Smart Factory – The Factory of the Future
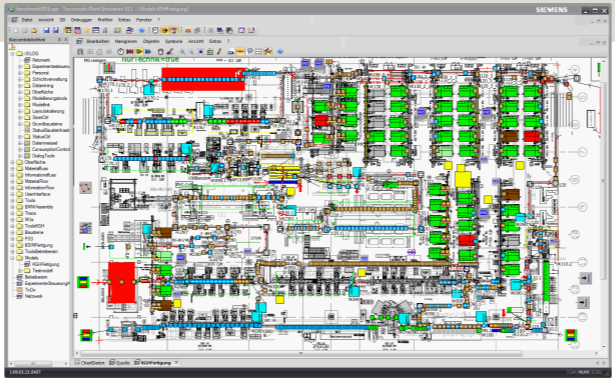
By: Zvi Feuer and Zvika Weissman
Developed countries are investing a lot of effort to advance the concept of the Smart Factory. They expect that this will enable them to maintain superiority of production efficiency and keep production jobs.
But what is a Smart Factory?
In this post, we will focus on the details and review some of the concepts that help make a factory – a Smart Factory. The breakthrough strengths of the Smart Factory are shop floor connectivity, advanced robotics, flexible automation, automation standards, virtual reality and augmented reality incorporation and energy management.
Smart Factory
A Smart Factory is a fully digitalized factory model representing a production system, a digital twin for production, which is completely connected to the main PLM data repository via sensors, SCADA systems, PLCs and other automation devices. In such a smart factory, all the events happening on the shop floor during production are recorded and the relevant ones are pushed back to the PLM system either directly or through the cloud.
The shop floor is an integral part of the digital thread, using one communication and automation standard through all manufacturing technologies allowing plug and use. These will be highly energy efficient factories with integrated energy monitoring to allow a self-adjusting decision making process. Artificial Intelligence (AI) technology studies the information the digital thread renders, analyzes it and sends its main findings back to product development, manufacturing planning or facility planning.
One application that is a big enabler of the Smart Factory is Intosite, a cloud-based application for sharing digital manufacturing and production information in a 3D context. Intosite fosters collaboration and cooperation between departments and disciplines based on a simple, intuitive user experience.
Intosite is a cloud-based application that provides smart map navigation of virtual factories around the globe enabling collaboration through the use of key manufacturing data, such as this production performance chart accessed from a tag on a machine.A Smart Factory is based on a set of manufacturing concepts such as full connectivity, flexibility, agility, lot size of one, parts, sub-assemblies and products moving on automated guided vehicles (AGVs). With no pre-defined route, the AGV moves from station to station, based on the manufacturing process plan, but can re-plan its next location of production/machine and assembly/inspection station, based on availability.
At any point in time, the AGV recalculates, on the fly, the trip to its next production location, while the necessary electronic work instructions will be sent to that new location dynamically, in the course of operations. Robot, machine or 3D printer instructions will upload to the next station and wait for the new job to arrive. The same is true for cutting tools, fixtures, jigs or any other production resource needed for the next production step.
This is a KARIS AGV equipped with a vision system and artificial intelligence (AI). It communicates with the factory’s Manufacturing Operations Management (MOM) system and negotiates with other AGVs to determine its next task and route.
This is Siemens Tecnomatix Plant Simulation software simulating a factory operation with KARIS AGVs. The goal of this simulation is to optimize the number of AGVs as well as the number of charging stations needed (and their locations) to meet production demand.
All production devices will be fully connected and will communicate, at the minimum, their location, status (working, waiting or blocked), temperature or humidity, etc. In cases where the production system is a computer controlled machine or station, the information could be much richer. In cases where the station is a manual station, or set on an OLD machine, the information will be collected via attachable sensors.
To make the system as flexible as possible, resources will be able to communicate with other resources, parts, sub-assemblies and products. In this future factory, each product will carry a chip that stores all relevant production and quality inspection information. When that product arrives at a station, the product’s chip will transmit the process that needs to be executed, the tool, fixture and machine programs to be used, as well as other necessary raw materials or parts and required worker skills.
Also, some of the production resources will be located on top of moving platforms. This will further increase flexibility because it will enable, when needed, bringing the resources to the part or product. For example, a computer numerical controlled (CNC) robot could be placed on a moving AGV platform, to send the robot to the right location to perform a machining or a polishing operation without needing to move the part or product from its current location.
In such a case, it will be possible to 3D print a part or subassembly, and it will be possible to finish the job to perfection by sending a robot to perform the finishing operation, right after the 3D printer finishes creating the part.
The part on the left is designed for conventional machining. The organic shaped part on the right has been optimized for additive manufacturing with reduced mass and equal strength. New Siemens additive manufacturing solutions with generative design and simulation technology yield reimagined parts like the one on the right with topology optimized shapes for performance and weight.
A cloud-based Manufacturing Operational Management (MOM) system will collect information from resources, enabling a much better and more adaptive factory maintenance system and processes, thus ensuring high uptime and better productivity.
The information collected during production from the process, from the part or product and from the production resources, will be shared with the product design and manufacturing planning departments. It will help to improve the product, make the manufacturing process more robust, and also help the production management people identify best practices, by comparing production processes in different plants around the globe.
In the Smart Factory, people will work alongside cooperative robots (co-bots), which will have more sensors and become more human-aware. Robots with vision systems and artificial intelligence (AI) will be able to perform autonomous tasks, move to new locations, replicate work done by humans and adapt to evolving situations, such as changes to the position of parts or products.
Siemens is exploring ways to virtually model and plan human-robot interactions using a digital twin within its Tecnomatix Process Simulate software to better assess risk of tasks and environment for safety regulation compliance.
Learning at the Smart Factory will be facilitated by the use of virtual reality (VR) devices. These devices will enable production employees to walk through the production lines, inside the production systems, in a virtual manner – well before they will be installed on the shop floor. Using these VR tools, maintenance crews will be trained how to maintain these quite complex manufacturing systems, while the production teams will be able to learn how to use the systems and execute the production tasks.
Once the production line is established, shop floor workers will be able to use augmented reality (AR) techniques, which will guide them through the production process, project process animations, as to the next needed production step, on the real part or product, and validate that workers executed the process correctly. Using such capabilities, workers will also be able to maneuver robots and assistors that can get to spots not reachable by workers and conduct manufacturing work at those spots.
Siemens is exploring ways to use VR/AR environments to create and deliver more meaningful electronic work instructions for shop floor operators, such as this assembly sequence created in its Tecnomatix Process Simulate software shown using Microsoft’s HoloLens.
All changes on the shop floor will be recorded automatically and uploaded via the MOM system to the main PLM repository, such as Siemens Teamcenter. Once the manufacturing engineer and production system design teams are asked to develop a new process for launching a new product on an existing line, they will be able to do so with minimal loss of data.
BMW Motoren GmbH, the biggest engine plant within the BMW Group located in Steyr, Austria reduced their lifecycle energy consumption of car engines and eco-footprint by 550 tons of CO2 equivalents per year following energy simulation using Siemens Tecnomatix Plant Simulation software.
Key measurements of Smart Factory performance are energy efficiency or the minimization of CO2 emissions during production. The energy aspect will be taken into account at the design phase via the use of smart simulation models, which will help to identify ways to reduce energy consumption and CO2 emissions already during design, and during the operation phase.
Siemens has tools that can be deployed today that can provide accurate energy and CO2 data during production.
Closing the loop from real to virtual can help a manufacturing company achieve a high level of continuous improvement, over time.
This concludes our introduction to the Smart Factory.
About the authors
Zvi Feuer is senior vice president of Manufacturing Engineering Software for Siemens PLM Software, a business unit of the Siemens Digital Factory Division. He has more than 25 years of experience in enterprise software business management, with a primary focus in the manufacturing industries. He has worked for: the Israeli Aircraft Industries (IAI); Digital Equipment, a leading provider of hardware and system integration projects; and since 1995, with Tecnomatix, UGS and Siemens. Feuer’s current responsibilities include leading global teams and initiatives to develop and service customers worldwide and providing manufacturing engineering software solutions. These solutions include optimizing production and service facilities, assembly line design, developing and validating production systems and programming CNC machines in major machine shops. Feuer received his Master of Science degree in industrial engineering from Technion Israel Institute of Technology, and also received an executive MBA from UCLA – NUS.
Zvika Weissman has more than 15 years of experience in the PLM market, dealing with digital manufacturing software business development, marketing, engineering and support. He is currently the aerospace and defense Business Development Director, in the Siemens Industry Software Manufacturing Engineering Software Solution segment. In his previous role, Weissman helped deploy digital manufacturing tools within leading automotive, aerospace, machinery and consumer goods companies in the U.S., Europe and Asia-Pacific. In this role, he gained special expertise in using digital manufacturing planning and simulation tools such as Teamcenter Manufacturing Process Planner, Process Designer, Robcad, Process Simulate and Plant Simulation. He analyzed companies’ business and engineering processes and developed workflows to be established as part of the companies’ continuous improvement processes. Weissman holds Bachelor of Science and Master of Science degrees in Mechanical Engineering from Technion Israel Institute of Technology, and a Master of Business Administration degree from Tel-Aviv University.