Real-time guidance for workers using smartwatches, AI and the digital twin

AI and digital twin technology are pivotal in shaping the digital revolution that is the future of manufacturing. Learn how AI and digital twin technology are transforming manufacturing by providing real-time guidance to workers through smartwatches.
In today’s fast-paced manufacturing landscape, the convergence of artificial intelligence (AI) and digital twin technology is reshaping traditional practices, offering real-time guidance to workers through the subtle yet powerful conduit of smartwatches. Spearheading this revolutionary transformation is Digiteh d.o.o., an innovative firm based in Slovenia, led by the visionary Dr. Hugo Zupan.
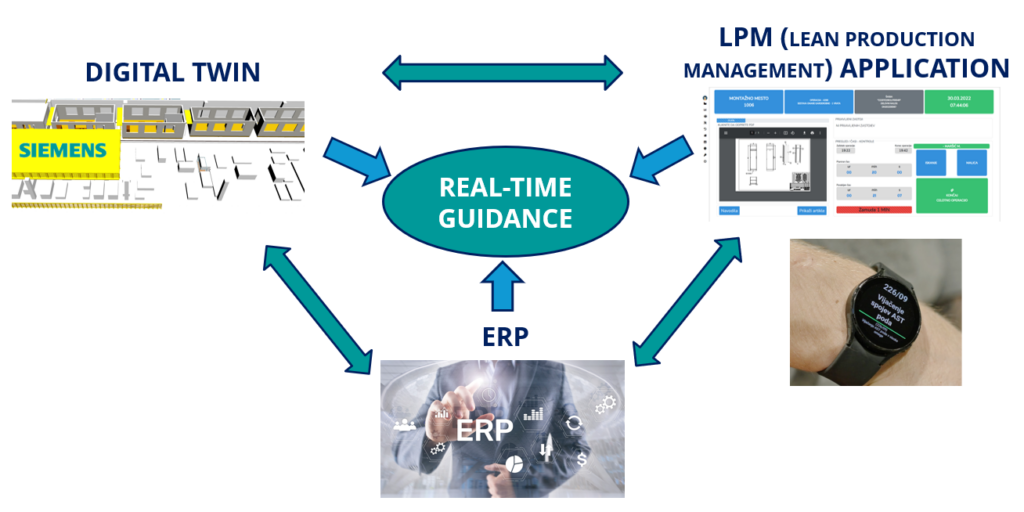
Figure 1 illustrates a sophisticated integration of digital twin technology with enterprise resource planning (ERP) and lean production management (LPM) applications to optimize manufacturing processes. At the core of this system is a digital twin with AI, developed using Siemens Plant Simulation, which functions as the brain of the operation by harnessing the full knowledge base of the enterprise.
This digital twin interfaces in real time with the ERP system, which holds all crucial production data. The LPM application serves as a visualization tool and communication interface between the digital twin and the end users, including workers, team leaders and managers, facilitating real-time guidance through smartwatches. This setup exemplifies how advanced technologies can enhance efficiency and decision-making in industrial settings.
Challenges before the transformation
Before the dawn of this digital metamorphosis, manufacturing entities grappled with inefficiencies and uncertainties. The timing of line movements remained an enigma, hindering the synchronization of operations. Task comprehension among workers lacked clarity, resulting in erratic productivity levels, with some individuals overburdened while others idled away. Production planning bore the weight of excess buffer, hindering agile responses to dynamic demands. Errors, when identified, often led to futile blame games, with responsibilities obscured in the organizational labyrinth. Communication silos between departments fostered a culture of stress and wasted time, exacerbating operational hurdles.
Presenter

Dr. Hugo Zupan stands at the forefront of AI and digital twin innovation. As a director and researcher, Dr. Zupan has translated his academic prowess from the Faculty of Mechanical Engineering at the University of Ljubljana into industrial applications. Renowned as a trailblazer in digital transformation, he has garnered acclaim, notably clinching the prestigious GoDigital award for his groundbreaking advancements in technological solutions.
Throughout his illustrious career, Dr. Zupan has been instrumental in both domestic and international projects, championing the evolution of production and logistics systems. His latest endeavor, hailed as the best digital project of the year, revolves around the development of a cutting-edge system for real-time worker guidance, leveraging digital twins and artificial intelligence. His visionary contributions represent a paradigm shift in optimizing manufacturing processes, promising revolutionary advancements in the industry.
AI and digital twin technology, coupled with Plant Simulation, form the backbone of the future of manufacturing, empowering operational efficiency and productivity.
Dr. Hugo Zupan, Digiteh d.o.o.
The digital renaissance: transformative solutions
However, the advent of AI and digital twin technology ushered in a new era of precision and efficiency. Line movements are now orchestrated with symphonic harmony, synchronizing operations across the organizational tableau. Smartwatches have become the conduits of clarity, endowing workers with lucid task instructions, visible on screens, fostering transparency and accountability. Through the seamless integration of AI-powered insights, workload distribution now adheres to a fine-tuned equilibrium, optimizing individual skills for collective productivity. Disruptions are met with swift responses, ensuring minimal downtime and maximal adaptability.
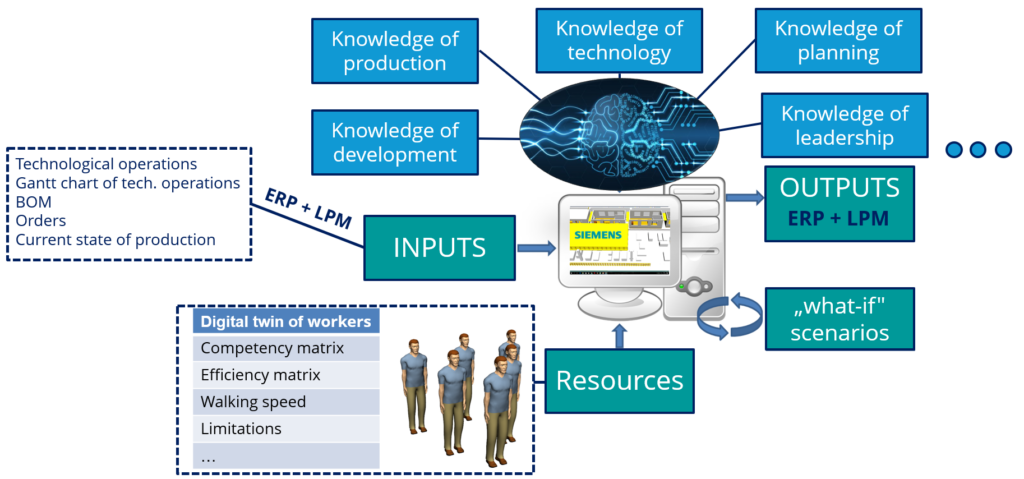
Figure 2 outlines a sophisticated, self-building digital twin system, that dynamically adapts to all production scenarios. This fully parametric system integrates real-time data from both LPM and ERP systems, providing comprehensive insights and supporting continuous optimization. Workers interact with the system via smart-watches, tablets, or PCs, receiving direct instructions and submitting task completions. The digital twin assesses each worker’s skills and efficiency, plans shifts in real-time, and recalibrates every five minutes to ensure optimal workflow and productivity.
The digital twin: orchestrating operational excellence
At the heart of this transformation lies the self-building digital twin, a virtual counterpart that mirrors the nuances of the physical realm, adapting dynamically to evolving scenarios. Workers, armed with smartwatches, seamlessly interface with this digital doppelgänger, receiving real-time instructions that guide their every move. Every task completed triggers a ripple effect, seamlessly transitioning to the next assignment, orchestrated by the ever-vigilant digital twin. Shift planning becomes an art of continual calibration, optimizing workflow and productivity in real-time.
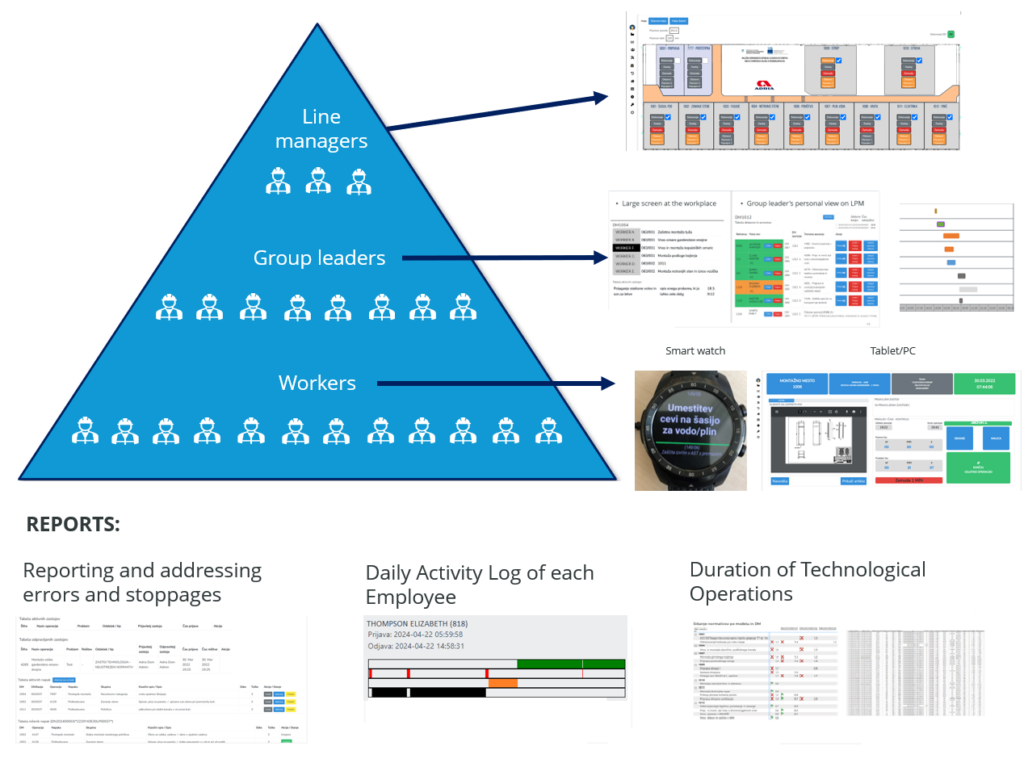
Figure 3 illustrates a hierarchical structure of the Lean Production Management (LPM) visualization tool, which effectively streamlines communication and task management across different levels of the manufacturing process. At the top, line managers have an overview, ensuring that strategic decisions align with real-time production data.
Group leaders monitor and control operations through dedicated screens that display relevant metrics and KPIs. They have the capability to access Gantt charts at any moment to review past activities and forward planning, including the start times of operations and assignment details. At the base, workers receive personalized tasks and instructions directly on their smartwatches, tablets, or PCs, ensuring clarity and efficiency. This system not only improves transparency with visible activities on multiple screens but also promotes an even workload distribution tailored to each worker’s skills. Additionally, the synchronization between smartwatches and central computers allows for dynamic updating of assembly instructions.
Lean production management: visualizing operational symphony
Moreover, Lean Production Management (LPM) emerges as a visual symphony, harmonizing the perspectives of line managers, group leaders and workers alike. Large screens adorn workspaces, offering panoramic vistas into the operational landscape, fostering collaboration and informed decision-making. Workers, equipped with smartwatches and tablets, navigate the digital realm with ease, empowered by real-time process monitoring and accurate information dissemination.
Celebrating excellence: the GoDigital award
In recognition of this transformative journey, Digiteh d.o.o. proudly clinched the prestigious GoDigital award for Best Digital Project of the year 2022, a testament to their unwavering commitment to innovation and excellence.
A grateful journey forward
As we embark on this digital odyssey, let us extend our gratitude to Dr. Hugo Zupan and the visionary minds at Digiteh d.o.o. for illuminating the path towards a future where efficiency, clarity and innovation converge seamlessly, propelling manufacturing into realms previously unimagined.
AI and Digital Twin benefits
The lecture underlines how AI and digital twin technology revolutionize manufacturing by offering real-time guidance to workers through smartwatches. The benefits outlined include:
- Improved operational efficiency: real-time guidance enables precise timing of line movements, enhancing overall operational efficiency and productivity.
- Enhanced task understanding: workers receive clear task instructions through smartwatches, leading to improved task comprehension and execution.
- Transparency and accountability: employee activities are visible on screens, fostering transparency and accountability across the production floor.
- Optimized workload distribution: even workload distribution based on individual skills ensures optimal resource utilization and minimizes idle time.
- Agile response to disruptions: the system rapidly responds to disruptions, minimizing downtime and ensuring smooth production flow.
- Enhanced traceability and analysis: full transparency and traceability in the production process enable detailed output data analysis for continuous improvement.
- Support for shift operations: efficient transition to two-shift operation is supported, boosting productivity and reducing employee stress.
2024 Plant Simulation User Conference
On June 6th 2024 at the 2024 Plant Simulation User Conference, taking place at the Infinity hotel in Munich, Germany, we will delve deeper into this topic. This event, taking place right after Realize LIVE Europe, is an ideal opportunity for attendees to learn from industry experts, network with peers and explore the latest advancements in Plant Simulation software. They will experience presentations like what’s new in Plant Simulation 2404 and engaging discussions that might transform their approach to material flow simulation.
Other lectures at the 2024 Plant Simulation User Conference are, for example:
- https://blogs.sw.siemens.com/tecnomatix/bosch-user-friendly-modeling-plant/
- https://blogs.sw.siemens.com/tecnomatix/decarbonization-strategies-plant/
- https://blogs.sw.siemens.com/tecnomatix/sustainability-bsh-co2-reduction/
- https://blogs.sw.siemens.com/tecnomatix/layout-planning-battery-production/
- https://blogs.sw.siemens.com/tecnomatix/8-axis-log-handler-simulation/
- https://blogs.sw.siemens.com/tecnomatix/ai-and-digital-twin-real-time-guid/
- https://blogs.sw.siemens.com/tecnomatix/electrolux-driving-efficiency/
- https://blogs.sw.siemens.com/tecnomatix/logistics-optimization-heat-maps/
- https://blogs.sw.siemens.com/tecnomatix/smart-factory-plant-simulation/
- https://blogs.sw.siemens.com/tecnomatix/logistics-simulation-modeling-ceit/