How a service knowledge management system fills in the blanks
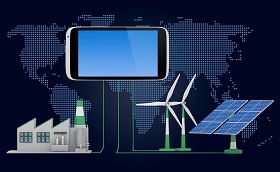
I saw an old commercial on TV the other night I hadn’t seen in decades. I’m sure many of you know it. An elderly woman is laying on the floor, and she clutches a device around her neck before saying those famous words: “Help! I’ve fallen and I can’t get up!”
The ad, which was for a product called Life Alert, got me thinking about the Internet of Things, better known as the IoT. The IoT is all about products communicating their status from the field. This seems like a new concept, but connected products have been around for quite some time.
Most of us have seen and used a vending machine. At one time, if you hung around one long enough and listened, you might’ve heard it dialing out to the distributor to report sold inventory or racks that needed restocking.
So what does a vending machine have to do with today’s IoT and servicing products in the field? Manufacturers today think it’s a cost-effective technology, thanks to inexpensive sensors to design products that “phone home” with status reports or cries for help. Today, that communication may use the Internet directly, a cellular network, or a combination of both to get through to manufacturers or service providers.
With Life Alert, initial communication was a single bit of information: someone needed help. But the volume of data available today is astonishing. A jet engine, processing plant, or a machine in a factory with sensors can send gigabytes of data taken at a rate of thousands of samples per minute. That Big Data can represent many conditions such as temperatures, vibration, pressure readings, utilization cycles, or interactions between systems.
Much of this data is a snapshot of a product’s performance. If the product is smart enough, it might send error codes or alerts that can be recognized and immediately acted upon. If it isn’t an error code, the volume of data probably isn’t necessarily processed in real-time. Think of thousands of jet engines sending gigabytes of data. That data may require more detailed analysis before it can guide current and future product development, or more importantly, service activities for currently fielded products.
Why you need a service knowledge management system
Even with everything that’s available from IoT or Big Data, key information is still missing. For the vending machine, if the distributor didn’t know what was in each rack, the wrong snacks could be brought out to restock the vending machine. These could negatively affect sales. It’s this missing configuration information I want to talk about.
A lot of the talk about Big Data and IoT involves learning more about product performance to improve a product’s design. That’s great for the future, but what about operational problems now? How do we use the information that IoT delivers to get smart, actionable data we can quickly use?
We need something else. We need a service knowledge management system that’s part of a larger service lifecycle management strategy. That strategy can help us execute faster, smarter service and deliver better value for customer investments.
It may sound like overkill, but think of how this kind of service knowledge management system would help that vending machine distributor. Wouldn’t it be better if the distributor had precise knowledge of what food is configured in each rack and when it was stocked? He’d know what is and isn’t selling and what snacks are expiring. He could prevent customers from having bad experiences with that machine.
With this extra bit of knowledge, the distributor could bring the proper inventory to restock the machine, change out expired items and make fewer trips to do it. A smart vending machine may have that information, but it’s probably more efficient to have a central knowledge base of all the managed vending machines with their snack configuration and turnover stats. That’s how the distributor can maximize revenue, and that’s how our customers can maximize their revenue.
This concludes part one of our series on using smart data to have smarter service. In part two, Steve O’Lear highlights how a service knowledge management system could help a pump in a deep-sea oil rig. Stay tuned.
About the author
Steve O’Lear has been in the information system industry for more than 35 years. He has held positions in consulting, services management, sales, and marketing across computer hardware, timesharing services (cloud), supercomputing, and customs information management solutions for various industry segments. He has more recently focused on PDM and PLM, and many of his customer engagements have been in the A&D industry and with discrete manufacturers. He is currently focused on product marketing for solutions related to document management and service lifecycle management. Early in his career, Steve recognized the need for manufacturers to manage product development data and processes more holistically and became involved with the development, implementation, and marketing of PDM solutions. He has also recognized this need with PLM and is now promoting the importance of the support phase in the product lifecycle as products become platforms for service for manufacturers.