer who needs it to perform a variety of simulation and analysis functions, such as evaluating thermal, vibration, shock, dust, and humidity effects.
As a part of the “issue management” process where you reference the specific design, track the exchange of design data, and issue status throughout the product lifecycle, you can also receive notifications when changes are proposed and/or accepted by the other team members.
Watch ECAD-MCAD Collaboration for Co-design of Smart Products and Eliminating ECAD-MCAD Domain Barriers with Siemens NX to discover some of the benefits of true ECAD-MCAD Co-design.
To learn more about managing your PCB design data and processes read these blogs focused on PCB Design and Data Management and PCB Parts Library Management.