Managing Materials, Beyond Material Compliance
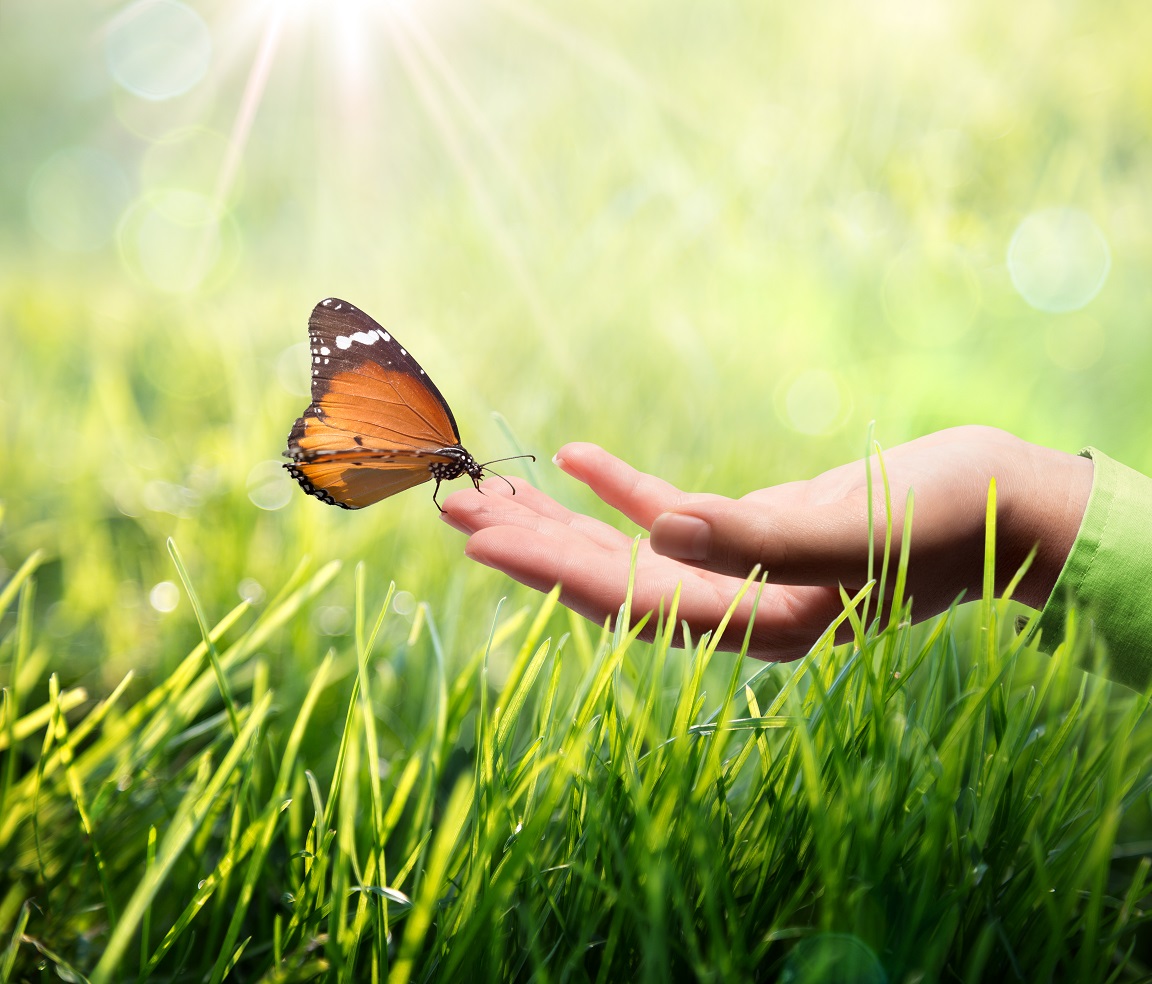
In my previous posts, we’ve discussed material compliance in the context of addressing the U.S. conflict minerals reporting requirements, and also the importance of supplier materials disclosure.For this article, I will focus on the important topic of materials-driven product design and innovation.
Materials-driven innovation is at the forefront of breakthrough products on the market today.Many innovative product designs owe their success to the revolutionary use and discovery of new materials – from smart appliances, to lightweight and electric vehicles, to green energy equipment (wind turbines, solar, etc.), to medical devices, and more.
For instance, take the bold example of material innovation from Ford Motor Company. The massive, century-old automaker made the drastic decision to alter the design of its longstanding and flagship F-150 model truck by using an unconventional aluminum body frame as well as other advanced, lightweight materials. This move was significant insofar as it defied convention and took a tried-and-true formula and heavily innovated it, making the vehicle lighter and more efficient in the process through the use of more efficient materials.
It was a risky move for an established, successful company to make, especially on what has been the best-selling truck in North America for nearly 40 years. However, Ford saw the opportunity to adapt, improve, respond, and innovate by incorporating more advanced materials into a signature product.And it appears that the risk paid off – sales for the new F-150 continue to rise and Ford’s two truck factories are working to keep up with high customer demand.
Material innovation requires a holistic view of material data used in all phases of the product lifecycle to help improve quality and reduce development cost.Materials management has multiple threads throughout the product development process, through research and development, design and analysis, quality and compliance, manufacturing and ultimately right into the field.These are threads that demand good practices and traceability, from sourcing through to the consumer and, if applicable, across re-use, recycling and disposal or decommissioning. Managing materials information broadly can have an enormous effect on the lifecycle of a product, its success in the market, and ultimately, the bottom line.
The thread of compliance should run through that of good materials management in sync with all other facets like traceability. Identifying 3TG suppliers and conducting due diligence on the source and chain of custody of minerals is an intricate core PLM weave. As the chain of responsibility increases and complexity of compliance in materials management presents different challenges, the efficiency of the technology used to manage materials becomes more relevant and crucial to the overall mix. Beyond compliance, materials-driven product innovation will require holistic materials data management, and validating materials and material use throughout the product lifecycle.
Material data silos have become hurdles to manufacturers today and hinder holistic materials data management objectives.With an influx in regulatory requirements, product line complexities, and customization of products for global markets – manual processes to manage materials data together with product development data is no longer a sustainable solution.Boundaries between materials management systems, CAD systems and product lifecycle management (PLM) systems can be eliminated by integrating materials data management with PLM.
Here are some examples of the benefits to manufactures who integrate materials data management to the right PLM solution:
- Streamline processes for tracking and reporting materials used in products down to the substance level
- Improve material data integrity of parts
- Improve material interoperability with suppliers
- Proactively manage direct and indirect material costs
- Reduce time to prepare material data for structural, crash, thermal, aesthetics and acoustic analysis
- Improve manufacturing processes and quality
Materials are fundamental to manufacturing, and integration of materials data management into PLM is essential to accelerating product innovation and staying competitive.
About the blogger:
Matthew Littlefield co-founded LNS Research in 2011 and is now President and Principal Analyst. In this role Matthew oversees LNS’s coverage of the industrial value chain, including EHS, MOM, APM, and QMS. His personal coverage includes digital transformation and the Industrial Internet of Things. As a recognized industry expert he contributes to the widely read LNS Research blog as well as many other industry publications. Matthew is also a sought after public speaker and continually advises manufacturing executives on how to best leverage technology in their operations.