Better planning and logistics optimization with Plant Simulation

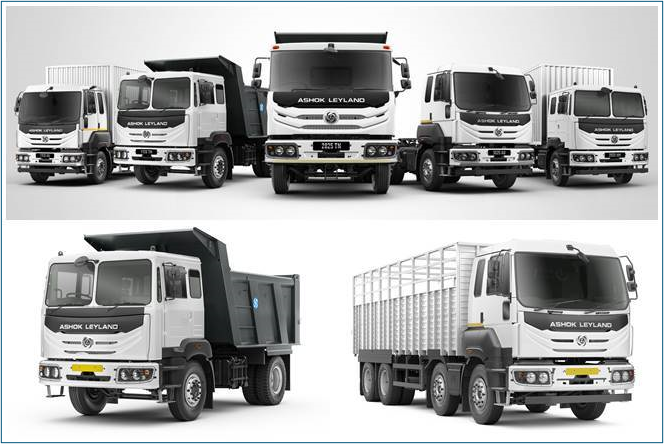
Ashok Leyland implements hybrid match-to-order process for planning and logistics optimization of commercial vehicle production
The Hinduja Group’s Ashok Leyland company is one of the largest producers of buses, trucks, and other commercial vehicles in the world. From its headquarters in Chennai, India, the manufacturer’s business footprint extends across 50 countries. Ashok Leyland faces a challenge common to many companies and industries – meeting customer demand for configuration freedom – but as a leading manufacturer, it faces this challenge on an unusually large scale. This has prompted the company to seek a more efficient and reliable way to plan its production and logistics, one that it has achieved by implementing Plant Simulation in the Tecnomatix® portfolio of digital manufacturing software solutions from Siemens Digital Industries Software.
At Realize LIVE 2021, Siemens’ global customer event, Ashok Leyland shared details of this business challenge, the company’s reasons for selecting Plant Simulation, and the results it has achieved through this implementation. This blog summarizes the presentation.
The manufacturing challenge
As the commercial vehicle market has become more volatile and unpredictable in recent years, Ashok Leyland maintains a competitive edge through continual improvement to the company’s business, design, and manufacturing approaches. One of these changes is a switch from a traditional static product structure to a modular product structure, which helps satisfy customer desire for more variety and configuration options on its vehicles.
To accommodate the modular product structure, Ashok Leyland is transitioning to a “match-to-order” (mTO) business process, which is a hybrid of conventional make to order (MTO) and make to stock (MTS) approaches. In the mTO production planning process, the plan is first created based on orders in the sales funnel. New orders are checked against model and stock availability, and they are added to the plan with a firm commitment date. A major requirement of the mTO process is to generate reliable delivery dates based on constraints, which helps to build customer confidence.
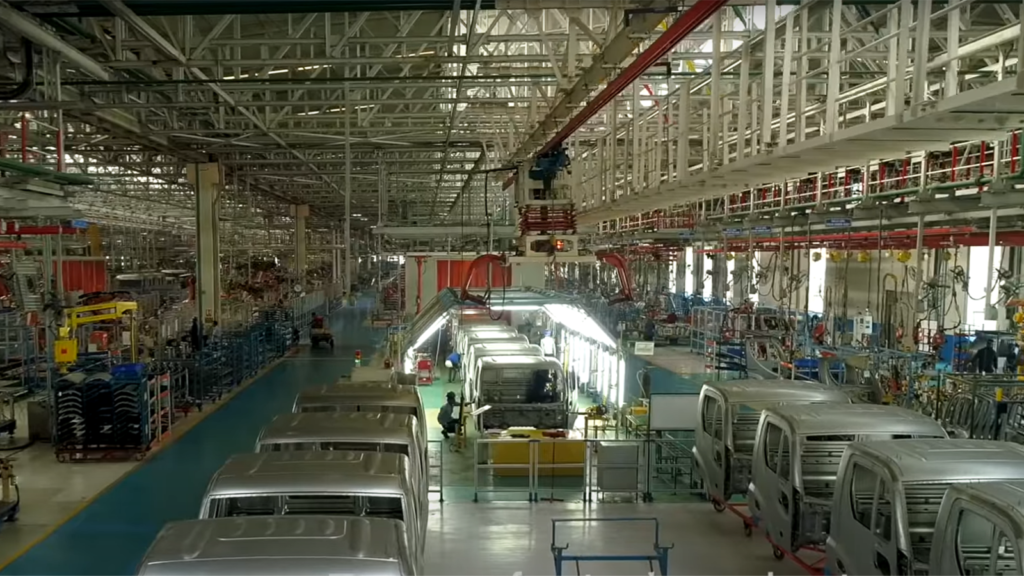
The mTO approach is not well suited to Ashok Leyland’s existing planning process, which relies on manual entry and manipulation of basic spreadsheets. The process becomes more difficult and time-consuming as the number of vehicle variants increases, and it imposes high lead times to respond to demand changes. “As the orders are going to be more dynamic,” explains M. Chandrasekaran, Ashok Leyland’s head of central planning, “generating a plan manually for dynamic market needs with lots of constraints will lead to a non-optimized production plan.”
Meeting mTO requirements is also a complex undertaking because Ashok Leyland is applying its modular product structure and new business process to operations that include:
- More than 10,000 demand orders from more than 40 area offices
- More than 600 vehicle configurations/variants
- Six vehicle assembly lines across 4 plants
- More than 60 critical parts or aggregates from external suppliers
This combination results in more than 60,000 decision variables. Additionally, the planning process must accommodate:
- Prioritizing mTO over MTS orders
- Minimum lot size for specific vehicle configurations
- Export prioritization
- Aggregate prioritization
- Inventory holding
- The applicability of each production line to the product model
Given all these considerations, Chandrasekaran says, “It would be impossible for a planner to allocate or optimize this demand manually. The need for an automated software solution to generate a production plan that is more reliable, answering the internal constraints and external constraints, is highly needed. That’s the reason we went for a software application to provide a solution for this problem.”
Implementing the MPS Optimizer
Ashok Leyland is using Tecnomatix Plant Simulation to plan a 12-week demand cycle at its four plants through what the company is calling its Master Production Planning and Scheduling (MPS) Optimizer for production planning and logistics optimization. The system receives order information from the company’s enterprise resource planning (ERP) system, and this information is used to generate an initial 12-week plan. The planning team then runs a plan optimizer that balances demand with capacity at the four plants. A second optimizer fine-tunes the plan at the plant level. After optimization is completed, the system generates a production plan, which is sent to the ERP system for delivery of the 12-week plan to each plant.
Plant Simulation offers Ashok Leyland high visibility into the production plan and actual production outcomes with its user interface. Details can be displayed both graphically on a dashboard and quantitatively in exportable tables. This user interface makes it easier for planners to identify aspects of the plan that can be improved. “They can understand which aggregates are creating bottlenecks,” Chandrasekaran illustrates, noting that the dashboard graphic clearly displays which aggregates are nearing or exceeding capacity. Action can be taken to improve the planning cycle by changing the master data. Detailed reports also provide data on how much demand has been allocated and how many allocations are performed each week.
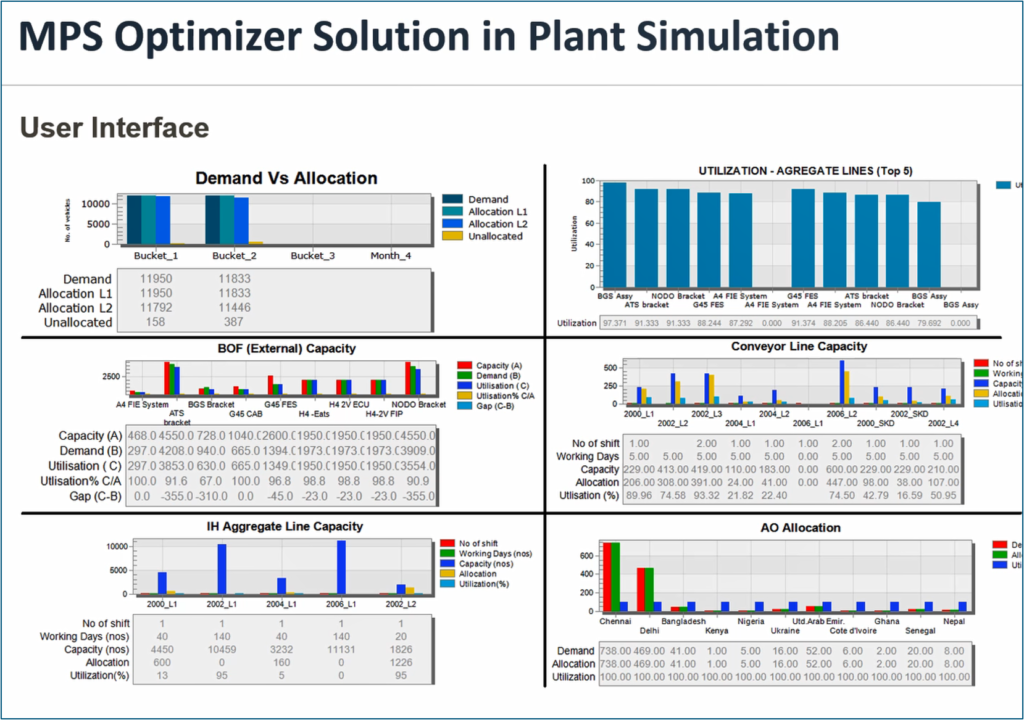
Interacting with the plan via the Plant Simulation user interface, Ashok Leyland planners have also been able to optimize the logistics associated with production and delivery. The system provides logistics information from each area office, detailing the distance to the nearest plant versus the allocated plant distance. To optimize logistics costs, orders can be reallocated to a closer plant. The ability of Tecnomatix Plant Simulation to evaluate outbound logistics represents a feature of the software that is not available in competing software products.
The benefits of Plant Simulation
Plant Simulation has fulfilled the expectations of Ashok Leyland, producing benefits that include:
- Reduced lead time for delivery
- Logistics cost optimization
- Unplanned inventory reduction
- Improved weekly delivery performance
- Complexity reduction in master data maintenance
Ashok Leyland plans to extend the application of Plant Simulation to a Phase 2 “Reverse MRP” optimization program, which will help ensure that older inventory is consumed. The company is also implementing a contribution-based optimization program, in which the production plan is optimized based on which plant is yielding a better contribution.
—–
> To hear more customer success stories like this one or to share your own success, join us at Realize LIVE 2023.