Industrial digitalization for robot functional safety at Electrolux

Leading multinational home appliance manufacturer presents the use of Siemens digital manufacturing software for their digitalization journey.
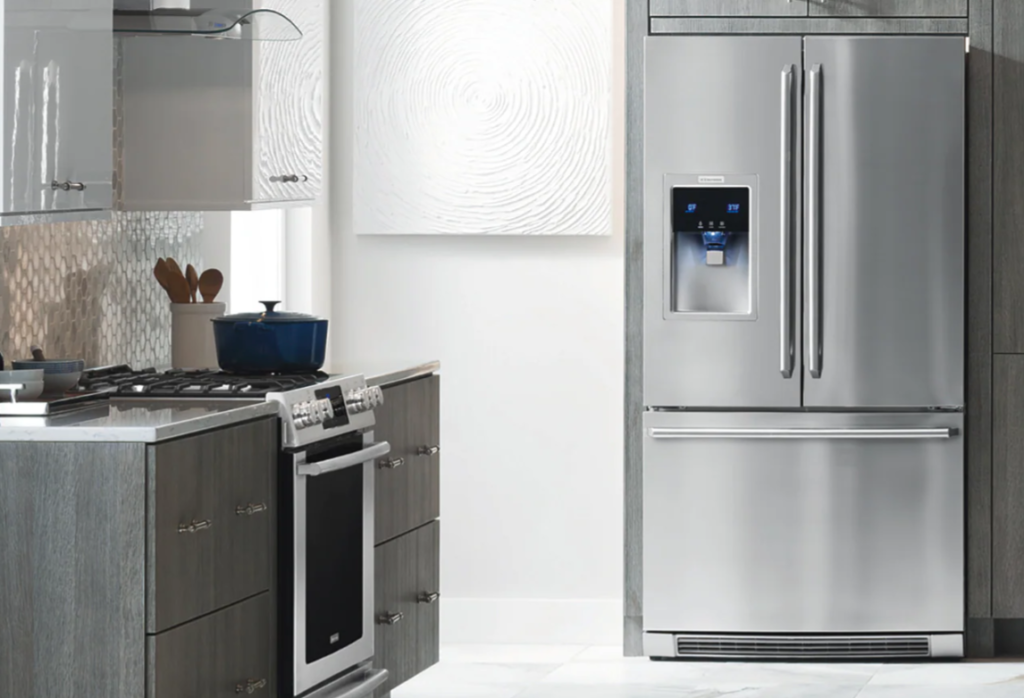
At Siemens Realize LIVE, Electrolux manufacturing engineer and simulation expert Yokesh Kumar presented their industrial digitalization journey using Process Simulate in the Tecnomatix® portfolio. The team works in Electrolux’s Global Manufacturing Engineering Food Preservation division, which manufactures refrigerators. They are responsible for setting up the factory automation all around the world for these products.
Electrolux, a global manufacturing company, has a long relationship with Siemens in digital manufacturing. They use Siemens tools such as NX™ Line Designer software, Process Simulate, and Plant Simulation in the Tecnomatix® portfolio – all making their production planning stronger. Siemens Teamcenter® software has integrated these solutions and established links across all products, creating greater connectivity and accessibility to all information right from the development stage.
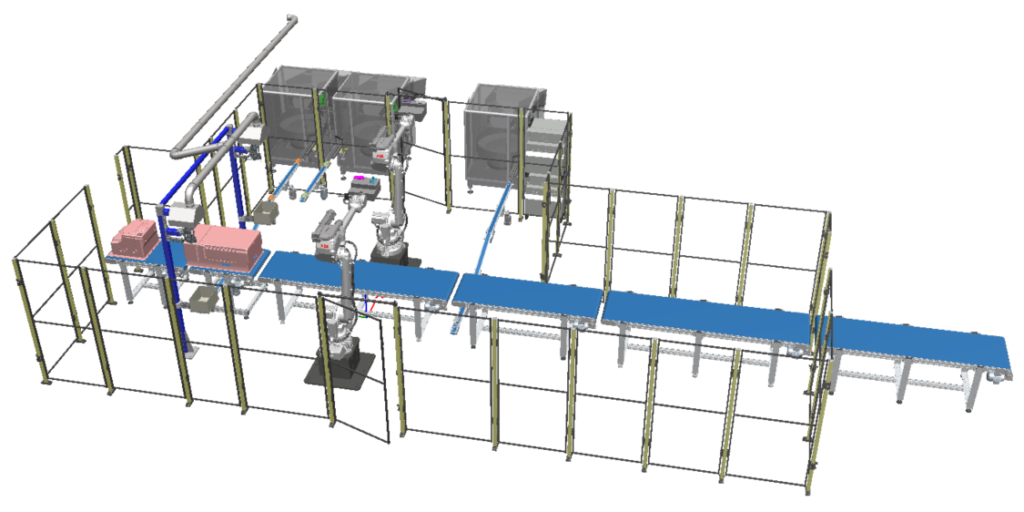
This Electrolux Food Preservation group was challenged with robot functional safety across multiple factories. They needed greater precision with safe move functions and safe operation functions. Their goal was to implement and verify robot functional safety, even at the pre-production stage. Electrolux uses Process Simulate to improve robot safety using the Safety Robots Manager tool. The solution allows them to pre-program their robot safe zones and safe bubbles at a very early stage of production.
The Electrolux team presented their solution with the new Safety Robots Manager feature. They also provided a demonstration and lessons learned through the digital transformation journey. The division uses ABB and KUKA as the major robot brands in the factory.
Safe Operation/Safe Move (the functional safety defined by the ABB and KUKA robots) is to protect the end-of-arm tool on the robot in the surrounding area – creating a safe bubble. The safety controller ensures safety of the robot system using supervision functions that can stop the robot, and monitoring functions that can set safe digital output signals. They are configured and controlled by the signals from the safety PLC (programmable logic controller).
Every robot manufacturer defines their own way of designing the safe zone areas for their robots. Safe zones are the space where the robot is entitled to operate in the specific 3D cartesian coordinate system. Workspace/protected space/switchable space can be designed according to the cell layout. Each zone can have up to 10 corners.
Creating the safe zones and safe bubbles is the hardest part for any robot programmer. ABB and KUKA provide teach pendant/smart pad screens to create these bubbles and safe zones visually. These are used in 2D and 3D software studios to create pre-production scenarios, which are transferred to the teach pendants/smart pads associated with the robots. Yet, it was difficult to see the reality of how the robots would perform in production.
Electrolux wanted to have safe zones created even before going into the commissioning stage. They used Process Simulate for this purpose. Using Safety Robot Manager, a new feature in the latest release of Process Simulate, they were able to create the safe zones and safe bubbles offline, and then transfer those to the factory.
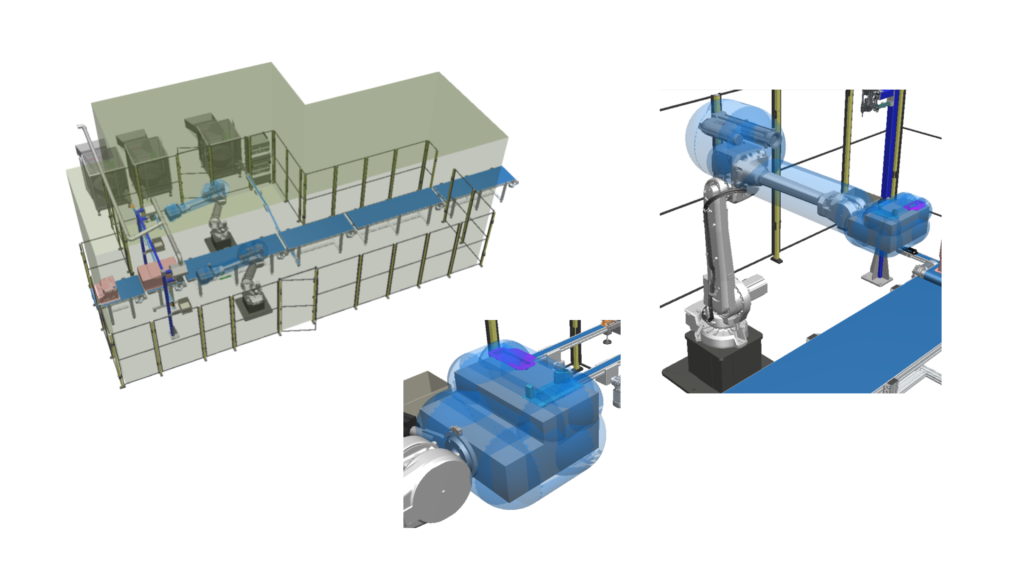
Safety Robot Manager allowed the Electrolux team to set braking before range limits and fixed stop data, with documentation created automatically. They were able to import and export data to the robot teach pendants/smart pads. They could also edit zones and spheres and send those changes back to the factory.
With Safety Robot Manager, all robot brands can be managed in a single application. Electrolux was able to optimize space, create safe velocities, and avoid collisions. The application is integrated with Process Simulate and import and export of safe mode data created perfect interoperability.
Attend future Siemens Realize LIVE events to learn how manufacturers are improving their robot functional safety and see demonstrations of actual simulations using Siemens digital manufacturing solutions.
Comments
Leave a Reply
You must be logged in to post a comment.
Thank you Siemens for sharing my work in Customer Success story.