Virtual reality and human simulation at GM

General Motors uses virtual reality and human simulation together to accelerate early issue discovery and improve team communication
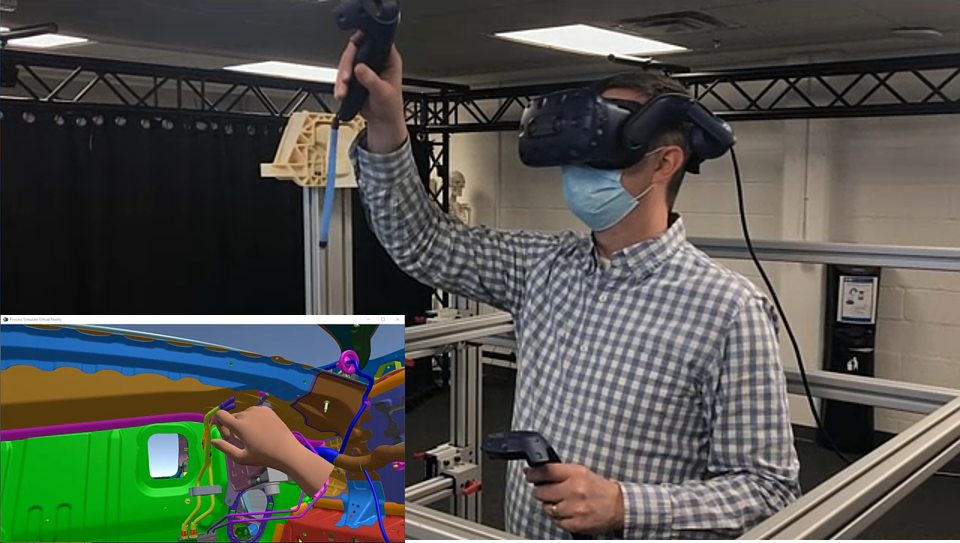
Virtual reality (VR) is an exciting technology that is proving to deliver real results across manufacturing industries. In particular, the application of VR in manufacturing process simulation is enabling the early identification of issues by allowing engineers to become immersed in their designs at one-to-one scale, discovering and solving problems before physical resources are spent. Integrating the results of VR simulation in the process workflow allows for the communication of issues effectively across physically separated teams. Because mastering VR is simple and intuitive, the technology is becoming rapidly adopted for industrial use.
Ryan Porto, Technical Specialist Ergonomics at General Motors, and Jonathan Botkin, Senior Program Ergonomist at General Motors, presented their application of VR using Process Simulate in the Tecnomatix® portfolio of digital manufacturing software from Siemens at Realize Live, Siemens’ global user conference. This blog summarizes their presentation and shows how VR is advancing efficiencies in the automotive industry.
Virtual reality and human simulation at General Motors
The Global Ergonomics Lab in Manufacturing Engineering at General Motors (GM) is currently conducting VR sessions using Process Simulate. The Ergonomics team uses VR to immerse product and manufacturing engineers in their designs, giving them visualization of a variety of advanced assemblies and operations in a 3D environment.
The focus of the immersive studies is to evaluate human reachability, line of sight, accessibility, and hand clearance. Immersive technology has enhanced human simulation studies during the vehicle development process for the design of safer workstations. It has also increased collaboration between product engineering and manufacturing engineering to reduce late design changes in the product lifecycle.
Virtual reality simulation
The GM team showed several video examples of how they are leveraging VR in their ergonomics lab. In one case, a subject interacts with an aluminum structure simulating the barrier and boundary awareness. The simulation mimics the hard points of a vehicle and simulates reach constraints.
The GM team added 3D printed parts to represent exact dimensions to assess accessibility and line of sight of the team member. The immersive technology helps them improve the skillset of program ergonomists and allows the ergonomist to validate their simulations in a 3D environment from a third-person point of view.
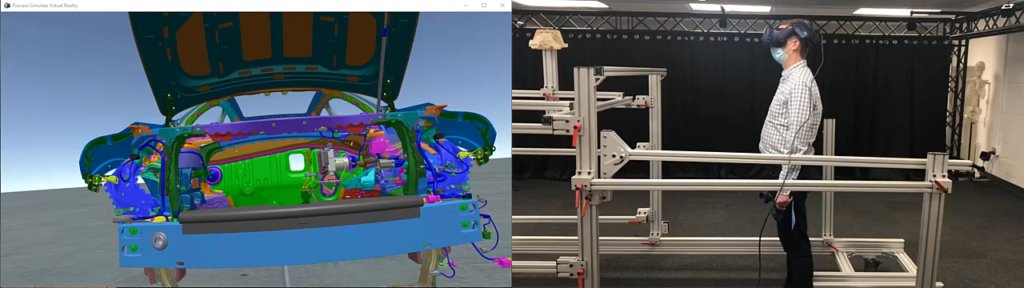
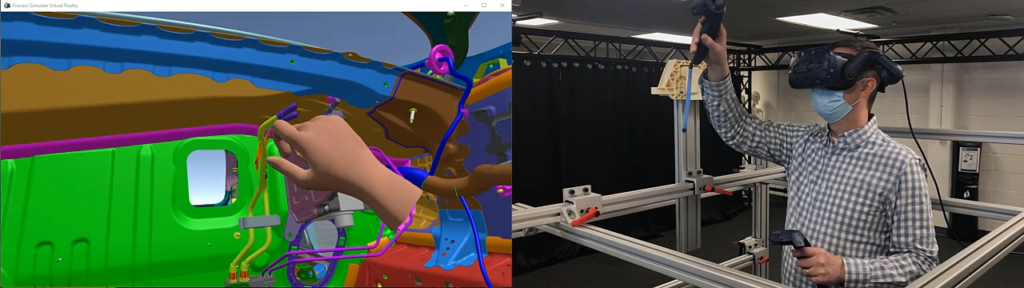
Included in the simulation is the Process Simulate “live hands” module, which gives a close-up understanding of manual assembly and hand clearance. Real-time measurement is available with an interactive ruler in the scene. Markup capabilities identify issues for the audience, and issue tracking is facilitated with notes to capture and document the issue description and record screenshots.
Virtual Reality in Process Simulate provides a realistic representation of an operation when the current plant or process does not exist today. It helps ensure consistency and reliability between evaluations across multiple programs.
Motion capture capabilities
The GM team leverages motion capture capabilities provided in Process Simulate. They use an inertial motion capture solution to record the task of a female operator as she ducks under the impact beam and enters the engine compartment. Using a larger male operator, motion capture can be used to compare how a larger anthropometry would enter the engine compartment. The team can evaluate the duck under height to ensure there is accessibility to the compartment and analyze the accurate posture of a future task or operation. Motion capture enables the integration and interaction with physical structures and 3D printed parts and assemblies.
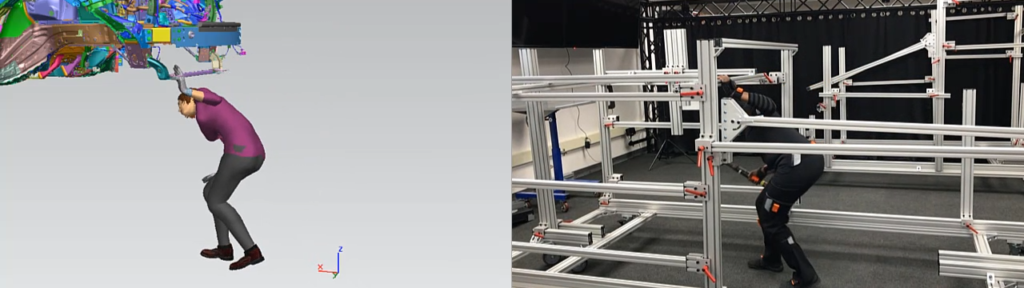
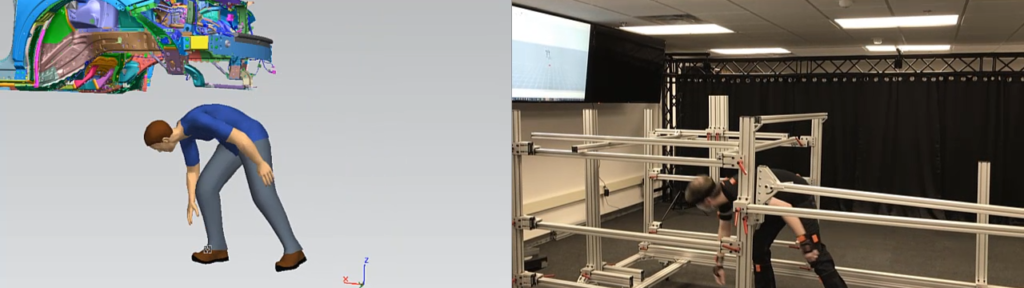
With motion capture playback, GM ergonomists can pause and evaluate the low back compression of a specific posture, and the time spent in a particular awkward posture. They can capture these poses and save them into the posture library for re-use.
Virtual reality live hands
The live hands feature of Process Simulate Virtual Reality allows the ergonomist to envision hands scaled and postured from the Process Simulate posture library. They are then able to do general hand clearance studies, validating simulations moving objects in an assembly sequence, as outlined by the manufacturing process.
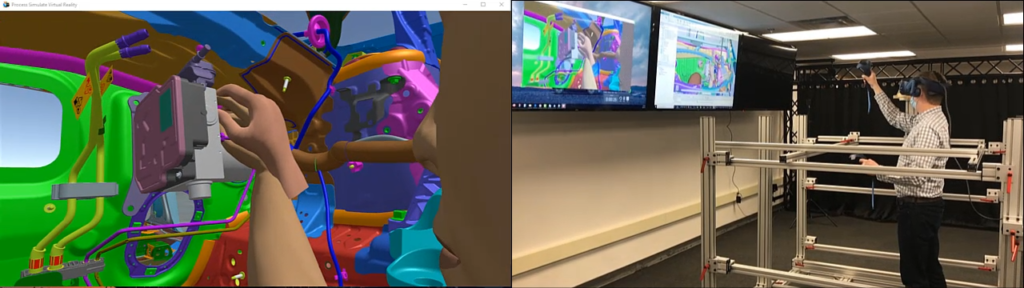
Virtual reality line of sight
The 3D assessments in Virtual Reality allow validation of operator line of sight. For example, the GM team can see the manikin line of site to determine whether the operator could see the fittings on the brake apply module. They are then able to leverage VR to find alternative postures that were not previously considered and now provide adequate line of sight.
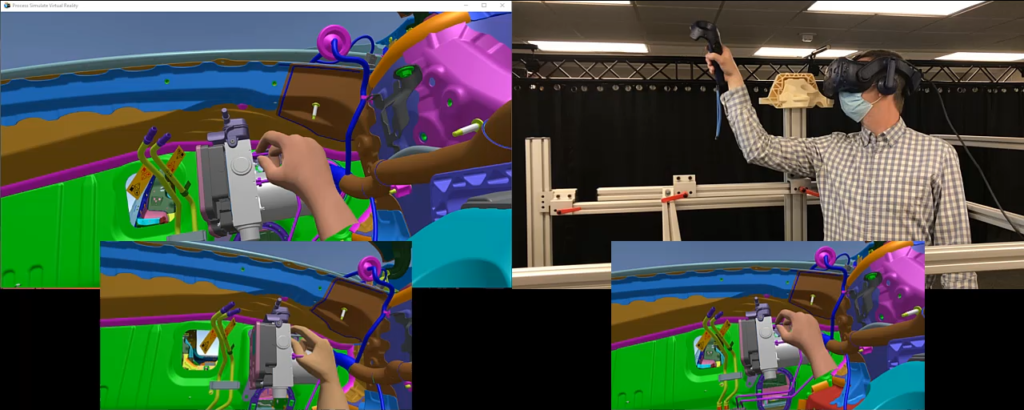
Collaboration within the VR module
In addition to the improvements of human simulation, VR has also brought tremendous value to collaboration across several groups at General Motors. During a time when working remotely has significantly increased, they have still been able to safely collaborate with key stakeholders such as designers, plant representatives, and product and manufacturing engineers. They are sharing immersive sessions and demos virtually through portals such as Microsoft Teams or Zoom. Rather than creating physical mock-ups from scratch, new vehicles can be reviewed by the members of the plant virtually.
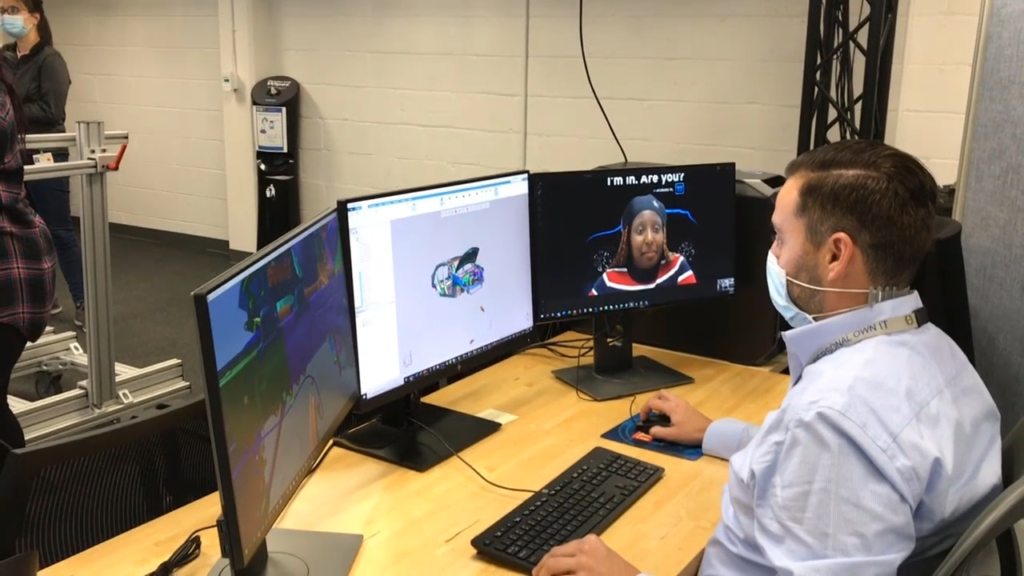
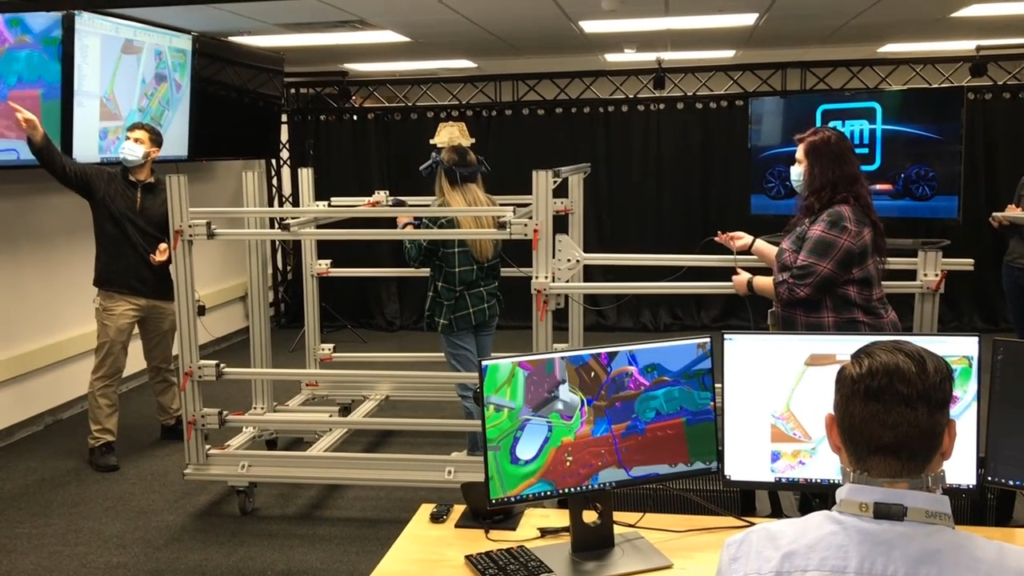
Future of virtual reality at General Motors
The GM team plans to expand their use of virtual reality. They envision improving the accuracy of a motion capture solution (optical or inertial) in the virtual reality environment to evaluate and enhance the first-person capability. Replacing VR controllers with VR gloves for a more realistic experience when grasping parts is also on their roadmap, as well as the ability to enhance haptic feedback for collision and grasping.
—–
Don’t have Tecnomatix software? Try Process Simulate Human for free.