Implementing flexible automation with fully integrated digital manufacturing tools

B/S/H/ leverages Tecnomatix, Teamcenter, and NX to optimize mixed robotic and manual assembly
Munich-headquartered B/S/H/ (BSH) has grown since its 1967 founding from a German exporter to one of the world’s leading home appliance manufacturers. The company manufacturers its entire range of home appliances at 38 factories worldwide. BSH is digitalizing its own products – manufacturing appliances that also offer personalized digital features, services, and content – while digitalization is also transforming the company’s manufacturing floors.
At Realize LIVE 2020, Siemens’ global customer event, BSH presented its approach to integrated digital product and process engineering for both manual and robotic operations on its assembly lines. This blog summarizes the presentation.
The manufacturing challenge
With the proliferation of product variation, including both conventional home appliance technologies and new digitally personalized features, BSH designs and manufactures millions of different products each year. The company’s team of manufacturing engineers must orchestrate the plans for its many factories and production lines, some of which support relatively long lifecycles for each product platform. A refrigerator manufacturing line, for example, may run the same product platform for several years.
The manufacturing engineering team plans for these products while taking into consideration an unprecedented number of variables and factors. Not only does the company manufacture a large variety of products, it also handles a full range of manufacturing steps, from receiving sheet metal to form, weld, rivet, paint and/or enamel-coat appliance housings, all the way through to packaging and shipping the finished products. Additionally, each process must be tailored to the equipment and resources available at each factory. And assembly lines at the plants sometimes include upwards of 50 workstations, with a mix of manual and robotic operations.
“As you can imagine, that brings quite some complexity into our factories, says Frank Helmke, head of the digital factory for BSH Home Appliances Group. “I’m convinced that we need software to handle that complexity.” Helmke’s team is responsible for all digital factory tools used at BSH Home Appliances, including those used for factory layout planning, production process planning, and process and logistics simulation.
Succinctly put, the challenge for Helmke’s team is to meet the goals of quality, productivity, cost and time, achieving required production output levels. An important key to meeting these goals is the team’s efforts to foster flexible automation. “With single-purpose automation,” Helmke explains, “we call an external partner, who performs the programming [of robots and automated systems], but they have to be called again anytime there is a product or process change.”
Recent enhancements to the BSH digital factory are designed to empower the manufacturing engineering team to implement changes that help optimize assembly operations.
An integrated manufacturing engineering solution
BSH is meeting its digital manufacturing needs with an integrated software solution on a Siemens Teamcenter® software platform. Products from the Siemens Digital Industries Software portfolio that BSH employs in its digital manufacturing software solution include Teamcenter Manufacturing Process Planner and Easy Plan applications, which the BSH engineering team uses to author, analyze and manage manufacturing process plans and communicate them to internal and external stakeholders. The solution also includes Line Designer based on NX™ software as well as Process Simulate and Plant Simulation in the Tecnomatix® portfolio.
“We share the Teamcenter system with product development,” Helmke adds, “which means all product data is inside. We as industrial engineers can consume that product data to define the processes.” The Teamcenter platform also interfaces with other BSH digital systems, including the company’s enterprise resource planning (ERP) and manufacturing execution system (MES).
Helmke illustrates the value of the company’s integrated digital factory with two recent projects that are improving process efficiency: (1) optimization of manual assembly line work and (2) incorporation of more lightweight robotics on mixed manual/robotic assembly lines.
Optimizing manual assembly line work
Goals of this project are to optimize the efficiency both of the operators performing manual assembly tasks and of the assembly line as a whole. With TiCon software for Teamcenter, BSH has implemented time studies using the methods-time measurement (MTM) approach. The company has also performed ergonomics assessments with Process Simulate Human. The project employs the ergonomic assessment worksheet (EAWS) method and motion capture technology.
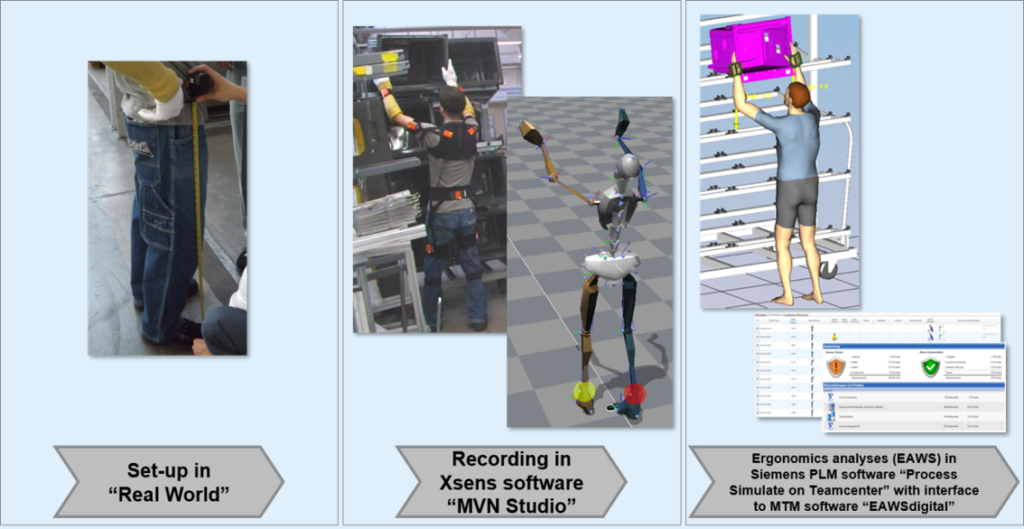
These assessments provided the manufacturing engineering team with data on which to build the optimization effort. They combined variant information with operations data to perform line balancing, which distributes manual tasks to the workstations along the assembly line in a way that helps maximize productivity and output. With line balancing completed, the integrated digital manufacturing system generates work instructions that inform operators what tasks to perform at each workstation. It also creates the product bill of processes (product BOP) and the local process plan (plant BOP) along with ERP routing information.
Incorporating more automation
Many BSH factories are located in regions of the world that are facing an aging workforce. In response, a major goal of this second project is to transfer manual tasks to lightweight robots. BSH engineers use Tecnomatix Process Simulate Robotics for advanced robotic simulation. “We set up a simulation study to validate if a certain automation project makes sense,” Helmke says.
Helmke outlines a couple successful transitions from manual to automated tasks:
Cooktop manufacturing line – As sheet metal is surface treated it is transferred from one hanging conveyor to another. BSH chose to automate this complex process as an opportunity to put the integrated digital manufacturing system through its paces. “It allowed us to validate the robustness of the new version, from study to robot execution,” Helmke recalls.
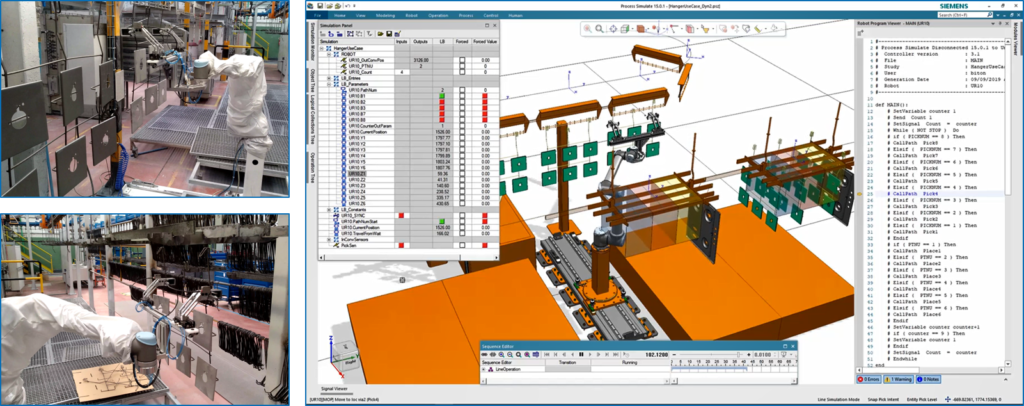
Refrigerator manufacturing line – Using Process Simulate, BSH engineers have evaluated several scenarios for a refrigerator door foaming line that involve the addition of two cobots and a robot. The evaluation combines human and robot simulation in one study. “From my point of view, that’s one of the big advantages that Process Simulate can offer,” Helmke says.
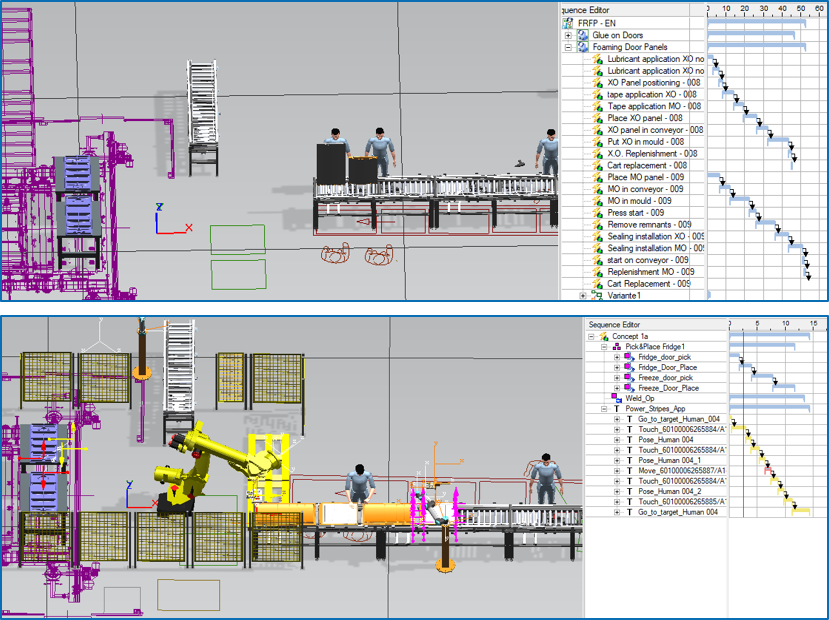
A critical piece of the integrated digital manufacturing system is a plug-in for Process Simulate that automatically generates the code for a specified robot from its library of robotics programs. This functionality opens the door to flexible automation because BSH engineers can modify robot operations without enlisting the help of an external partner. “We can now think about automating single operations, a combination of manual and robot operations, stepwise if needed and in parallel to our classical assembly planning,” Helmke notes.
Digital planning into the future
The integrated digital manufacturing system that BSH has implemented promises to continue improving process efficiency at the company’s factories worldwide. BSH is already benefiting with:
- Streamlined line commissioning
- Optimized cycle time
- Automatic code generation and intuitive programming
- Simulations that verify robot reach locations, collision avoidance, and other automation issues
- Enhanced collaboration through the Teamcenter platform.
BSH has also begun supporting integrated virtual reality (VR) functionality for remote collaboration. They have tested VR collaboration with one engineer in China and another in Germany but interacting in the same virtual space. They will also be able to use VR with external partners.
“Moving the classical digital factory onto Teamcenter and integrating it toward product engineering – that’s the key strategy for us,” Helmke concludes.
Siemens continues to partner with leaders across manufacturing industries to build products and systems that improve sustainability, safety, quality, and compliance, allowing them to better serve their customers, and contribute to a more prosperous world.
—–