Leveraging simulation to advance pharmaceutical manufacturing

Miebach Consulting improves efficiency and quality using Tecnomatix Plant Simulation – 7 case study scenarios
Miebach Consulting is a globally recognized name in the supply chain space. Founded in 1973, Miebach’s comprehensive knowledge in pharmaceuticals, medical device, and life sciences, coupled with their service pillars of Supply Chain Transformation, Engineering and Implementation, and Operational Excellence has made them a leader in advancing efficiency and quality across the supply chain.
In the Pharma sector, Miebach has proven their abilities for transformation. In fact, 20 of the top 26 Pharma companies worldwide are clients of Miebach. Across the sectors of R&D, product manufacturing, wholesale and retail, this market has special conditions that add complexity to the supply chain. In the production area, clean rooms, waiting time limitations, batch tracing, and quality control are some of the unique conditions. Further down the value chain, transportation of hazardous substances, traceability of each product, and prescription restrictions further exacerbate the complexity.
Miebach has chosen Plant Simulation in the Tecnomatix® portfolio of digital manufacturing software from Siemens as their standard tool to work with their clients in this space. They site Plant Simulation’s flexibility, object orientation, library concept, and data handling as key advantages over other alternatives.
Case studies in pharma simulation
Dr. Jens Zimmermann, Principal at Miebach, and Markus Nadj, Consultant at Miebach, presented several Pharma case studies at Realize LIVE 2020, Siemens’ global customer event. They span the entire Pharma value chain and reflect the potential improvements that can be achieved by creating a digital twin of the physical system.
Case study 1: Production logistics of a manufacturer of pharmaceutical products
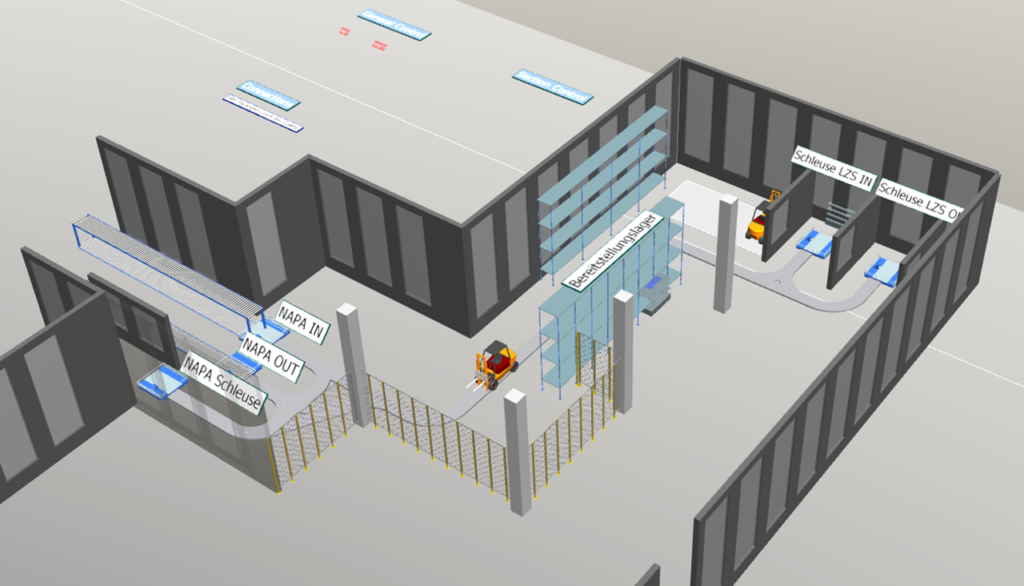
Miebach created a simulation model for the intermediate storage of raw materials, packaging, and finished goods. The model also included the simulation of the transport for production supply and disposal with automated guided vehicles. This simulation brought all these components together to reveal potential efficiencies for the manufacturer.
Case study 2: Production logistics of a manufacturer of pills in blister packaging
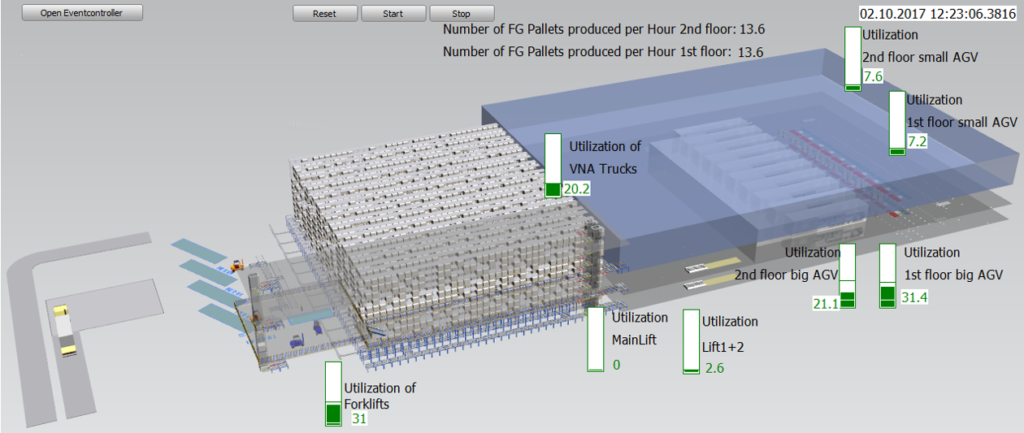
Miebach modeled the storage, kitting process, and production with the production schedule. The model included the production supply and forklift trucks to determine both the number of vehicles required and the utilization of each vehicle. The model had animated processes and was delivered to the customer with a user interface for optimizing the number of trucks and their utilization. As a second phase, Miebach modeled the transports between several production buildings and the central warehouse.
Case study 3: Production logistics of a manufacturer of coronavirus antibody tests
This simulation modeled the production process and the production supply of a manufacturer for the liquids of the Coronavirus antibody test. The model also included the inbound and outbound processes, the storage, and the intralogistics transports with automated guided vehicles and forklift trucks. The unique restriction in this case was that a production batch must complete before the quality control can start, after which the whole batch can be released.
Case study 4: Production logistics of a manufacturer of medications based on blood plasma
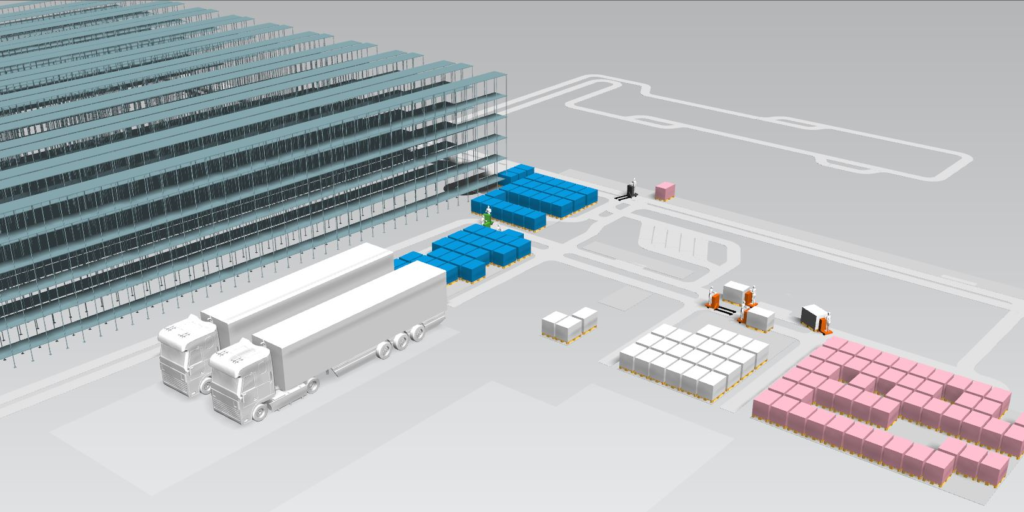
This project simulated the intralogistics processes of a manufacturer of medication based on blood plasma. The model of the production processes with the production schedule was used to determine the picking processes for the raw material and the packaging. The packaging had multiple customer-oriented variations, including size, language, country-specific packaging requirements, all of which were distributed worldwide to wholesalers and the customer’s own distribution centers. The modeling of the storage with stocks of raw materials, packaging, and the intermediate and final products allowed the manufacturer to determine their storage capacity limits.
Case study 5: Production line of a manufacturer of patient individual cancer medications
This innovative project was the first planning of a production line to manufacture these types of medications at scale, moving from the laboratory environment to mass production. The model included patient sample through analyzing and generating the medication in production with continuous quality control. The main goal was to minimize the total processing time and increase throughput, while accommodating waiting time restrictions. The process was further complicated by large variations in the process time and periodic machine breakdowns.
Case study 6: Picking process of a manufacturer of pharmaceutical products
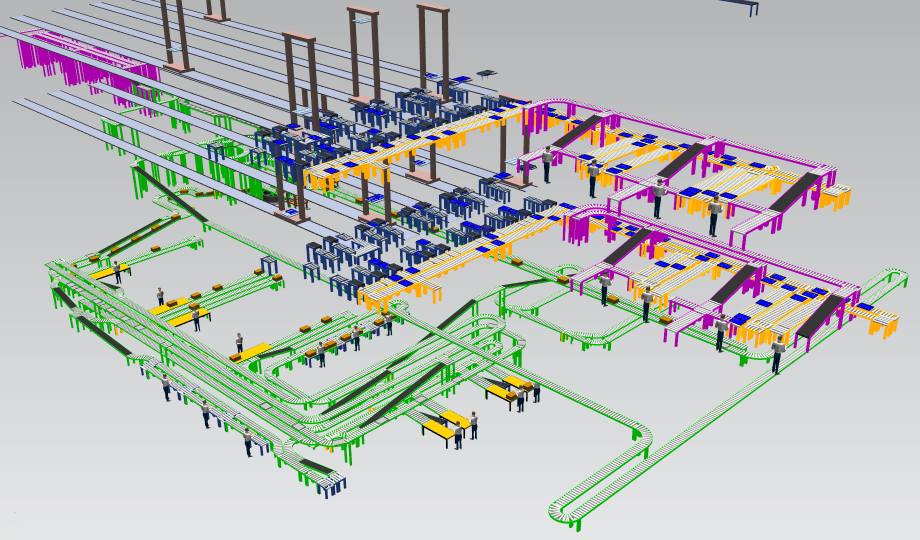
This project simulated the automated picking process for shipping to wholesalers and pharmacies in the concept planning and the realization phase. The model included the storage (concept planning phase as a miniload, realization as a multilevel shuttle) with inbound and picking supply. The model was extrapolated using real data to determine the maximum throughput and to find bottlenecks in the system.
Case study 7: The new warehouse of an online pharmacy
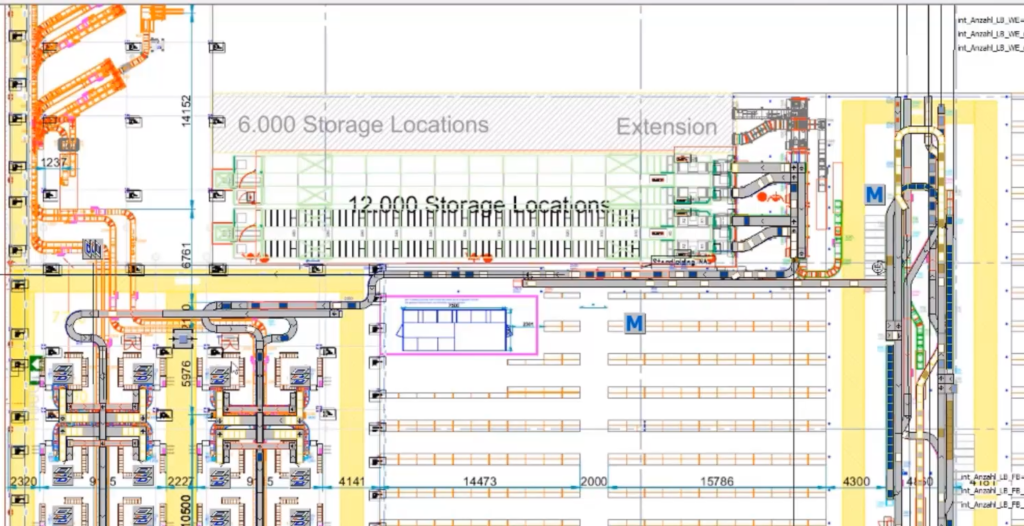
This simulation of the new warehouse included inbound from wholesalers, storing in different storage systems, picking processes of customer-oriented orders, and packaging and shipping to the end customer. The simulation supported the concept planning phase and the adaptation of the model to the realization phase of the supplier. The main goal was to understand throughput and throughput times of custom orders, testing the material flow system on a peak day.
Siemens continues to partner with leaders across manufacturing industries to build products and systems that improve sustainability, safety, quality, and compliance, allowing them to better serve their customers, and contribute to a more prosperous world.
—–