New Teamcenter Product Cost Management Capabilities
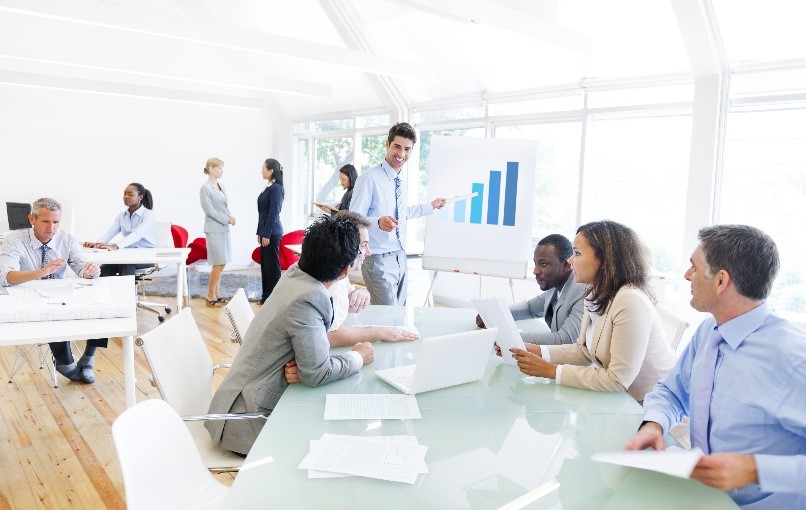
B2C and B2B markets have evolved. Manufacturer competitive position is even more determined by the ability to innovate their product portfolio and the time required to introduce new products to the market. Manufacturers have to launch new sophisticated products in increasingly fast cycles and their ability to ramp up to full scale production volume rapidly is crucial for success. Also the individualization and complex demands on consumer side due to e.g. localization of products has an impact on manufacturing companies by exploding number of RFQ’s that finally increases volume of work in costing.
To help manufacturer provide answers to these key levers and responding to customer requests we enhanced many of the Teamcenter product cost management capabilities and incorporated new capabilities as well. Here are the highlights.
Integration with the Siemens PLM Software portfolio – With the integration into Teamcenter we enable cost engineers to participate and contribute to the product development lifecycle in an efficient manner to ensure to have the right information. What does this mean exactly?
Receive 3D Data at a glance for product and tool cost calculations: Teamcenter product cost management users are able to import a configured structure of a BOM from Teamcenter and the links to the related JT-Data. They have the possibility to open in Teamcenter product cost management a 3D model in the integrated viewer and extract the relevant parameters such as thickness, surface, volume for the calculation. There is a continuous workflow without manual entry of values. This means if an engineer is updating a part in Teamcenter the cost calculation for this part is updated automatically in Teamcenter product cost management. As a result cost engineers are faster in their calculations with less error prone since they can open only the files which are relevant for them. Since they have now access to the latest versions/revisions calculations are always up-to-date. No more calculations on outdated engineering data! IT complexity can also be reduced since there is no data redundancy and the required storage capacity is reduced. Data do not need to be saved locally but only centrally on FMS (file management service).
Here are more exciting new Teamcenter product cost management capabilities which improve calculation accuracy, usability and performance:
Part revision – Clear traceability of changes occurring during the product development: Users can better track changes that are made within the calculation process with the costing structure. They can align the calculation history to the product life cycle and compare easily two versions of calculations from the history.
Master data management and consumption: A significant part of the data structure was re-engineered and enhanced to gain more flexibility, consistency, and increase automation to drive standardization and effectivity.
- New classification engine, that allows classifications to be used by various objects
- A new master data structure that allows to cluster a set of logically related master data
- To find the best match of master data, you can define a look-up strategy. If there is no correct match, the application provides the best-fit data depending on a fallback strategy.
- Consistent management of multiple exchange rates such as time-, customers- or supplier-specific.
Quick Editor – Efficient cost calculation through simple editing of complex product structures: Increased changes of product designs during development process, requires fast adjustments of calculations to enable a quick feedback on cost changes. Version 8.0 allows you to do flexible edit fields for several parts at a glance, in a spread sheet-like manner.
Cycle time calculator for stamping – Extended cost models for manufacturing technology: The calculator for standard manufacturing technologies now includes the new cycle time calculator for stamping.
Calculator for semi-finished parts – Increased transparency on price composition: For some manufacturing technologies, there are a high variety of semi-finished parts, such as: metal plates, coils, tubes, etc. The prices of these semi-finished parts are driven by multiple parameter matrix/tables and can result in thousands of possible price compositions. It causes high administrative efforts to maintain and update every single possible price composition. With version 8.0 manufacturers only need to maintain relevant price tables which significantly reduces time and effort.
Invests for dedicated machines – Enhanced allocation within projects: New capabilities allow to allocate investments for dedicated machines used for several product variants within a project. Manufacturers can share the investment cost depending on the individual occupancy of the product variants. This increases transparency on investment costs within a project.
Cost breakdown – Increased flexibility and reduced efforts on creating cost breakdowns: One of the common challenges is to import several cost breakdown because of different formats or the mapping of cost breakdowns. With the enhancements we made in this area you can import several cost breakdowns from suppliers to have them available for a comparison.
Aggregated profitability – Visualize profitability for multiple projects: Finance can now review profitability cross over multiple projects. This offers an even better overview of several projects (for example, all projects to a customer or an overall view of a product group, etc.) to different groups, like top-management.
All the new and improved capabilities increase calculation efficiency at each stage during the product development phase and enable business analytics/dashboards to make the right decisions.
Read more about Teamcenter product cost management.