Manufacturing quality’s role in a future-proof business
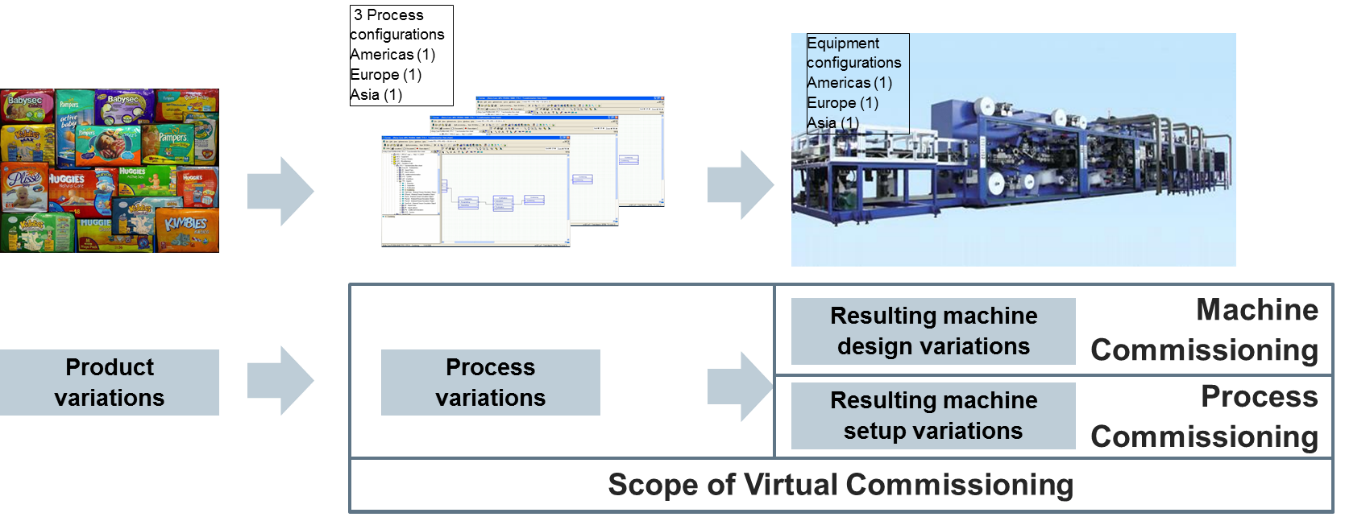
Imagine we run a company that makes a popular, useful and necessary product. It’s something all parents have used at one point in time: diapers.
All companies that manufacture diapers, including our competitors, can only innovate the diaper so much. Eventually, the companies producing the diapers will reach a point where they’re at a level playing field and everyone’s products are virtually the same.
So what does your company do to get ahead? The competitive edge is no longer in the product at that point, but in the manufacturing quality of the processes and production machines used to create that product. These machines must be able to respond and adapt to planned and unexpected changes. And, these machines must be able to respond to changes in product requirements, raw materials and regional regulations.
If we look at a product such as the diaper, we see that the product itself has likely reached its limits with innovation. There simply aren’t many breakthrough innovations left to make with the diaper’s overall design.
But the production machine that a company uses to manufacture the diaper is what could make your company more competitive in the market.
Why would you be more competitive? Because the machine you’ve designed executes a production process that has higher quality, reliability and productivity that none of your competitors can reach. And because the process is more efficient, your price gives you an edge over your competition.
This is not a fictional story. We work with a partner company that produces consumer goods, and it has completed this work on its manufacturing processes to get ahead of the competition. By doing this work, it created a system that can adapt to new changes in the market. The company can quickly respond to unexpected surprises it encounters in the marketplace.
This question of improving your own manufacturing quality situation will eventually occur with every product of yours that hits the market. Are you prepared to answer?
Improve manufacturing quality for a competitive edge
There is only so much innovation a company can execute with its products. These innovations may put you ahead in the market for a time, but you will reach a point where your products are virtually the same as your competitors’ products.
When that happens, that’s when you need to take your innovation to the next level.
The market is fast approaching that point. Due to a number of factors, including increased product personalization and the Industrial Revolution we’re entering into, the market is a volatile place where product innovation is no longer enough to guarantee success.
If you want to survive this new kind of ultra-competitive and even volatile market, your manufacturing process must also become innovative. It can no longer be a rigid, inflexible process. Instead, the process must include high manufacturing quality that can adapt and account for different variables. How do you make continuous breakthroughs with your machines to accomplish this?
The answer is quite complex, but virtual commissioning is an incredibly important part of it.
To survive a new kind of competitive and often volatile market, you must innovate your manufacturing process.
Virtual commissioning and manufacturing quality
Virtual commissioning is the process of validating a device for its intended use in the context of its operational environment by using its digital model without involving the physical device.
The term ‘virtual commissioning’ is derived from the conventional form of commissioning, which was introduced to perform final tests on completed systems as to put the entire system into service without major problems.
Conventional commissioning is performed in the final stages of a real machine or system immediately before its use, so a design change is limited to the data that controls the system’s functionality, the behavior of the PLC-code and the on-board software.
These were the only variables that could be modified to optimize the performance and debug the behavior of the system. With virtual commissioning, you can break these borders and open up the possibilities to complete these tasks much earlier, even before the machine itself exists.
Virtual commissioning was understood to be the process for final tweaks in an automation system’s software, which means you can perform the commissioning tasks without occupying the real system.
However, the availability of the multi-disciplinary properties of the system already in the design phases, such as mechanics, electrics and automation, widens the horizon of achievable tasks in very early phases of the system’s creation.
This is the scope of virtual commissioning based on product and process variations.
With virtual commissioning, it isn’t just about mechanical design or software or logic. All disciplines that define the operational properties of a machine or a system need to be considered holistically in an associative manner. It’s the responsibility of virtual commissioning tools to validate the functional integrity of the commissioned system in context of the target process.
Consider what happens if you produce a product and something changes. These changes can be sudden, but they’re often expected changes, especially if there is new business or if you need to adapt to new regions. You want to respond to those changes quickly, but you also don’t want to disrupt production or endanger your manufacturing quality. With these changes, you also want to ensure your product and manufacturing process is secure in diverse environments.
With virtual commissioning, you can start working on the change in the product which would lead to the change in your production processes as soon as you receive signs of change in market. Why? Because all this work can happen in parallel – on the virtual side – to your real production systems. You can mature the process and you can do it quickly.
Virtual commissioning plays an important role in numerous stages of a system’s lifecycle, and it can help you improve your manufacturing quality so you can get ahead – and stay ahead – of the competition. In this series, we’ll cover the different roles of virtual commissioning during the design and in pre-delivery stages of a machine and in its phases of operation after the delivery at a target plant.
This concludes part one of our introduction to virtual commissioning. In part two, we take a closer look at virtual commissioning’s role in how production systems are designed.
About the author
Dr. Nezih Yaramanoglu is the Program Manager of two major cross organizational research and development programs in Siemens Product Lifecycle Management, with the scope on Digital Enterprise and end-to-end machinery production solutions. His focus is on industry processes and their influences on IT solution architectures. Nezih has more than 36 years of experience in IT Solution research and development for production processes. Prior to his current role, he provided development support in initiating and leading strategic Digital Manufacturing projects. He co-founded the e-Factory organization of UGS in 2001 and led the dCADE PBU of UGS Products organization, which merged with Unigraphics Solutions GmbH in 1999. Before the merger, he was the President and CEO of dCADE GmbH, which he co-founded in 1991. Nezih’s academic background is in mechanical engineering. He received a Ph.D. in production engineering from Technical University of Berlin, Germany, where he also received his Master’s degree in biomedical engineering.