Enterprise-wide PCB parts library management … take back control!
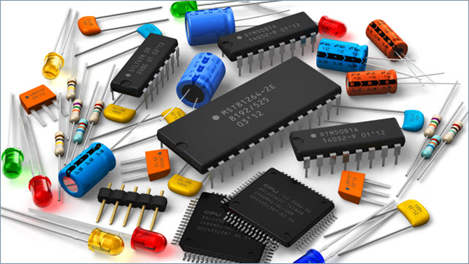
It’s time you took control back from your enterprise-wide PCB parts library management.
On average, PCB components constitute about 35% of a products cost, so management of the PCB parts library is critical in your ability to produce cost competitive products. However, in globally distributed design and supplier environments, multiple PCB tools (each with its own PCB parts library and control processes) are frequently used. This contributes to the long list of issues including: multiple libraries, part duplication, data inconsistency, use of unauthorized parts and organizational inefficiency.
With today’s shortened innovation cycles, environmental requirements, and decentralized product development, the enterprise-wide management and organization of your PCB parts library’s sourcing information is vital, and it’s even more important to complete it in the PLM environment you use to manage all your other domain’s design data.
By leveraging your PLM environment for PCB part library management, your design teams can consolidate all of the various PCB tool’s distinct library information into a single secure location, making it available for use across multiple PCB tools. Once the library information is consolidated in your PLM environment, you can synchronize its library data with each individual PCB tool’s local library – thus ensuring accurate and consistent information is available throughout your organization regardless of the PCB tool being used. By establishing specific access privileges, structured workflows, and formal approval processes, you can prevent design teams from using unapproved, obsolete, or out-of-date parts when incorporating changes.
Once in PLM, you can also do a better job of managing and coordinating with vendors and suppliers as well as fostering environmental compliance initiatives. Since PLM provides the ability to capture, track, and manage all of the vital information that defines each vendor’s location and points-of-contact – you can establish relationships that identify a vendor as a “preferred” supplier or even a “back-up” supplier. This information is especially useful when creating assembly bid packages for contract manufacturers and can dramatically reduce component sourcing cycle times, lowers part costs, and facilitates more informed and equitable buying decisions.
Since environmental compliance directives, such as RoHS, REACH, WEEE and others are constantly being updated, managing the PCB parts library in PLM makes it easier to leverage the sustainability and compliance management capabilities needed to meet the compliance requirements established by these directives. Within PLM, you can analyze an individual part, a product BOM, a group of BOMs, or even something as large as an entire library. Design teams need to be able to verify environmental compliance and investigate the root cause of any failures before costly mistakes make their way into the product release cycle.
To learn more about the benefits of managing your PCB parts library in Teamcenter watch this video.